Business inventories y ae – Business inventories YAE (year-over-year change) provides crucial insights into economic health. Understanding how businesses manage their stock of raw materials, work-in-progress, and finished goods reveals much about consumer demand, production efficiency, and overall economic trends. This analysis delves into the intricacies of inventory management, exploring its impact on economic growth, profitability, and the various factors that influence inventory levels.
We’ll examine different inventory management techniques and the significance of year-over-year comparisons in interpreting economic data.
Analyzing year-over-year changes in business inventories offers a unique perspective on economic cycles. Periods of high inventory accumulation often suggest weakening demand, while inventory depletion can indicate strong consumer spending. This analysis explores the relationship between inventory levels and economic growth, highlighting the importance of understanding these dynamics for businesses and policymakers alike. We’ll consider macroeconomic factors such as consumer confidence, interest rates, and supply chain disruptions and how they influence inventory decisions.
Business Inventories
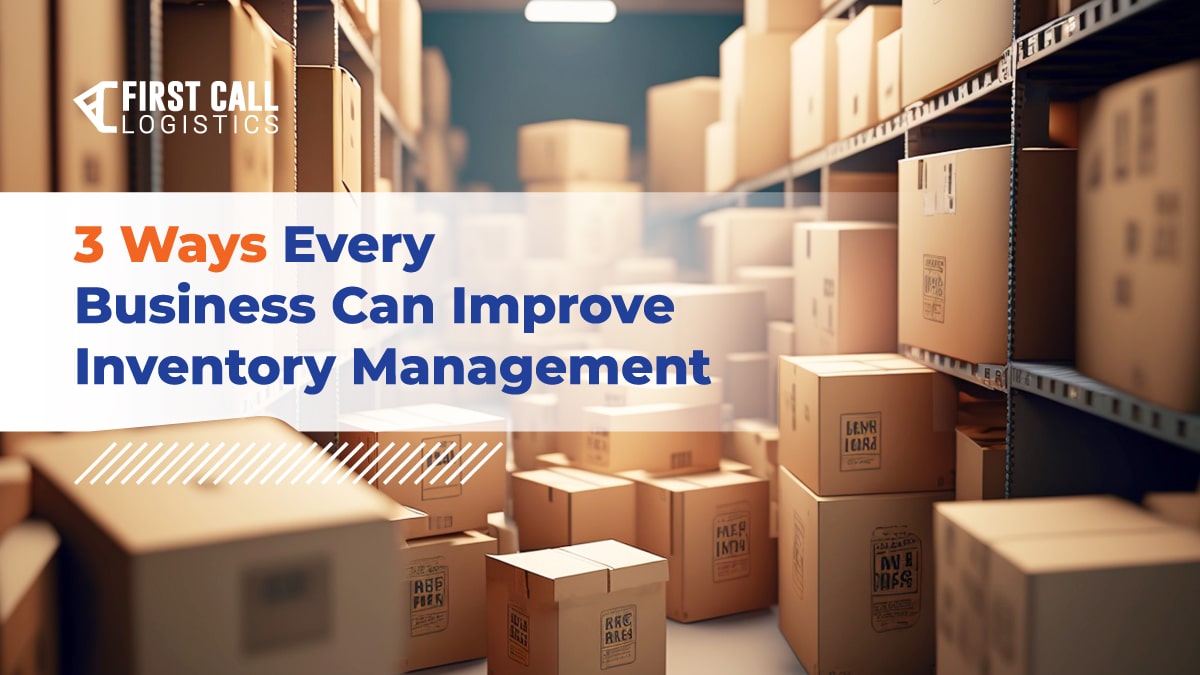
Business inventories represent the goods held by businesses at a specific point in time, intended for sale or use in production. Understanding these inventories is crucial for macroeconomic analysis, as they serve as a key indicator of economic health and future production levels. Changes in inventory levels can signal shifts in consumer demand, production capacity, and overall economic activity.
Components of Business Inventories
Business inventories are typically categorized into three main components: raw materials, work-in-progress (WIP), and finished goods. Raw materials are the unprocessed inputs used in production. Work-in-progress encompasses partially finished goods that are still undergoing various stages of manufacturing. Finished goods are completed products ready for sale to consumers or other businesses. The proportion of each component within a company’s total inventory will vary significantly depending on the industry and the company’s production cycle.
Inventory Categorization Across Industries
Different industries will categorize their inventories in ways that reflect their unique production processes and supply chains. For example, a manufacturing company will have a significant portion of its inventory in work-in-progress, while a retailer will primarily hold finished goods. A technology company might have a large inventory of components and semi-finished products, while a service-based company might have minimal physical inventory, focusing instead on intangible assets and intellectual property.
The specific classification and management of inventories are vital for efficient operations and profitability.
Inventory Type, Description, and Economic Impact
Inventory Type | Description | Example | Impact on Economic Activity |
---|---|---|---|
Raw Materials | Unprocessed inputs used in production. | Steel for a car manufacturer, cotton for a textile company. | Increased raw material inventories can signal anticipated increased production, potentially boosting economic activity. Conversely, decreased inventories might indicate supply chain disruptions or decreased future production. |
Work-in-Progress (WIP) | Partially finished goods undergoing manufacturing. | Car bodies in a car assembly plant, partially sewn garments in a clothing factory. | High WIP inventories might indicate production bottlenecks or slowdowns. Low WIP inventories can signify efficient production processes. |
Finished Goods | Completed products ready for sale. | Cars in a dealership, clothes on retail shelves. | High finished goods inventories can indicate weak consumer demand or overproduction, potentially leading to price reductions and impacting economic growth. Low inventories might signal strong demand, leading to increased production and economic expansion. |
Inventory Levels and Economic Growth: Business Inventories Y Ae
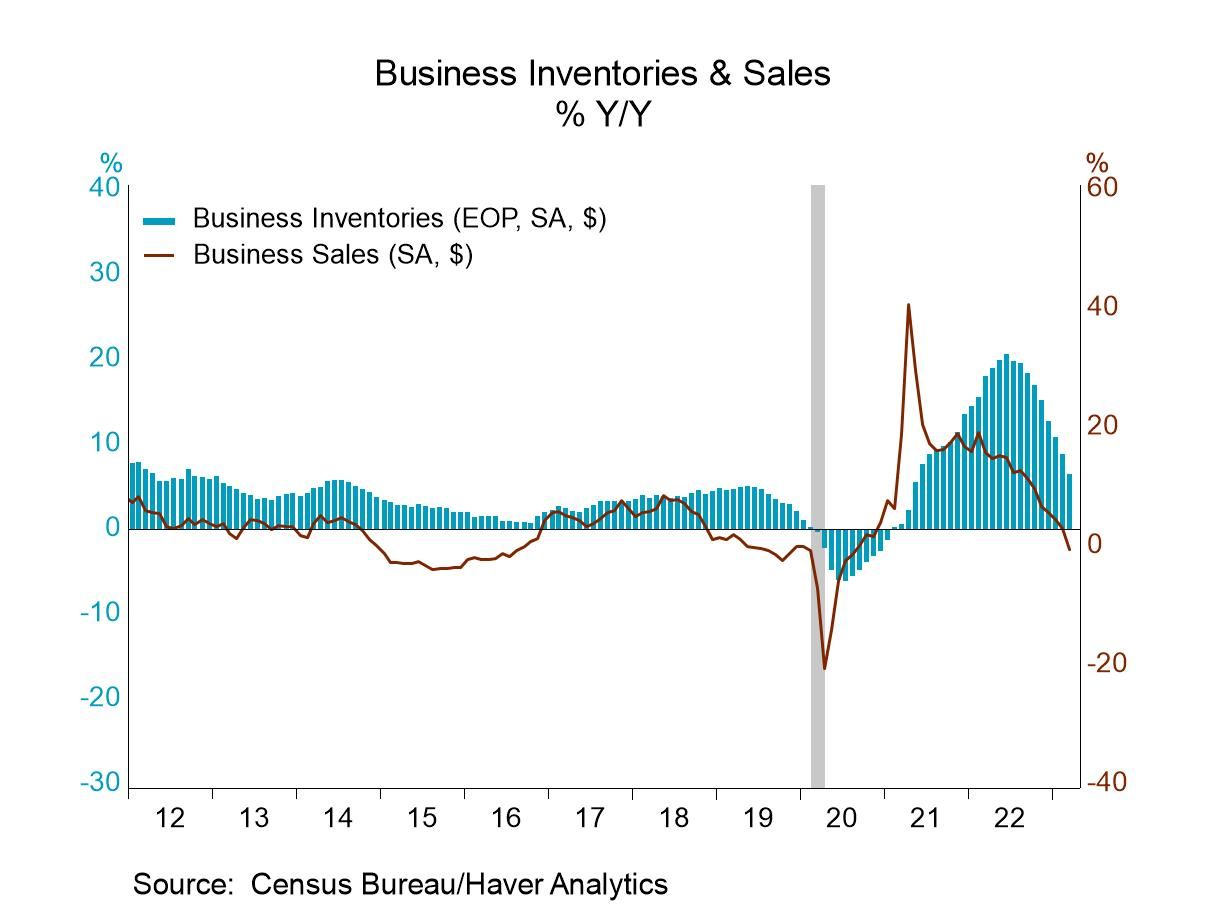
Inventory levels play a crucial role in economic growth, acting as a buffer between production and consumption. Fluctuations in inventory investment directly impact a nation’s Gross Domestic Product (GDP), offering valuable insights into the health and trajectory of the economy. Understanding this relationship is key to effective economic forecasting and policymaking.Changes in inventory investment significantly contribute to GDP calculations.
Inventory investment represents the change in the value of inventories held by businesses from one period to the next. When businesses increase their inventories (accumulation), this adds to GDP, reflecting increased production. Conversely, when businesses reduce their inventories (depletion), this subtracts from GDP, signaling potentially weakening demand. This is because GDP measures the total value of goods and servicesproduced* within a specific period, and changes in inventory levels directly reflect this production.
A rise in inventory suggests increased production exceeding current sales, while a fall indicates sales exceeding production.
Inventory Accumulation and Depletion
Periods of high inventory accumulation often precede economic slowdowns. Businesses build up inventories anticipating increased future demand, but if that demand fails to materialize, they are left with excess stock, potentially leading to price reductions, decreased profitability, and ultimately, layoffs. Conversely, inventory depletion can indicate strong consumer demand, stimulating further production and economic expansion. However, sustained depletion can also signal potential shortages and supply chain issues, which can hinder economic growth in the long run.
For example, during the initial phases of the COVID-19 pandemic, many businesses experienced significant inventory depletion due to unprecedented demand for certain goods, highlighting the complexities of this relationship. Conversely, the subsequent periods saw significant inventory accumulation as supply chains struggled to keep pace.
Hypothetical Scenario: Unexpectedly High Inventory Levels
Imagine a clothing retailer, “Trendy Threads,” anticipating a surge in demand for a new line of winter coats. They significantly increase their inventory orders. However, due to unexpectedly mild weather, demand remains low. Trendy Threads is now burdened with high inventory levels. To clear the excess stock, they are forced to offer substantial discounts, drastically reducing profit margins.
The high carrying costs associated with storing the unsold coats – including warehouse fees, insurance, and potential obsolescence – further erode profitability. This scenario illustrates how unexpectedly high inventory levels, even if initially intended to support growth, can negatively impact a company’s financial performance, leading to reduced profits and potentially losses. This situation highlights the risk associated with inaccurate demand forecasting and the importance of efficient inventory management.
Factors Influencing Inventory Levels
Business inventory management is a complex balancing act, significantly impacted by a confluence of internal and external factors. Understanding these influences is crucial for businesses to optimize their inventory levels, minimizing costs while ensuring sufficient stock to meet demand. Effective inventory management directly contributes to profitability and overall business success.
Macroeconomic Factors Influencing Inventory Decisions
Consumer demand, interest rates, and production capacity are key macroeconomic factors that significantly shape business inventory decisions. Strong consumer demand typically leads businesses to increase inventory levels to meet anticipated sales. Conversely, weak demand might prompt them to reduce inventory to avoid holding costs. High interest rates increase the cost of borrowing, discouraging businesses from holding large inventories, as the financing becomes more expensive.
Production capacity constraints can also limit the amount of inventory a business can hold, forcing them to manage their stock more carefully. For example, a surge in demand for electronics during a holiday season might cause manufacturers to increase their production and inventory levels to meet consumer expectations. However, if interest rates rise sharply, those same manufacturers might hesitate to borrow heavily to finance increased inventory.
Supply Chain Disruptions and Inventory Management
Supply chain disruptions, such as natural disasters, geopolitical instability, or pandemics, can severely impact inventory management. These events can lead to delays in receiving raw materials or finished goods, causing stockouts and potentially harming a company’s reputation. The COVID-19 pandemic, for instance, highlighted the vulnerability of global supply chains, resulting in widespread shortages of various goods. Effective risk management strategies, including diversification of suppliers and maintaining safety stock, are crucial to mitigate the effects of supply chain disruptions.
Imagine a clothing retailer heavily reliant on a single supplier in a region hit by a major earthquake; the disruption could lead to significant inventory shortages and lost sales.
Comparing Inventory Management Strategies
Businesses employ different inventory management strategies based on their business model and risk tolerance. Just-in-time (JIT) inventory management aims to minimize inventory holding costs by receiving materials only when needed for production. This strategy is efficient but highly vulnerable to supply chain disruptions. In contrast, just-in-case (JIC) inventory management involves holding larger quantities of inventory to buffer against unexpected demand fluctuations or supply chain issues.
While JIC offers greater security, it increases storage and holding costs. A car manufacturer might use a JIT approach for some components, while a grocery store might prefer a JIC approach for perishable goods to avoid spoilage.
Unexpected Changes in Consumer Behavior and Inventory Imbalances
Unexpected shifts in consumer behavior can lead to significant inventory imbalances. Changes in consumer preferences, driven by trends, technological advancements, or economic factors, can render existing inventory obsolete or insufficient. For example, a sudden shift towards plant-based diets could leave meat producers with excess inventory, while creating shortages for plant-based alternatives. Similarly, a rapid increase in demand for home fitness equipment during a pandemic could lead to stockouts, while the subsequent decline in demand might result in excess inventory for fitness equipment retailers.
Effective market research and demand forecasting are essential to mitigate the risks associated with unpredictable consumer behavior.
Inventory Management Techniques

Effective inventory management is crucial for a business’s success. Maintaining optimal inventory levels balances the need to meet customer demand with the costs associated with holding excess stock. Several techniques help businesses achieve this balance, each with its own strengths and weaknesses. Understanding these techniques is key to streamlining operations and maximizing profitability.
ABC Analysis
ABC analysis categorizes inventory items based on their value and consumption. ‘A’ items represent a small percentage of total items but account for a large percentage of the total value. ‘B’ items are intermediate in both value and volume, while ‘C’ items are numerous but have a low overall value. This analysis allows businesses to prioritize inventory control efforts, focusing resources on managing high-value ‘A’ items more closely.
The advantages include improved resource allocation and reduced risk of stockouts for critical items. However, it requires accurate and up-to-date data on item value and consumption, and the categorization may need periodic review as market conditions change.
Economic Order Quantity (EOQ) Model
The EOQ model determines the optimal order quantity that minimizes the total inventory costs, balancing ordering costs and holding costs. The formula considers factors such as demand rate, ordering cost, and holding cost.
EOQ = √[(2DS)/H] where D = annual demand, S = ordering cost per order, and H = holding cost per unit per year.
Advantages include cost reduction through optimized ordering and reduced storage space needs. Disadvantages include assumptions of constant demand and lead times, which may not always hold true in reality. Furthermore, the model doesn’t account for potential stockouts or discounts for bulk ordering.
Safety Stock
Safety stock is the extra inventory held to buffer against unexpected demand fluctuations or supply chain disruptions. The amount of safety stock depends on factors such as demand variability, lead time, and service level targets. The primary advantage is protection against stockouts and maintaining customer service levels. However, holding safety stock increases carrying costs and ties up capital that could be used elsewhere.
Determining the optimal safety stock level requires careful consideration of various factors and often involves statistical forecasting techniques.
Comparison of Inventory Control Systems
The effectiveness of inventory management hinges on the chosen control system. Choosing the right system depends on factors like business size, product type, and industry. Below is a comparison of three common systems:
The following table compares three common inventory control systems:
Inventory Control System | Advantages | Disadvantages |
---|---|---|
Just-in-Time (JIT) | Minimizes inventory holding costs, improves efficiency, reduces waste. | Highly dependent on reliable suppliers, vulnerable to supply chain disruptions, requires precise demand forecasting. |
Periodic Review System | Simple to implement, requires less frequent inventory counts. | Higher risk of stockouts, may lead to higher ordering costs due to larger order quantities. |
Continuous Review System | Lower risk of stockouts, allows for efficient management of individual items. | Requires more sophisticated tracking systems, can be more complex to implement. |
Forecasting Models and Inventory Optimization, Business inventories y ae
A clothing retailer, for example, might use time series analysis to forecast demand for specific items based on past sales data, seasonality, and trends. This forecast then informs the retailer’s ordering decisions, allowing them to adjust inventory levels to meet anticipated demand. If the model predicts a surge in demand for a particular style of coat during the upcoming winter season, the retailer can proactively increase its inventory levels to avoid stockouts and lost sales.
Conversely, if demand for a certain type of shirt is predicted to decline, the retailer can reduce its orders to avoid excess inventory and minimize storage costs. This proactive approach, driven by accurate forecasting, helps optimize inventory levels and improve profitability.
The Role of “YAE” (Year-to-Year Change) in Inventory Analysis
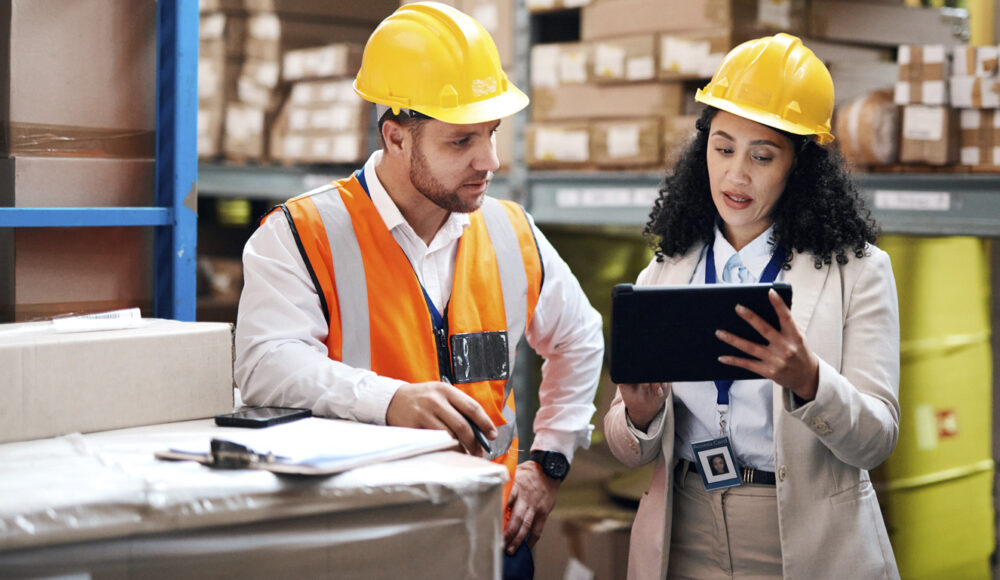
Year-over-year (YAE) changes in business inventories provide a crucial long-term perspective on inventory trends, offering valuable insights often obscured by shorter-term fluctuations seen in monthly or quarterly data. Analyzing YAE data allows businesses and economists to identify underlying patterns and assess the health of the economy more effectively.Analyzing YAE data helps to understand inventory trends and economic cycles by smoothing out the noise of seasonal variations and short-term market shocks.
This longer-term view reveals underlying growth or decline trends more clearly, allowing for more accurate forecasting and strategic decision-making. For example, a consistent upward trend in YAE inventory levels might indicate strong consumer demand and healthy economic growth, while a persistent downward trend could signal weakening demand and potential economic slowdown.
Comparison of YAE, Monthly, and Quarterly Data Analysis
Analyzing YAE data offers a distinct advantage over relying solely on monthly or quarterly data. While monthly and quarterly figures provide granular detail, they can be highly volatile, influenced by factors like seasonal sales patterns or temporary supply chain disruptions. YAE data, however, provides a more stable picture by averaging out these shorter-term fluctuations. This makes it particularly useful for identifying significant long-term shifts in inventory levels and their correlation with broader economic cycles.
For instance, a sharp increase in monthly inventory might be a temporary surge, while a consistent increase in YAE inventory over several years would point to a more substantial trend.
Interpreting Significant Increases or Decreases in YAE Business Inventory Data
A significant increase in YAE business inventory data can indicate several possibilities. A strong increase coupled with robust sales growth suggests healthy demand and efficient inventory management. However, a large increase accompanied by stagnant or declining sales could signal overstocking, potentially leading to reduced profitability due to storage costs and potential markdowns. Conversely, a significant decrease in YAE inventory could reflect strong consumer demand outpacing supply, potentially leading to stockouts and lost sales opportunities.
It could also indicate deliberate inventory reduction strategies by businesses aiming to improve efficiency or respond to weakening demand. The interpretation requires careful consideration of concurrent economic indicators, such as sales figures, production levels, and consumer confidence indices. For example, a significant decrease in YAE inventory during a period of high inflation might indicate businesses are actively trying to reduce costs by minimizing stock.
Data Sources and Analysis of Business Inventories
Understanding business inventories requires access to reliable data and the ability to interpret it effectively. This section details key data sources, data collection methods, interpretation guidelines, and potential biases inherent in available inventory data. Accurate inventory analysis is crucial for understanding economic trends and making informed business decisions.Reliable sources of data on business inventories are primarily government statistical agencies.
These agencies employ rigorous methodologies to collect and process data, providing a relatively consistent and comprehensive view of inventory levels across various sectors of the economy.
Reliable Sources of Business Inventory Data
Government statistical agencies, such as the U.S. Census Bureau (in the United States), the Bureau of Economic Analysis (BEA), and their counterparts in other countries, are the primary sources of comprehensive business inventory data. These agencies regularly collect and publish data on various aspects of inventories, including manufacturing, wholesale, and retail sectors. International organizations like the Organisation for Economic Co-operation and Development (OECD) also compile and aggregate inventory data from member countries, providing a global perspective.
Private sector data providers often supplement government data, offering more granular industry-specific information, but their data may not always be as comprehensive or publicly accessible.
Methods for Collecting and Processing Business Inventory Data
Data collection typically involves surveys sent to businesses across various industries. These surveys request information on the value of inventories held at specific points in time, often monthly or quarterly. The surveys employ sampling techniques to reduce the burden on businesses while ensuring representativeness of the overall economy. Data processing involves rigorous quality checks, error correction, and adjustments for seasonal variations and price changes to ensure the data’s accuracy and comparability over time.
Sophisticated statistical methods are used to estimate inventory levels for businesses that do not respond to the surveys.
Interpreting Inventory Data from a Government Report
A step-by-step guide to interpreting inventory data from a government report might look like this:
1. Identify the reporting agency and data frequency
Understand the source of the data (e.g., BEA, Census Bureau) and the reporting period (monthly, quarterly, annually). This context is crucial for interpreting the data’s relevance and limitations.
2. Examine the data categories
Government reports typically break down inventory data by industry (manufacturing, wholesale, retail), type of inventory (raw materials, work-in-progress, finished goods), and sometimes by specific product categories. Understanding these categories is crucial for focusing the analysis on relevant sectors.
3. Analyze inventory levels and changes
Pay attention to both the absolute levels of inventory and the changes over time (year-over-year, month-over-month). Large increases or decreases can signal shifts in economic activity or business strategies.
4. Consider inventory-to-sales ratios
This ratio indicates the number of months of sales covered by current inventory levels. A high ratio may suggest overstocking, while a low ratio may indicate potential supply shortages.
5. Relate inventory data to other economic indicators
Inventory data should be analyzed in conjunction with other economic indicators, such as sales, production, and consumer spending, to gain a more comprehensive understanding of economic trends.
Potential Biases and Limitations in Business Inventory Data
While government data is generally reliable, certain biases and limitations exist. Sampling errors can occur, particularly in surveys of smaller businesses. Businesses may underreport inventory levels for tax purposes or due to difficulties in accurately tracking inventory. Data revisions are common as more information becomes available, requiring analysts to account for potential changes in reported figures over time.
Furthermore, the data may not capture the full complexity of inventory management practices within individual firms, focusing primarily on aggregate measures rather than firm-specific details. Finally, changes in accounting methods can affect the comparability of inventory data across time periods.
Closing Summary
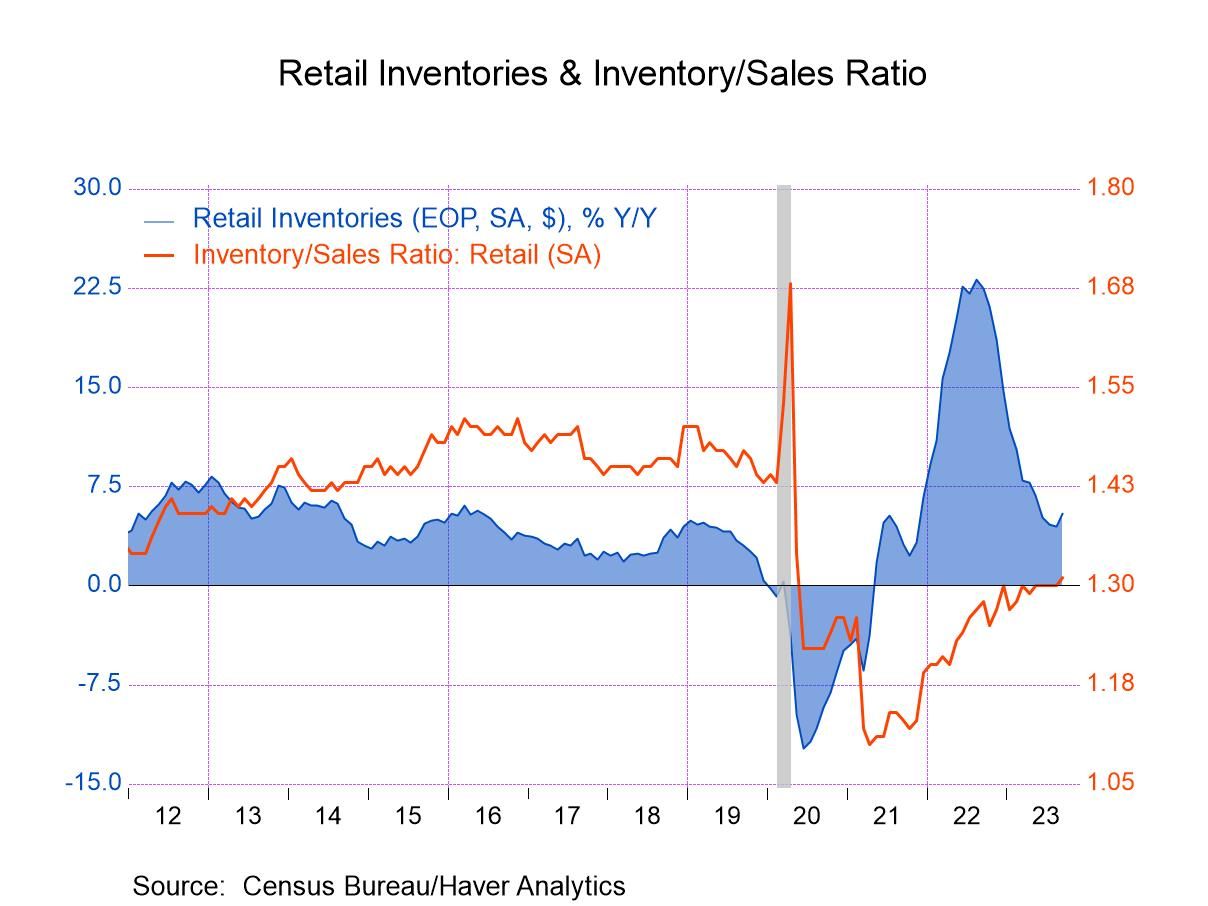
In conclusion, effective business inventory management is crucial for both individual companies and the overall economy. Analyzing year-over-year changes in inventory levels provides a valuable tool for understanding economic trends and predicting future performance. By carefully considering macroeconomic factors, employing appropriate inventory management techniques, and leveraging reliable data sources, businesses can optimize their inventory levels, enhance profitability, and contribute to a healthier economy.
Understanding the nuances of business inventories and their year-over-year fluctuations is paramount for navigating the complexities of the modern economic landscape.
Question & Answer Hub
What are the potential risks of holding excessive inventory?
Holding excessive inventory increases storage costs, risks obsolescence, and ties up capital that could be used elsewhere. It also makes a business vulnerable to losses if demand unexpectedly falls.
How does seasonality affect inventory management?
Businesses in industries with seasonal demand (e.g., retail, tourism) must adjust their inventory levels to meet fluctuating consumer needs. This often involves forecasting and strategic planning to avoid overstocking or stockouts.
What is the role of technology in modern inventory management?
Technology plays a significant role, with software solutions providing real-time inventory tracking, demand forecasting, and automated ordering systems, improving efficiency and reducing errors.
How can a small business improve its inventory management?
Small businesses can benefit from using simple inventory management software, implementing regular stock checks, and focusing on accurate forecasting based on sales history and market trends.