Business inventory accounting programs are crucial for efficient business operation. They streamline inventory management, offering real-time tracking, automated valuation, and insightful reporting features. Understanding the various inventory accounting methods, such as FIFO, LIFO, and weighted average, is vital for accurate financial reporting and informed decision-making. This exploration delves into the core functionalities, implementation, benefits, and future trends of these powerful tools.
From small startups to large enterprises, the right inventory accounting program can significantly impact profitability and operational efficiency. By automating tedious tasks, providing accurate data, and offering predictive analytics, these programs empower businesses to optimize stock levels, minimize waste, and ultimately, boost their bottom line. This guide provides a comprehensive overview, helping businesses choose and implement the solution best suited to their specific needs.
Defining Business Inventory Accounting Programs
Business inventory accounting programs are software solutions designed to streamline the management and tracking of a company’s inventory. These programs automate many of the manual processes involved in inventory control, leading to increased efficiency, reduced errors, and improved profitability. They are essential tools for businesses of all sizes, from small startups to large corporations, that need to accurately manage their stock levels.Inventory accounting programs provide a centralized system for recording inventory transactions, including purchases, sales, returns, and adjustments.
This allows for real-time tracking of inventory levels, providing valuable insights into stock movement and helping businesses make informed decisions regarding purchasing, production, and sales. Core functionalities typically include data entry of inventory items, generating reports on stock levels, managing purchase orders, and tracking costs associated with inventory. Furthermore, they offer features for managing multiple locations and integrating with other business systems, such as accounting and point-of-sale (POS) systems.
Inventory Accounting Methods
Different inventory accounting methods impact how the cost of goods sold (COGS) and ending inventory are calculated. Choosing the right method depends on various factors, including the type of inventory and industry regulations. The three most common methods are:
- First-In, First-Out (FIFO): This method assumes that the oldest inventory items are sold first. This generally results in a higher net income during periods of inflation, as the cost of goods sold is based on older, lower costs. For example, if a company purchased 100 units at $10 and later 100 units at $12, under FIFO, the cost of goods sold for the first 100 units sold would be $1000.
- Last-In, First-Out (LIFO): This method assumes that the newest inventory items are sold first. This generally results in a lower net income during periods of inflation, as the cost of goods sold is based on newer, higher costs. Using the same example, under LIFO, the cost of goods sold for the first 100 units sold would be $1200.
- Weighted Average Cost: This method calculates the average cost of all inventory items available for sale during a period. This average cost is then used to determine the cost of goods sold and ending inventory. In our example, the weighted average cost would be ($10 + $12)/2 = $11, resulting in a cost of goods sold of $1100 for the first 100 units.
Businesses Benefiting from Inventory Accounting Programs
A wide range of businesses can significantly benefit from implementing inventory accounting programs. These include:
- Retail Businesses: Effectively managing stock levels is crucial for retailers to avoid stockouts or overstocking. Inventory programs help optimize inventory levels, reducing storage costs and maximizing sales opportunities.
- Manufacturing Companies: Precise inventory tracking is essential for manufacturers to ensure they have the necessary raw materials and components for production. Inventory programs help manage production schedules and minimize disruptions caused by material shortages.
- Wholesale Distributors: Distributors need to efficiently manage large volumes of inventory from multiple suppliers. Inventory programs streamline order processing, tracking, and delivery, ensuring timely fulfillment of customer orders.
- Restaurants and Food Service Businesses: Accurate inventory control is critical for managing perishable goods and minimizing waste. Inventory programs help track stock levels, predict demand, and optimize ordering to reduce spoilage.
Comparison of Inventory Accounting Programs
The following table compares three popular inventory accounting programs:
Feature | Program A | Program B | Program C |
---|---|---|---|
Cost | $29/month | $49/month | $99/month |
Inventory Tracking Methods | FIFO, Weighted Average | FIFO, LIFO, Weighted Average | FIFO, LIFO, Weighted Average, Specific Identification |
Reporting Capabilities | Basic reports | Advanced reports, customizable dashboards | Highly customizable reports, real-time data visualization |
Integration Capabilities | Limited integrations | Integrates with popular accounting software | Seamless integration with multiple platforms |
Key Features and Benefits: Business Inventory Accounting Program
A robust business inventory accounting program offers a range of features designed to streamline operations and improve profitability. These features go beyond simple stock tracking; they provide real-time insights, automate complex processes, and integrate seamlessly with other crucial business systems. The resulting benefits translate directly into increased efficiency, reduced costs, and improved decision-making.Real-time inventory tracking is essential for maintaining accurate stock levels and preventing stockouts or overstocking.
Automated inventory valuation and reporting provide timely financial information, while integrated inventory management ensures data consistency across different business functions. Finally, advanced forecasting features offer predictive capabilities, allowing businesses to proactively manage their inventory and optimize their supply chain.
Real-Time Inventory Tracking
Real-time inventory tracking provides immediate visibility into stock levels, location, and movement. This eliminates the delays and inaccuracies associated with periodic stocktaking, allowing businesses to respond quickly to changes in demand and prevent costly stockouts. For example, a retail store using a real-time system can instantly see when a popular item is running low, allowing them to reorder immediately and avoid lost sales.
This dynamic view minimizes the risk of lost sales due to unavailable inventory and prevents the tying up of capital in excess stock. The system provides accurate data for improved purchasing decisions.
Automated Inventory Valuation and Reporting
Automated inventory valuation and reporting significantly reduces the time and effort required for financial reporting. The system automatically calculates the value of inventory using various methods (FIFO, LIFO, weighted average), generating accurate reports for financial statements and tax purposes. This automation minimizes human error and ensures compliance with accounting standards. For instance, a manufacturing company using an automated system can generate accurate cost of goods sold (COGS) reports in real-time, enabling timely financial analysis and informed decision-making regarding pricing and production.
These reports are critical for accurate financial reporting and tax compliance.
Integrated Inventory Management
Integrating inventory management with other business software, such as accounting and CRM systems, eliminates data silos and ensures data consistency. This integration streamlines workflows and improves overall efficiency. For example, when an order is placed in the CRM system, the integrated inventory system automatically updates stock levels, preventing overselling and ensuring accurate order fulfillment. Similarly, the accounting system automatically receives accurate COGS data, eliminating manual data entry and reducing the risk of errors.
This seamless flow of information between systems minimizes data discrepancies and promotes a unified view of business operations.
Inventory Forecasting Features
Inventory forecasting features utilize historical data and predictive algorithms to forecast future demand. This allows businesses to proactively manage inventory levels, optimizing stock levels and minimizing storage costs. For example, a clothing retailer using a forecasting system might predict higher demand for winter coats in November and December, allowing them to adjust their purchasing and stocking strategies accordingly. This proactive approach avoids stockouts during peak seasons and minimizes the risk of holding excessive inventory during periods of low demand.
The system helps avoid unnecessary storage costs and potential losses from obsolete stock.
Implementation and Integration
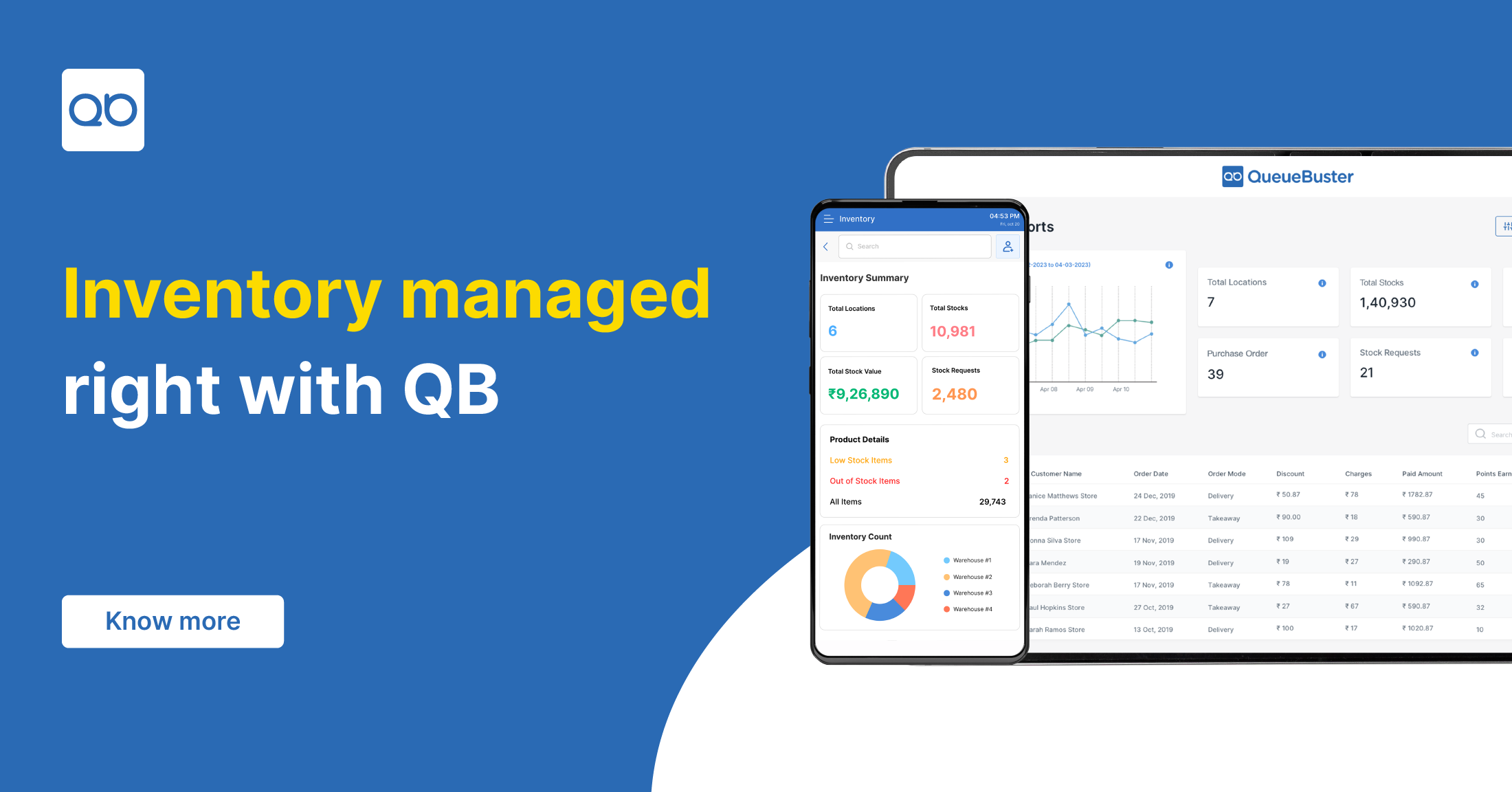
Successfully implementing a business inventory accounting program requires careful planning and execution. This involves not only setting up the software itself but also integrating it seamlessly with your existing systems and migrating your data effectively. A smooth transition minimizes disruption to your business operations and ensures the program delivers its intended benefits.The process of setting up and configuring a business inventory accounting program typically involves several key steps.
These steps ensure the software accurately reflects your business needs and data. Proper configuration is crucial for optimal performance and reliable reporting.
Software Setup and Configuration
This stage involves installing the chosen software, configuring user access and permissions, and customizing settings to match your business’s specific requirements. This might include defining chart of accounts, setting up inventory tracking methods (FIFO, LIFO, weighted average), and establishing reporting preferences. For example, you would define your inventory items, including their unique identifiers, descriptions, cost, and location. You would also configure the system to automatically calculate inventory value based on your chosen method.
The setup process will vary slightly depending on the specific software, but most programs provide detailed guides and support documentation.
Integrating with Existing Accounting Systems
Integrating your new inventory accounting program with your existing accounting software (like QuickBooks or Xero) is essential for a streamlined workflow. This integration typically involves using APIs (Application Programming Interfaces) or data import/export features. For example, sales data from your point-of-sale (POS) system can automatically update inventory levels in your inventory management software, eliminating manual data entry and reducing the risk of errors.
A successful integration will provide a real-time view of your inventory and financial performance, providing accurate data for decision-making. The specific integration process will depend on the capabilities of both your inventory and accounting software.
Data Migration from Manual Systems
Migrating data from a manual system to an automated one requires a structured approach. This process involves extracting data from spreadsheets, databases, or physical inventory records. Data cleaning and validation are critical steps to ensure data accuracy. For example, you might need to standardize product codes, correct inconsistencies in pricing, and reconcile discrepancies between physical inventory counts and recorded data.
This data will then be imported into the new inventory accounting program. Consider using a phased approach, migrating data in segments to minimize disruption and allow for error correction along the way.
Checklist of Essential Considerations Before Implementation
Before implementing a new inventory management system, a thorough assessment is crucial. This checklist summarizes key factors to consider:
- Define your requirements: Clearly articulate your business needs and objectives for the new system.
- Software selection: Choose software that aligns with your budget, business size, and technical capabilities.
- Data migration plan: Develop a detailed plan for migrating existing data, including data cleaning and validation.
- Training and support: Ensure adequate training is provided to staff, and establish a support system for ongoing assistance.
- Integration testing: Thoroughly test the integration with existing systems to identify and resolve potential issues.
- Go-live plan: Develop a detailed plan for the transition to the new system, minimizing disruption to operations.
- Post-implementation review: Schedule a review to assess the system’s performance and identify areas for improvement.
Data Management and Reporting
Effective data management and insightful reporting are crucial for optimizing inventory control and maximizing profitability. A robust inventory accounting program should provide tools to ensure data accuracy, generate comprehensive reports, and facilitate informed decision-making. This section details how to leverage these capabilities for better inventory management.
Maintaining Data Accuracy and Integrity
Data accuracy is paramount. Implementing a system of checks and balances, including regular data validation and reconciliation, is essential. This involves comparing data from various sources, such as purchase orders, sales invoices, and physical stock counts, to identify discrepancies. Automated data entry wherever possible minimizes human error. Regular backups of the database safeguard against data loss.
User access controls limit data modification to authorized personnel only, enhancing data integrity. Implementing a system of audit trails tracks all changes made to the inventory data, providing accountability and facilitating error identification.
Generating Insightful Inventory Reports
The program’s reporting features allow for the generation of various inventory reports providing valuable insights into stock levels, sales trends, and profitability. Standard reports should include stock level reports showing current quantities on hand, reorder points, and lead times for each item. Sales trend reports illustrate sales performance over time, identifying seasonal variations and predicting future demand. Profitability reports analyze the gross profit margin for each item, highlighting high- and low-margin products.
These reports are essential for informed decision-making related to purchasing, pricing, and product lifecycle management.
Identifying Slow-Moving or Obsolete Inventory
The program can identify slow-moving or obsolete inventory through the generation of customized reports. These reports often analyze inventory turnover rates, comparing the rate of sales to the amount of inventory held. Items with low turnover rates, below a predefined threshold, are flagged as slow-moving. Obsolete inventory, which is unlikely to be sold due to obsolescence or damage, is identified by comparing inventory against sales data over a specified period.
This allows for proactive management, enabling businesses to clear out slow-moving items through discounts or other strategies, minimizing storage costs and potential losses.
Examples of Custom Reports
The program allows for the creation of custom reports tailored to specific business needs. Below are examples of such reports, along with sample data:
Report Type | Item | Quantity | Value |
---|---|---|---|
Low Stock Report | Widget A | 10 | $100 |
Low Stock Report | Widget B | 5 | $50 |
Sales Trend Report (Last 3 Months) | Widget C | 100, 120, 150 | $1000, $1200, $1500 |
Profitability Report | Widget D | 200 | $2000 (60% margin) |
Report Type | Item | Turnover Rate | Status |
---|---|---|---|
Inventory Turnover Report | Widget E | 0.5 | Slow-Moving |
Inventory Turnover Report | Widget F | 0.2 | Obsolete |
Inventory Turnover Report | Widget G | 2.0 | Fast-Moving |
Inventory Turnover Report | Widget H | 1.5 | Normal |
Cost and Return on Investment
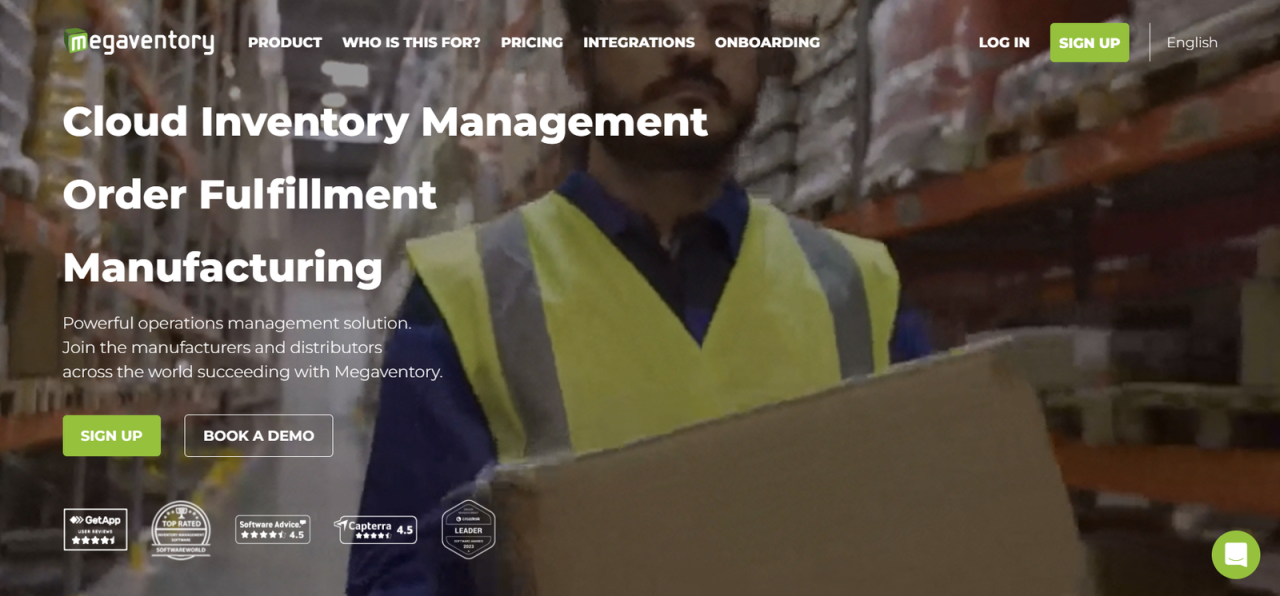
Implementing an inventory accounting program represents a significant investment, but the potential returns can far outweigh the initial expenses. A thorough understanding of both the costs and the potential ROI is crucial for making an informed decision. This section details the various cost factors involved and explores how improved inventory management translates into tangible financial benefits.The costs associated with implementing and maintaining an inventory accounting program are multifaceted.
These costs can be broadly categorized into upfront implementation costs and ongoing maintenance costs.
Software Licensing and Implementation Costs
Software licensing fees vary widely depending on the chosen program’s features, scalability, and vendor. These fees can range from a one-time purchase to recurring subscription models. Implementation costs include the time and resources required to set up the system, integrate it with existing software, and train employees. This might involve consulting fees, internal staff time, and data migration expenses.
For example, a small business might spend between $1,000 and $5,000 on software and implementation, while a larger enterprise could invest tens of thousands of dollars.
Ongoing Maintenance and Support Costs, Business inventory accounting program
Beyond the initial investment, ongoing costs include software maintenance fees (updates, bug fixes, and technical support), employee training on new features or updates, and potential costs associated with system upgrades or expansions. These ongoing costs should be factored into the overall budget and considered when assessing the long-term ROI. A typical annual maintenance cost could range from 15% to 25% of the initial software license fee, depending on the support package chosen.
Return on Investment (ROI) from Improved Inventory Management
The ROI of an inventory accounting program stems from several key improvements in inventory management. Accurate inventory tracking minimizes stockouts, reducing lost sales and customer dissatisfaction. Simultaneously, it prevents overstocking, reducing storage costs, obsolescence, and potential write-offs. Improved forecasting capabilities enable optimized purchasing, leading to lower procurement costs and better cash flow management. These benefits translate into increased profitability and a stronger bottom line.
Key Performance Indicators (KPIs)
Several KPIs can effectively measure the success of an inventory accounting program. These include:
- Inventory Turnover Rate: Measures how efficiently inventory is sold over a period. A higher turnover rate generally indicates better inventory management.
- Stockout Rate: Represents the percentage of times a product is unavailable when a customer demands it. A lower stockout rate demonstrates improved inventory accuracy and forecasting.
- Holding Costs: Encompasses storage, insurance, and obsolescence costs associated with maintaining inventory. Lower holding costs indicate efficient inventory management.
- Gross Profit Margin: Shows the profitability of sales after deducting the cost of goods sold. Improved inventory management can directly enhance gross profit margins.
Tracking these KPIs provides quantifiable evidence of the program’s impact on the business’s financial performance.
Hypothetical Scenario: Manual vs. Automated Inventory Management
Let’s consider a hypothetical scenario comparing manual inventory management to using an inventory accounting program.
- Manual Method: A small retail store manages inventory using spreadsheets. Inaccurate tracking leads to 10% stockouts, resulting in lost sales of $10,000 annually. Overstocking results in $5,000 in holding costs. Total annual losses: $15,000.
- Automated Method: The same store implements an inventory accounting program costing $3,000 initially and $500 annually for maintenance. Stockouts are reduced to 2%, resulting in $2,000 in lost sales. Holding costs are reduced to $2,
000. Total annual costs: $3,500 + $2,000 + $2,000 = $7,
500. Net savings: $15,000 – $7,500 = $7,500.
This scenario demonstrates how the initial investment in the inventory accounting program yields significant cost savings and a substantial return on investment within the first year. The long-term benefits are even more pronounced as the business grows and inventory complexity increases.
Security and Data Protection
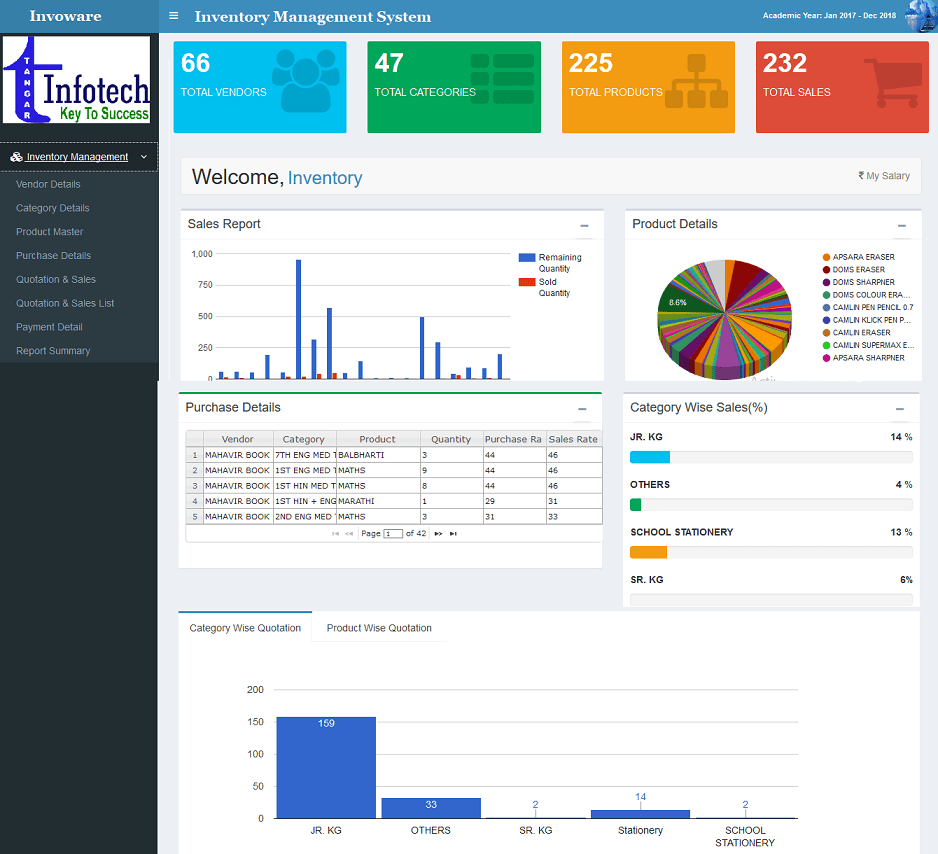
Protecting your inventory data is paramount to the success and integrity of your business. A robust security strategy safeguards not only your financial assets but also your operational efficiency and reputation. This section details the essential security measures necessary for a business inventory accounting program.Data breaches can lead to significant financial losses, operational disruptions, and damage to your company’s reputation.
Therefore, implementing comprehensive security measures is not merely a best practice, but a business necessity. This includes proactive measures to prevent unauthorized access and reactive measures to mitigate the impact of potential breaches.
Data Encryption
Data encryption is a crucial security measure that transforms your sensitive inventory data into an unreadable format, protecting it from unauthorized access even if a breach occurs. Strong encryption algorithms, such as AES-256, should be employed to encrypt data both at rest (stored on servers and databases) and in transit (during transmission over networks). This ensures that even if an attacker gains access to your data, they cannot decipher its contents without the decryption key.
Regular key rotation further enhances security by limiting the impact of any potential compromise of a single key.
Data Backups and Disaster Recovery Planning
Regular data backups are essential to ensure business continuity in case of unforeseen events like hardware failure, natural disasters, or cyberattacks. A comprehensive backup strategy should include multiple backup copies stored in different locations, ideally using both on-site and off-site storage. A well-defined disaster recovery plan Artikels the procedures for restoring data and systems in the event of a disaster, minimizing downtime and data loss.
This plan should be regularly tested and updated to reflect changes in your system and infrastructure. For example, a company might use a 3-2-1 backup strategy: three copies of data, on two different media, with one copy offsite.
Compliance Requirements
Compliance with relevant data privacy and security regulations is crucial. Regulations like GDPR (General Data Protection Regulation) in Europe and CCPA (California Consumer Privacy Act) in the United States impose strict requirements on how businesses collect, store, and process personal data. Compliance involves implementing appropriate technical and organizational measures to protect data, providing individuals with control over their data, and responding to data breach incidents in a timely and transparent manner.
Failure to comply can result in significant fines and legal repercussions.
User Access Control and Permissions
Implementing a robust user access control system is vital to limit access to sensitive inventory data only to authorized personnel. This involves assigning different roles and permissions to users based on their job responsibilities, ensuring that each user only has access to the data they need to perform their tasks. Multi-factor authentication (MFA) adds an extra layer of security by requiring users to provide multiple forms of authentication, such as a password and a one-time code generated by an authentication app, before gaining access to the system.
Regularly reviewing and updating user access permissions helps to maintain a secure environment and prevent unauthorized access. For instance, a warehouse manager might have access to all inventory data, while a sales representative only has access to data relevant to their sales region.
Future Trends in Inventory Accounting
The field of inventory accounting is undergoing a significant transformation, driven by rapid advancements in technology. These changes are not merely incremental improvements but represent a fundamental shift in how businesses manage and account for their inventory, leading to increased efficiency, reduced costs, and improved decision-making. The integration of emerging technologies is paving the way for a more accurate, real-time, and insightful approach to inventory management.The impact of technological advancements on inventory accounting programs is profound.
Real-time data capture and analysis are becoming the norm, allowing businesses to respond swiftly to changes in demand and supply. This increased visibility into inventory levels and movements leads to optimized stock control, minimizing waste and maximizing profitability. Furthermore, automation is streamlining many previously manual processes, freeing up valuable time and resources for more strategic initiatives.
Emerging Technologies and Their Impact
Artificial intelligence (AI), the Internet of Things (IoT), and blockchain technology are three key technologies reshaping inventory accounting. AI-powered predictive analytics can forecast demand with greater accuracy, enabling businesses to optimize their inventory levels and reduce carrying costs. IoT devices, such as RFID tags and sensors, provide real-time visibility into inventory location and condition, eliminating manual stocktaking and improving accuracy.
Blockchain technology offers enhanced security and transparency in the supply chain, ensuring the integrity of inventory data and reducing the risk of fraud. For example, a large retailer using AI to predict seasonal demand for winter coats could significantly reduce overstocking and associated storage costs compared to a retailer relying on historical data alone. Similarly, a manufacturing company using IoT sensors to monitor the temperature and humidity of its warehouse could prevent spoilage of temperature-sensitive goods, saving significant costs.
Finally, a company utilizing blockchain to track the movement of its goods across the supply chain can enhance traceability and reduce the risk of counterfeiting.
Adapting to Change and Leveraging New Opportunities
Businesses can adapt to these changes by investing in the necessary technology and training their employees to utilize it effectively. This includes implementing cloud-based inventory management systems, integrating IoT devices, and adopting AI-powered analytics tools. Furthermore, businesses should foster a data-driven culture, encouraging the use of data insights to inform inventory management decisions. By embracing these changes, businesses can gain a competitive advantage by improving efficiency, reducing costs, and enhancing customer satisfaction.
For instance, a small business adopting a cloud-based inventory system can access real-time inventory data from any location, improving responsiveness to customer orders and reducing the risk of stockouts.
Potential Future Features of Advanced Inventory Accounting Software
The future of inventory accounting software promises even greater sophistication and integration. Several potential features could transform inventory management:
- Predictive Inventory Optimization: Software that not only forecasts demand but also automatically adjusts ordering quantities based on real-time data and changing market conditions.
- Automated Inventory Reconciliation: Systems that automatically reconcile physical inventory counts with recorded data, minimizing discrepancies and improving accuracy.
- AI-Powered Quality Control: Integration of AI and machine learning to automatically detect and flag defective or damaged goods during the inventory process.
- Advanced Reporting and Analytics Dashboards: Interactive dashboards providing comprehensive insights into inventory performance, including key metrics such as inventory turnover, carrying costs, and stockout rates.
- Enhanced Supply Chain Visibility: Integration with supply chain partners to provide a holistic view of the entire inventory lifecycle, from procurement to delivery.
- Blockchain-Based Inventory Tracking: Secure and transparent tracking of inventory throughout the supply chain using blockchain technology.
Closing Summary
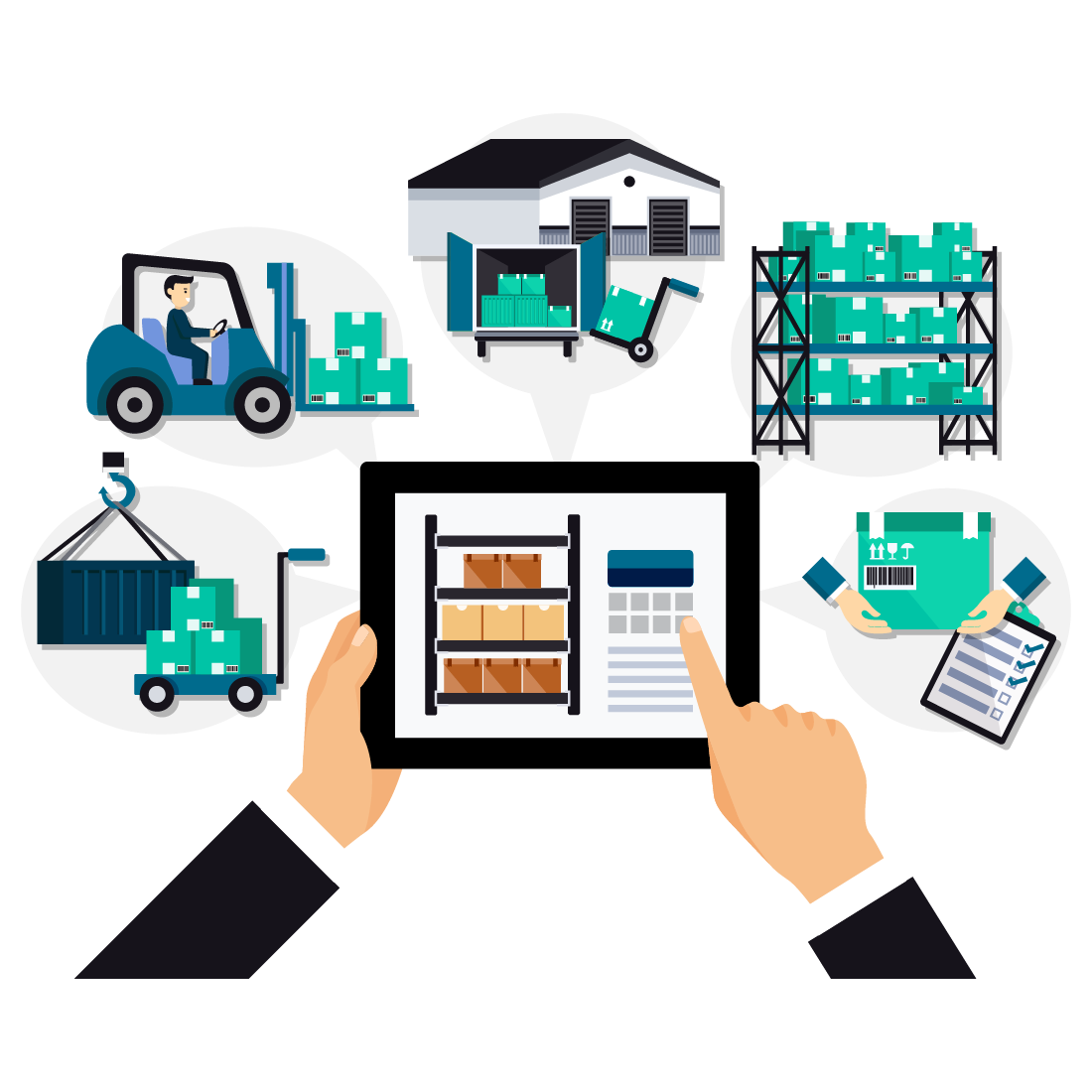
Implementing a business inventory accounting program represents a significant investment in efficiency and accuracy. By understanding the various methods, integrating the program effectively, and leveraging its reporting capabilities, businesses can gain valuable insights into their inventory performance. The ongoing evolution of technology, incorporating AI and IoT, promises even more sophisticated solutions in the future, further enhancing the value and strategic importance of these programs for businesses of all sizes.
Careful planning and selection are key to maximizing the return on investment and achieving optimal inventory management.
FAQ Overview
What is the difference between FIFO and LIFO?
FIFO (First-In, First-Out) assumes the oldest inventory is sold first. LIFO (Last-In, First-Out) assumes the newest inventory is sold first. These methods affect cost of goods sold and inventory valuation differently.
How secure is my data in an inventory accounting program?
Reputable programs employ robust security measures, including encryption, access controls, and regular backups. Choosing a program with strong security protocols and adhering to best practices is crucial for data protection.
Can I integrate my inventory program with other business software?
Many inventory accounting programs offer seamless integration with accounting software, CRM systems, and e-commerce platforms, streamlining data flow and enhancing efficiency.
What are the common reporting features available?
Common reports include stock levels, sales trends, profitability analysis, slow-moving inventory reports, and custom reports tailored to specific business needs.