Business inventory barcode system office equipment represents a significant advancement in streamlining operations and enhancing efficiency. Implementing a barcode system for tracking office assets offers numerous benefits, from minimizing loss and theft to optimizing purchasing decisions and improving overall asset management. This comprehensive guide explores the intricacies of establishing and maintaining such a system, covering everything from selecting the right barcode symbology to integrating the system with existing software platforms and leveraging advanced features like RFID tracking.
We’ll delve into the practical aspects of implementation, including hardware and software considerations, step-by-step barcode assignment procedures, and the creation of effective inventory tracking spreadsheets. Furthermore, we’ll examine data management strategies, reporting techniques, and the potential return on investment associated with this technology. Understanding these elements is crucial for any business seeking to optimize its office equipment inventory management.
Introduction to Business Inventory Barcode Systems for Office Equipment
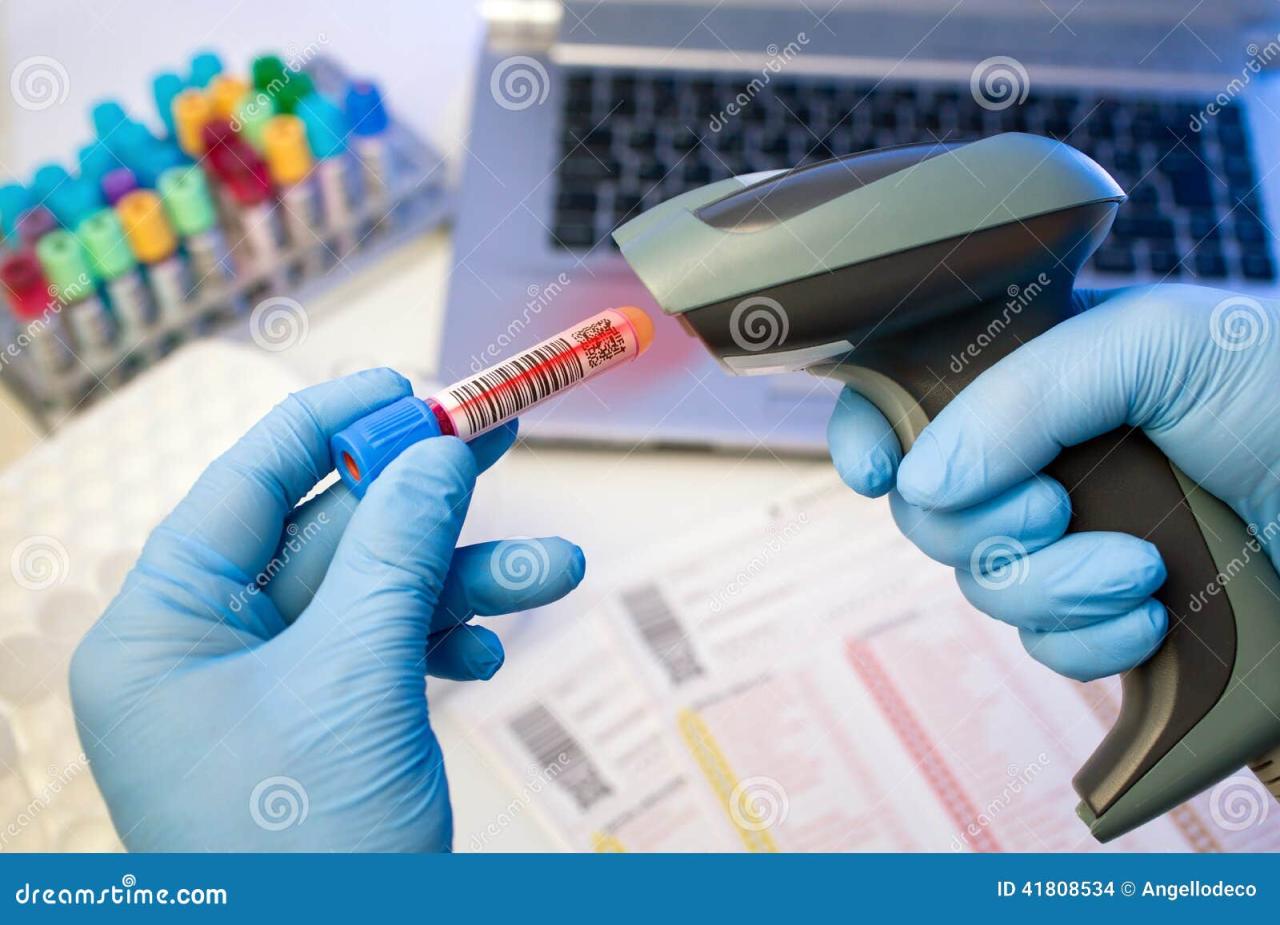
Efficiently managing office equipment is crucial for any business, ensuring smooth operations and minimizing downtime. A barcode inventory system offers a streamlined and accurate method to track and manage this equipment, providing significant benefits over manual methods. Implementing such a system can lead to substantial improvements in productivity and cost savings.Implementing a barcode system for office equipment inventory offers several key advantages.
Real-time tracking capabilities allow for immediate identification of assets, simplifying the location process and reducing time spent searching for specific items. This improved efficiency translates directly into increased productivity for employees. Furthermore, accurate inventory data minimizes the risk of overstocking or understocking, optimizing resource allocation and reducing unnecessary expenditure. Automated tracking also helps prevent loss or theft, as each item’s location and movement can be monitored and recorded.
Finally, the data generated by the system provides valuable insights for informed decision-making regarding equipment purchasing, maintenance, and replacement cycles.
Barcode Symbologies Used in Office Equipment Inventory Management
Several barcode symbologies are suitable for tracking office equipment, each with its own strengths and weaknesses. The choice depends on factors such as the amount of data needed, the quality of the barcode scanner, and the environment in which the barcodes will be used. Commonly used symbologies include Code 128, which is widely compatible and capable of encoding a large amount of data, and EAN-13, frequently used for retail products and also suitable for larger office equipment items.
Code 39, while less efficient in data capacity, offers good readability and is simple to implement. Data Matrix symbology, a two-dimensional code, is increasingly popular due to its high data density and resistance to damage. The selection of the appropriate symbology is a critical aspect of system design.
Examples of Office Equipment Benefiting from Barcode Tracking
Many types of office equipment can benefit from barcode tracking. This includes computers (desktops, laptops, and servers), printers (laser, inkjet, and multi-function), scanners, copiers, projectors, telephones (desk phones and mobile devices), and other peripheral devices such as keyboards, mice, and monitors. Even smaller items, such as power supplies or network cables, can be tracked effectively using barcodes, providing a complete inventory of all office assets.
Tracking these items with barcodes allows for comprehensive management and control of the entire office equipment inventory.
Implementing a Barcode System
Implementing a barcode system for your office equipment offers significant improvements in inventory management, reducing time spent on manual tracking and minimizing the risk of loss or misplacement. This process involves careful planning and execution, encompassing hardware acquisition, software selection, and the systematic assignment of barcodes to each piece of equipment.The successful implementation of a barcode system hinges on a well-defined strategy.
This includes assessing your current inventory, selecting appropriate hardware and software, and establishing a clear procedure for barcode assignment and data entry. Failure to adequately plan can lead to inefficiencies and ultimately negate the benefits of the system.
Hardware and Software Selection
Choosing the right hardware and software is crucial for the efficient operation of your barcode system. Hardware requirements typically include barcode scanners (either handheld or stationary), a computer or server for data storage and management, and potentially a printer for generating barcode labels. Software options range from simple spreadsheet programs with barcode integration to dedicated inventory management systems offering advanced features like reporting and analytics.
Consider factors such as the size of your inventory, budget constraints, and desired level of functionality when making these selections. For example, a small office might suffice with a handheld scanner and a spreadsheet program, while a larger organization may require a more robust system with multiple scanners and dedicated inventory management software.
Step-by-Step Barcode Assignment
A structured approach to barcode assignment ensures accuracy and consistency. The following steps Artikel a recommended procedure:
- Create a comprehensive inventory list: This list should include a detailed description of each piece of office equipment, including its make, model, serial number, and location.
- Generate barcodes: Use barcode generation software to create unique barcodes for each item on your inventory list. Many free and paid options are available online. Ensure the chosen software can generate barcodes in a format compatible with your scanner.
- Print barcode labels: Print the generated barcodes onto durable labels suitable for affixing to the office equipment. Consider using labels resistant to wear and tear, especially for items frequently handled.
- Attach labels to equipment: Carefully attach the barcode labels to a visible and easily accessible location on each piece of equipment. Avoid placing labels in areas that might be easily damaged or obscured.
- Scan and verify: Scan each barcode using your barcode scanner to verify that the system correctly reads the data. Correct any errors promptly.
Inventory Tracking Spreadsheet
A well-designed spreadsheet can effectively track your office equipment using barcode data. The following table provides a simple example, adaptable to your specific needs.
Barcode | Item Description | Location | Status |
---|---|---|---|
123456789012 | HP LaserJet Pro MFP M428fdw | Office A, Room 2 | Active |
987654321098 | Dell OptiPlex 7070 | Office B, Room 1 | Active |
135792468013 | Lenovo ThinkPad T14s | Office A, Room 1 | Maintenance |
Data Management and Reporting
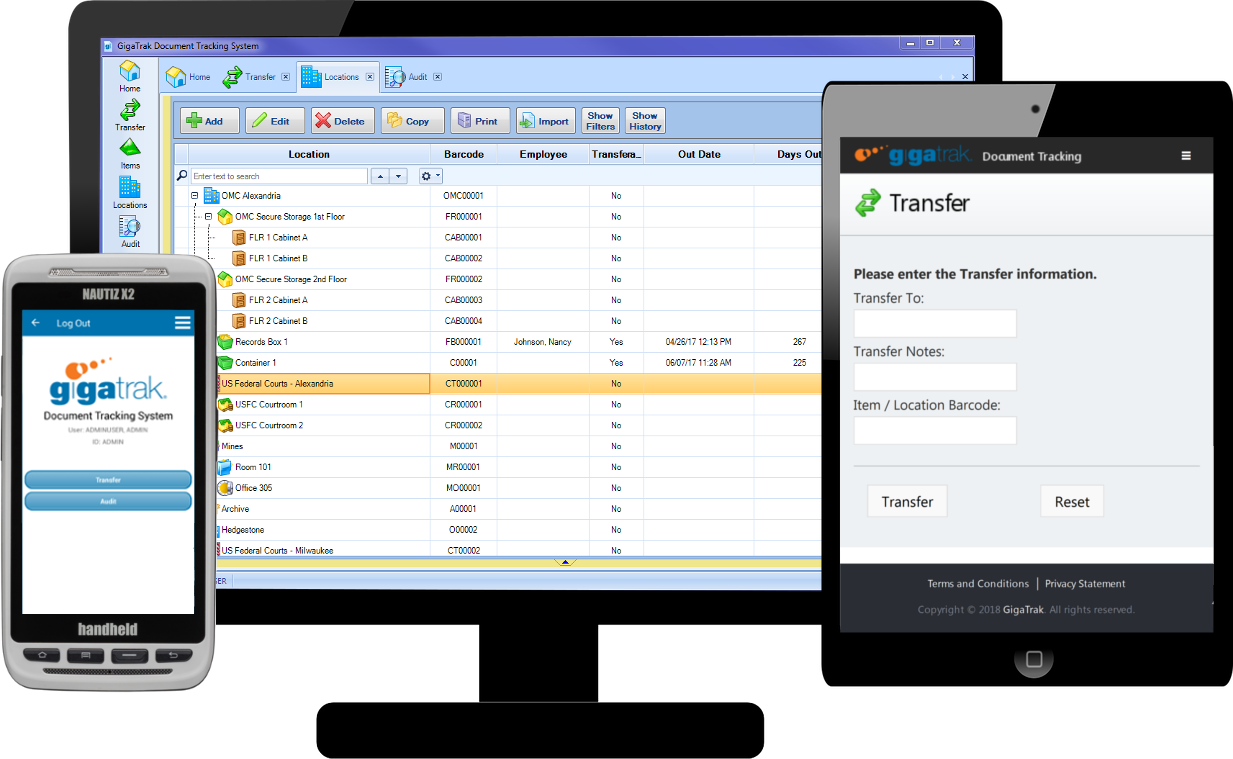
Efficient data management is crucial for maximizing the benefits of a barcode inventory system for office equipment. A well-structured system allows for quick retrieval of information, streamlined reporting, and informed decision-making regarding equipment acquisition, maintenance, and disposal. This section explores effective data storage and management techniques, along with the types of reports that can be generated and how barcode data can be leveraged for comprehensive equipment tracking.Effective data management hinges on selecting the right database software and implementing robust data entry procedures.
Database software can range from simple spreadsheet programs like Microsoft Excel (suitable for smaller inventories) to sophisticated database management systems (DBMS) like MySQL or PostgreSQL (more appropriate for larger organizations with complex inventory needs). Regardless of the chosen software, consistent data entry practices are paramount to ensure accuracy and reliability. This includes employing standardized naming conventions for equipment, using consistent units of measurement, and regularly verifying data accuracy.
Database Software Selection and Implementation
The choice of database software should align with the scale and complexity of the inventory. Spreadsheet software provides a simple, cost-effective solution for smaller inventories, allowing for basic data entry, sorting, and filtering. However, for larger inventories with numerous data points and complex reporting requirements, a dedicated DBMS offers greater scalability, security, and data management capabilities. These systems offer features such as data validation, user access control, and advanced query capabilities for efficient data retrieval and analysis.
For example, a company with hundreds of pieces of equipment might benefit from a DBMS’s ability to handle large datasets and generate complex reports, unlike a spreadsheet program that might become cumbersome and prone to errors.
Report Generation
The power of a barcode inventory system lies in its ability to generate insightful reports. These reports provide valuable information for various business functions, aiding in inventory management, budget planning, and equipment lifecycle management.
- Inventory Summary Report: Provides a comprehensive overview of all equipment, including quantities, locations, and condition.
- Low Stock Report: Identifies items nearing depletion, enabling timely procurement and preventing disruptions.
- Equipment Location Report: Shows the current location of each piece of equipment, facilitating efficient asset tracking and retrieval.
- Equipment Usage Report: Tracks equipment usage frequency and duration, helping to identify underutilized or overused assets.
- Maintenance Report: Schedules and tracks preventative and corrective maintenance activities, ensuring equipment longevity and minimizing downtime.
- Depreciation Report: Calculates the depreciation of equipment over time, providing valuable data for financial reporting and asset management.
Tracking Equipment Usage, Maintenance, and Depreciation
Barcode data provides a robust mechanism for tracking equipment throughout its lifecycle. By scanning barcodes during check-in/check-out processes, usage patterns can be easily monitored. This data can then be used to optimize equipment allocation, identify underutilized assets, and inform procurement decisions. Similarly, integrating maintenance records with barcode data allows for efficient tracking of service intervals and repair history.
This data can be utilized to predict potential equipment failures and schedule preventative maintenance, minimizing downtime and extending equipment lifespan. Depreciation calculations can be automated by linking barcode data with initial equipment cost, useful life, and chosen depreciation method (e.g., straight-line, declining balance). This ensures accurate financial reporting and facilitates informed decisions regarding equipment replacement or upgrades. For example, tracking the usage of a particular printer might reveal that it’s consistently overworked, requiring more frequent maintenance or prompting a decision to purchase a more robust model.
Integration with Existing Systems
Seamless integration of your new barcode system with your existing business software is crucial for maximizing efficiency and avoiding data silos. A well-integrated system allows for automated data transfer, minimizing manual data entry and reducing the risk of errors. This section will explore various integration methods and address potential challenges.Integrating a barcode system with existing accounting or asset management software streamlines workflows and improves data accuracy.
For example, when an item is scanned, the system can automatically update inventory levels in your accounting software, eliminating the need for manual updates and reconciliation. Similarly, asset management software can be updated with location and condition information directly from the barcode scan.
Methods of Integrating Barcode Data
Different approaches exist for integrating barcode data with other business systems. The choice depends on factors like the existing software’s capabilities, budget, and technical expertise. Common methods include application programming interfaces (APIs), file-based integration, and dedicated integration software.APIs offer a robust and flexible method for real-time data exchange. The barcode system’s software communicates directly with the accounting or asset management system through a defined set of instructions.
This ensures immediate updates and reduces latency. File-based integration, on the other hand, involves exporting barcode data to a file (e.g., CSV or XML) which is then imported into the other system. This is simpler to implement but less efficient for real-time updates. Dedicated integration software acts as a bridge between the two systems, often offering more features and customization options than API or file-based integration.
This can be a cost-effective solution for businesses lacking in-house technical expertise.
Challenges in Integrating Barcode Systems
Integrating a barcode system isn’t always straightforward. Potential challenges include data format incompatibility, security concerns, and the need for system downtime during integration. Data format incompatibility arises when the barcode system and the existing software use different data structures. This requires data transformation or mapping to ensure compatibility. Security is a critical concern; robust security measures must be implemented to prevent unauthorized access to sensitive data.
Finally, system downtime during integration can disrupt operations. Careful planning and implementation, potentially using phased rollouts, can mitigate this risk.
Solutions to Integration Challenges
Addressing these challenges requires proactive planning and the right approach. Data mapping and transformation tools can handle data format incompatibility. These tools automate the process of converting data from one format to another. Secure APIs and encryption protocols can protect sensitive data during transmission and storage. Phased integration, where the system is implemented in stages, minimizes downtime and allows for thorough testing.
Outsourcing the integration process to a specialized firm can provide expertise and reduce the burden on internal IT staff. Thorough testing and validation are essential before full deployment to ensure seamless functionality and data integrity.
Advanced Barcode System Features

Upgrading your office equipment inventory system beyond basic barcode scanning unlocks significant efficiency gains and enhanced data insights. This section explores advanced features that can transform your inventory management process, leading to better resource allocation and reduced operational costs. We’ll examine the capabilities of RFID technology, the benefits of real-time location tracking, and the advantages of leveraging mobile applications.
RFID Tag Functionality Compared to Barcodes
RFID (Radio-Frequency Identification) tags offer a significant advantage over traditional barcodes in tracking office equipment. Unlike barcodes, which require line-of-sight scanning, RFID tags can be read from a distance, even if they are obscured or stacked. This means faster inventory counts and the ability to track multiple items simultaneously. Furthermore, RFID tags can store significantly more data than barcodes, allowing for the inclusion of serial numbers, asset tags, maintenance history, and other crucial information.
This richer data set facilitates more comprehensive tracking and analysis of your office equipment. For example, an RFID tag could track not only the location of a laptop, but also its last service date and the assigned user.
Real-Time Location Tracking and Inventory Management
Real-time location tracking (RTLS) systems, often integrated with RFID technology, provide continuous monitoring of office equipment within a defined area. This eliminates the need for periodic manual inventory checks, offering an always-up-to-date view of asset location. This improved visibility helps prevent loss or theft, simplifies equipment relocation, and streamlines maintenance scheduling. Imagine a scenario where a crucial piece of equipment is needed immediately – with RTLS, its precise location is instantly available, minimizing downtime.
In a large office environment, this can translate into significant cost savings by reducing search time and improving operational efficiency.
Mobile Applications for Enhanced Barcode Inventory Management
Mobile applications designed for barcode inventory management offer a significant boost in productivity and accessibility. These apps often incorporate features such as barcode scanning, data entry, real-time reporting, and integration with existing inventory management software. For instance, an inventory manager can use a mobile app to conduct a quick inventory check on the go, updating the system in real-time.
Some applications allow for image capture, facilitating the documentation of equipment condition. Examples include inventory management software like Sortly, inFlow Inventory, or Cin7, which offer mobile app compatibility for convenient and efficient inventory tracking. The ability to access and update inventory data from any location empowers staff to manage resources effectively, regardless of their physical proximity to the central office.
Cost Analysis and Return on Investment

Implementing a barcode inventory system for office equipment requires a careful consideration of costs and the potential return on that investment. Understanding the various expenses involved, from initial setup to ongoing maintenance, is crucial for making an informed decision. Equally important is assessing the potential benefits, such as reduced equipment loss and streamlined purchasing processes, to determine the overall value proposition.
A comprehensive cost analysis should encompass all aspects of system implementation and operation. This includes the initial investment in hardware (barcode scanners, printers, etc.), software licensing fees, and professional services for installation and training. Ongoing maintenance costs, such as software updates and technical support, should also be factored in. The long-term financial implications should be carefully weighed against the potential for cost savings and increased efficiency.
Barcode System Cost Comparison
The cost of implementing a barcode system varies significantly depending on the scale of the operation, the chosen software, and the level of integration required. The following table provides a comparative overview of different system options, illustrating the range of potential expenses.
System Type | Initial Investment | Ongoing Maintenance (Annual) | Software Licensing (Annual) |
---|---|---|---|
Basic, Standalone System | $500 – $1500 | $100 – $300 | $50 – $200 |
Mid-range System with Cloud Integration | $1500 – $5000 | $300 – $800 | $200 – $800 |
Enterprise-level System with Full Integration | $5000+ | $800+ | $800+ |
Note: These figures are estimates and can vary based on specific vendor offerings and system requirements. It is recommended to obtain quotes from multiple vendors to accurately assess costs.
Return on Investment (ROI) from Barcode Inventory Systems, Business inventory barcode system office equipment
The ROI of a barcode inventory system stems from several key areas. Improved accuracy in inventory tracking minimizes the risk of equipment loss or theft, resulting in direct cost savings. Furthermore, a streamlined system optimizes purchasing decisions by providing real-time data on equipment availability, reducing the likelihood of overstocking or stockouts. This leads to lower storage costs and improved operational efficiency.
For example, a company with a history of losing 10% of its office equipment annually, costing $10,000, could see a direct saving of $1000 annually simply by reducing losses by 10% through better tracking. Moreover, reduced stockouts and overstocking could lead to further cost savings in storage and purchasing, boosting the overall ROI. A well-implemented system can quickly pay for itself through these combined benefits.
Impact of Improved Inventory Management
Effective inventory management significantly reduces equipment loss and optimizes purchasing decisions. Real-time tracking allows for immediate identification of missing or damaged items, enabling quicker recovery or replacement. This minimizes downtime and maintains operational efficiency. Data-driven insights into equipment usage patterns help optimize purchasing decisions, ensuring that the right equipment is procured at the right time, preventing unnecessary expenses associated with overstocking or outdated technology.
The ability to track equipment location also aids in efficient asset deployment and simplifies maintenance scheduling.
Conclusive Thoughts
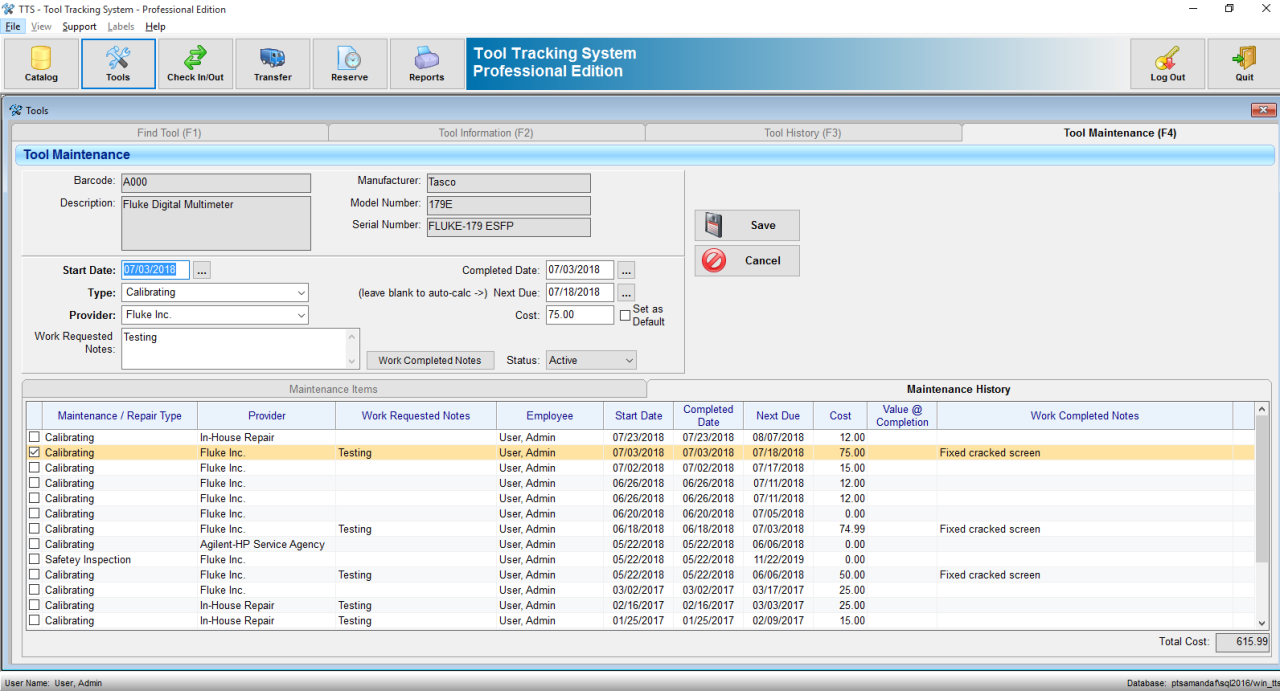
Successfully implementing a business inventory barcode system for office equipment can dramatically improve efficiency and reduce costs. By carefully considering the various aspects discussed—from choosing the appropriate barcode symbology and hardware to integrating the system with existing software and leveraging advanced features—businesses can optimize their asset management processes. The potential return on investment, in terms of reduced losses, improved purchasing decisions, and streamlined operations, makes this a worthwhile investment for organizations of all sizes.
A well-structured system ensures accurate tracking, simplifies reporting, and ultimately contributes to a more organized and productive work environment.
Detailed FAQs: Business Inventory Barcode System Office Equipment
What are the different types of barcode scanners available?
Several types exist, including laser scanners, CCD scanners, and imagers, each with varying capabilities and price points. The best choice depends on your specific needs and budget.
How do I handle damaged or unreadable barcodes?
Establish a clear protocol for handling damaged barcodes, which might involve re-labeling the item with a new barcode and updating the inventory database accordingly.
What security measures should be implemented to protect barcode data?
Implement access controls to limit who can access and modify barcode data. Consider using encryption to protect sensitive information.
What if my office equipment inventory changes frequently?
Choose a system that allows for easy updates and modifications to your inventory database. Cloud-based solutions often offer the most flexibility.