Business inventory accounting tool streamlines inventory management, offering businesses of all sizes a powerful way to track stock, manage costs, and boost profitability. From small startups to large enterprises, efficient inventory control is crucial for success, and the right tool can significantly enhance operational efficiency and financial accuracy. This guide explores the key features, benefits, and considerations involved in selecting and implementing such a tool.
We’ll delve into various inventory costing methods (FIFO, LIFO, weighted average), discuss the importance of integration with accounting software, and highlight the analytical power of robust reporting features. Understanding data security and cost considerations is also crucial, and we’ll provide practical advice on optimizing your investment in an inventory accounting tool. Ultimately, mastering inventory management empowers businesses to make data-driven decisions, reduce waste, and maximize profits.
Defining Business Inventory Accounting Tools
Business inventory accounting tools are software applications designed to streamline and automate the process of tracking and managing a company’s inventory. These tools offer a comprehensive solution for businesses of all sizes, providing real-time visibility into stock levels, helping optimize ordering, and ultimately boosting profitability. They move beyond simple spreadsheets, offering sophisticated features for accurate accounting and efficient inventory control.Inventory accounting tools are crucial for accurate financial reporting, preventing stockouts and overstocking, and improving overall operational efficiency.
They provide a centralized system for managing all aspects of inventory, from purchasing and receiving to sales and returns. This leads to better decision-making, reduced costs, and improved customer satisfaction.
Core Functionalities of Business Inventory Accounting Tools
A core functionality of business inventory accounting tools is the accurate tracking of inventory levels. This involves recording incoming and outgoing inventory items, adjusting for discrepancies, and generating reports on current stock levels. Beyond this, these tools typically integrate with accounting software, providing seamless data transfer for financial reporting. Automated features such as low-stock alerts, reorder point calculations, and demand forecasting also help businesses proactively manage their inventory.
Furthermore, many tools offer robust reporting capabilities, providing insights into sales trends, inventory turnover rates, and other key performance indicators (KPIs).
Types of Businesses Benefiting from Inventory Accounting Tools
A wide range of businesses benefit from using inventory accounting tools. Retailers, wholesalers, manufacturers, and distributors all rely on these tools to manage their inventory effectively. Even small businesses with limited inventory can benefit from the organization and efficiency these tools provide. For example, a small bakery might use an inventory tool to track flour, sugar, and other essential ingredients, ensuring they always have enough on hand without overstocking and wasting perishable goods.
Larger businesses, such as a national clothing retailer, would utilize more sophisticated tools to manage vast quantities of inventory across multiple locations. The scalability of these tools makes them adaptable to businesses of all sizes and complexities.
Common Features of Inventory Management Software
Several common features are found in various inventory management software solutions. These include barcode or RFID scanning for efficient inventory tracking, real-time inventory visibility dashboards providing an up-to-the-minute overview of stock levels, automated purchase order generation based on pre-set reorder points, detailed reporting and analytics capabilities for identifying trends and optimizing inventory strategies, and integration with other business systems like accounting software, e-commerce platforms, and point-of-sale (POS) systems.
Some advanced tools also incorporate features like lot tracking for managing perishable goods or serialized items, and forecasting tools to predict future demand.
Comparison of Inventory Accounting Tools
Below is a comparison of three different inventory accounting tools, highlighting their pricing, features, and user interface. Note that pricing can vary based on the number of users, features selected, and other factors.
Tool | Pricing (Monthly) | Key Features | User Interface |
---|---|---|---|
InventoryPro | $99 – $499+ | Barcode scanning, real-time inventory tracking, reporting, integration with accounting software | Intuitive, user-friendly dashboard; easy navigation |
StockManager | $49 – $249+ | Real-time inventory updates, automated ordering, sales forecasting, multi-location support | Clean and modern design; customizable dashboards |
InvenTrack | $29 – $199+ | Basic inventory tracking, reporting, simple user interface, suitable for smaller businesses | Straightforward; may lack advanced features of other tools |
Inventory Management Methods and Procedures
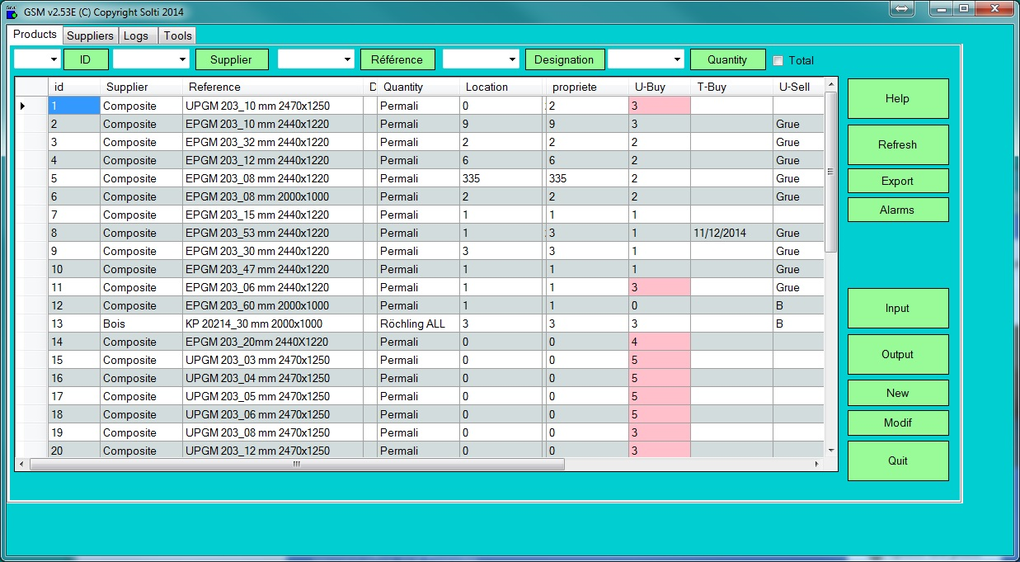
Effective inventory management is crucial for maintaining profitability and ensuring smooth business operations. Understanding different costing methods and implementing robust tracking procedures are key components of this process. This section will Artikel several inventory management methods and provide practical guidance on best practices.
First-In, First-Out (FIFO) Inventory Costing Method
FIFO assumes that the oldest inventory items are sold first. This method aligns with the natural flow of goods in many businesses. The cost of goods sold (COGS) is calculated using the cost of the oldest inventory, while the ending inventory reflects the cost of the most recently acquired items. For example, if a company purchases 100 units at $10 each and later 150 units at $12 each, and sells 120 units, the COGS under FIFO would be (100 units
- $10) + (20 units
- $12) = $1240. The value of the remaining inventory would be (130 units
- $12) = $1560. During periods of inflation, FIFO generally results in a lower COGS and a higher net income compared to LIFO.
Last-In, First-Out (LIFO) Inventory Costing Method
LIFO operates on the opposite principle to FIFO: the most recently acquired inventory items are assumed to be sold first. Using the same example as above, the COGS under LIFO would be (150 units
- $12) + (30 units
- $10) = $2100. The value of the remaining inventory would be (70 units
- $10) = $700. During inflationary periods, LIFO generally results in a higher COGS and a lower net income, often leading to lower tax liabilities. It’s important to note that LIFO is not permitted under IFRS (International Financial Reporting Standards).
Weighted-Average Cost Method for Inventory Valuation
The weighted-average cost method calculates the average cost of all inventory items available for sale during a period. This average cost is then used to determine both the COGS and the value of ending inventory. To calculate the weighted-average cost, the total cost of goods available for sale is divided by the total number of units available for sale.
Continuing with the previous example, the weighted-average cost would be (($1000 + $1800) / 250 units) = $11.20 per unit. The COGS would then be (120 units
- $11.20) = $1344, and the value of the remaining inventory would be (130 units
- $11.20) = $1456. This method simplifies inventory valuation and reduces the impact of price fluctuations.
Best Practices for Accurate Inventory Tracking and Record-Keeping
Maintaining accurate inventory records is essential for effective inventory management. This requires implementing a robust system that includes:
- Regular cycle counting: Conducting frequent counts of a small portion of inventory to identify discrepancies early.
- Barcoding or RFID tagging: Utilizing technology to track inventory movement and location.
- Real-time inventory updates: Ensuring that inventory records are updated immediately after each transaction.
- Automated inventory management system: Implementing software to streamline inventory tracking and reporting.
- Regular reconciliation: Comparing physical inventory counts with recorded inventory levels to identify and correct discrepancies.
These practices minimize errors, reduce waste, and improve overall efficiency.
Performing a Physical Inventory Count: A Step-by-Step Guide
A physical inventory count is a crucial process for verifying the accuracy of inventory records. Here’s a step-by-step guide:
- Planning and Preparation: Define the scope, schedule the count, gather necessary supplies (counting sheets, scanners, etc.), and train personnel.
- Counting the Inventory: Organize the warehouse or storage area logically, assign teams to specific areas, and use a systematic counting method to avoid double-counting or omissions. Clearly label counted items.
- Reconciliation: Compare the physical count results with the inventory records. Investigate any significant discrepancies.
- Reporting and Analysis: Document the findings, identify areas for improvement in inventory management, and take corrective actions.
Checklist for Implementing a New Inventory Accounting Tool
Implementing a new inventory accounting tool requires careful planning and execution. Use this checklist to ensure a smooth transition:
- Define requirements: Identify specific needs and functionalities required from the new tool.
- Research and select a tool: Evaluate different options based on features, cost, and integration capabilities.
- Data migration: Plan and execute the transfer of existing inventory data to the new system.
- Training: Provide comprehensive training to staff on using the new tool.
- Testing: Thoroughly test the new system before full implementation to identify and resolve any issues.
- Go-live: Schedule and execute the implementation of the new tool.
- Post-implementation review: Evaluate the effectiveness of the new tool and make necessary adjustments.
Integration with Accounting Software
Integrating your inventory accounting tool with your general ledger software is crucial for maintaining accurate financial records and streamlining your business operations. A seamless integration eliminates the need for manual data entry, reducing errors and saving valuable time. This integration allows for a holistic view of your business finances, providing a more accurate picture of profitability and inventory health.Data synchronization between inventory and accounting systems typically occurs through automated data transfers.
The inventory tool sends transactional data, such as purchase orders, sales invoices, and inventory adjustments, to the accounting software. This data is then automatically posted to the relevant general ledger accounts. This process usually happens in real-time or on a scheduled basis, depending on the system’s configuration. The specific method used depends on the integration method employed (API, file transfer, etc.).
Data Synchronization Mechanisms
Efficient data synchronization hinges on the chosen method. Common approaches include Application Programming Interfaces (APIs), which enable real-time data exchange, and file-based transfers (like CSV or XML files), which involve scheduled data imports. Real-time synchronization via APIs offers the most up-to-date information, while file-based transfers are simpler to implement but may introduce slight delays. The choice depends on factors such as technical capabilities and desired update frequency.
For instance, a small business might opt for scheduled file transfers, while a larger enterprise might prioritize real-time API integration for immediate data visibility.
Challenges in Software System Integration
Integrating different software systems can present various challenges. Compatibility issues between systems, differing data structures, and the need for custom coding or middleware solutions are common hurdles. Security concerns surrounding data transfer also require careful consideration. For example, integrating a legacy accounting system with a modern inventory management tool might necessitate extensive customization or the use of a third-party integration platform to bridge the gap between differing data formats and communication protocols.
Moreover, ensuring data security during the transfer process is paramount, requiring robust encryption and authentication measures.
Configuring Automatic Accounting Record Updates
Configuring an inventory accounting tool to automatically update accounting records typically involves several steps. First, you need to select the appropriate integration method (API or file transfer). Next, you must establish a connection between the two systems, providing necessary authentication credentials. Finally, you configure the data fields to be synchronized and set up the update schedule. For example, to automate the posting of sales transactions, you would map the inventory tool’s sales invoice data to the accounting software’s sales accounts and inventory accounts.
This setup ensures that when a sale is recorded in the inventory system, the corresponding entries are automatically generated in the accounting system, eliminating manual data entry.
Examples of Common Accounting Software Integrations
Many inventory accounting tools offer pre-built integrations with popular accounting software packages. Common examples include integrations with QuickBooks, Xero, and Sage. These integrations often streamline the setup process and ensure compatibility. For example, an inventory tool might offer a dedicated QuickBooks connector, allowing users to seamlessly sync inventory data with their QuickBooks account. This reduces the manual effort required to maintain accurate financial records and enhances the overall efficiency of the accounting process.
Similarly, integrations with Xero and Sage offer comparable functionalities, tailoring the integration process to the specific features of each accounting platform.
Reporting and Analysis Capabilities
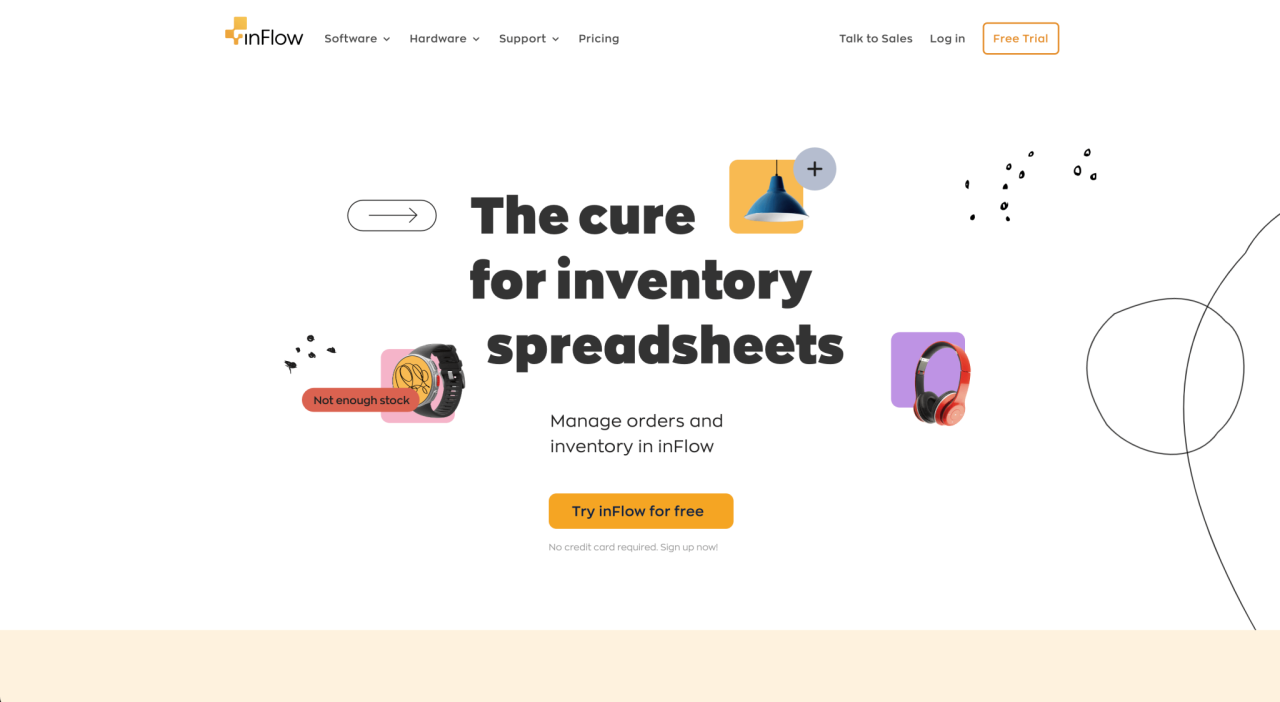
Effective inventory accounting tools provide robust reporting and analysis capabilities, offering crucial insights into inventory performance and overall business health. These reports empower businesses to make data-driven decisions, optimize inventory levels, and ultimately improve profitability. Understanding the types of reports available and how to interpret the data is key to maximizing the value of your inventory management system.Inventory accounting tools generate a variety of reports to provide a comprehensive overview of inventory levels, costs, and sales.
These reports are invaluable for identifying trends, pinpointing areas for improvement, and informing strategic decisions related to purchasing, pricing, and sales forecasting. Key performance indicators (KPIs) derived from these reports provide a quantifiable measure of inventory management efficiency.
Types of Inventory Reports
Inventory accounting tools typically generate several key report types. These include inventory valuation reports, which detail the value of inventory at a specific point in time using different costing methods (FIFO, LIFO, weighted average). Sales reports track sales data, including quantities sold, revenue generated, and associated costs. Stock level reports show current inventory levels for each item, highlighting potential stockouts or overstocking situations.
Other reports might include demand forecasting reports, which predict future inventory needs based on historical sales data, and inventory turnover reports, showing how efficiently inventory is being sold.
Using Reports for Informed Business Decisions
The reports generated by inventory accounting tools are not merely data dumps; they are powerful tools for decision-making. For example, a consistently low inventory turnover ratio might indicate slow-moving or obsolete inventory, prompting a review of pricing strategies or product offerings. Conversely, high inventory turnover could suggest strong demand but also potential stockout risks if not managed properly.
Analyzing sales reports in conjunction with stock level reports allows businesses to optimize their ordering processes, ensuring sufficient inventory without excessive holding costs. By tracking key metrics over time, businesses can identify trends and make proactive adjustments to their inventory management strategies.
Key Performance Indicators (KPIs) for Inventory Management
Several key performance indicators (KPIs) are commonly used to assess the efficiency and effectiveness of inventory management. These include:
- Inventory Turnover Ratio: This measures how many times inventory is sold and replaced during a specific period (e.g., annually). A higher ratio generally indicates efficient inventory management.
- Gross Profit Margin: This shows the profitability of sales after deducting the cost of goods sold (COGS). Analyzing this in conjunction with inventory turnover can highlight pricing and cost control opportunities.
- Days Sales of Inventory (DSI): This represents the average number of days it takes to sell inventory. A lower DSI suggests faster inventory turnover and potentially less risk of obsolescence.
- Inventory Holding Costs: This encompasses all costs associated with storing and maintaining inventory, including storage space, insurance, and potential spoilage or obsolescence. Minimizing these costs is crucial for profitability.
Sample Inventory Valuation Report
The following table presents a hypothetical inventory valuation report using the FIFO (First-In, First-Out) method:
Item | Quantity | Unit Cost | Total Value |
---|---|---|---|
Widget A | 100 | $10 | $1000 |
Widget B | 50 | $15 | $750 |
Widget C | 200 | $5 | $1000 |
Total | 350 | $2750 |
Identifying Slow-Moving or Obsolete Inventory
By analyzing inventory reports, businesses can readily identify slow-moving or obsolete inventory. Reports showing low turnover ratios for specific items, combined with long storage times, indicate potential problems. Regularly reviewing these reports allows for proactive measures, such as discounts, promotions, or even write-offs to minimize losses associated with unsold inventory. The ability to filter and sort reports by various criteria (e.g., sales velocity, last purchase date, etc.) significantly simplifies the identification of these items.
Security and Data Management
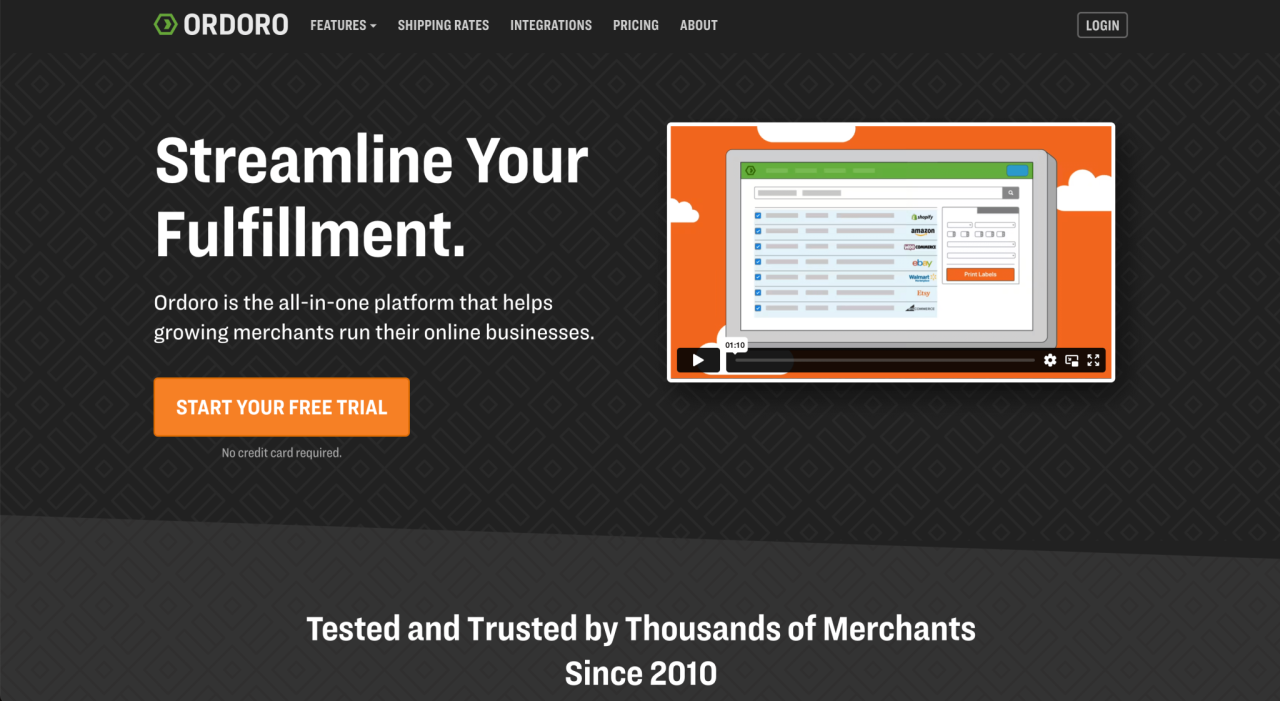
The security of your inventory data is paramount. A breach can lead to significant financial losses, operational disruptions, and damage to your reputation. Robust security measures are therefore essential for any inventory accounting tool, ensuring the confidentiality, integrity, and availability of your inventory information. This section details crucial aspects of data security and management within the context of inventory accounting software.Data security measures in inventory accounting tools are multifaceted and should be designed to address various potential threats.
These measures aim to protect your sensitive inventory data from unauthorized access, modification, or destruction. Implementing a comprehensive security strategy requires a multi-layered approach, combining technical controls with robust operational procedures.
Access Controls
Access controls restrict who can view, modify, or delete inventory data. This is typically achieved through user roles and permissions. For example, a warehouse manager might have access to update inventory levels, while an accountant may only have read-only access to reports. Strong passwords and multi-factor authentication (MFA) further enhance security by requiring multiple forms of verification before granting access.
Regular audits of user access rights help ensure that permissions remain appropriate and that no unauthorized access is granted. For instance, an employee leaving the company should have their access revoked immediately.
Data Encryption
Data encryption transforms data into an unreadable format, protecting it from unauthorized access even if a breach occurs. Encryption can be implemented at various levels, including data at rest (stored on servers or databases) and data in transit (being transmitted over a network). Strong encryption algorithms, such as AES-256, are crucial for robust protection. The use of encryption keys, carefully managed and protected, is paramount for data decryption.
Regular key rotation helps mitigate the risk of compromised keys.
Data Backup and Recovery Procedures
Regular data backups are critical for business continuity. A comprehensive backup strategy should include both on-site and off-site backups, preferably using different storage mediums. Regular testing of the backup and recovery process is crucial to ensure its effectiveness. The frequency of backups should be determined based on the criticality of the data and the rate of changes.
For example, daily backups might be necessary for high-volume inventory systems, while weekly backups may suffice for less dynamic systems. The recovery point objective (RPO) and recovery time objective (RTO) should be defined and documented to guide the backup and recovery strategy.
Potential Security Threats and Mitigation Strategies
Several threats can compromise inventory data security. Malware, such as viruses and ransomware, can encrypt or destroy data, rendering it inaccessible. Phishing attacks can trick users into revealing their credentials. Insider threats, from malicious or negligent employees, can also pose a significant risk. Mitigation strategies include installing and regularly updating antivirus software, implementing robust security awareness training for employees, and regularly reviewing system logs for suspicious activity.
Network security measures, such as firewalls and intrusion detection systems, help prevent unauthorized access. Regular security audits and penetration testing can identify vulnerabilities and weaknesses in the system.
Data Security Policy
A comprehensive data security policy should Artikel procedures for user access management, data encryption, backup and recovery, incident response, and security awareness training. The policy should be clearly communicated to all employees and regularly reviewed and updated. The policy should also define roles and responsibilities for data security. For example, it might specify who is responsible for conducting regular security audits or responding to security incidents.
Regular compliance checks against the policy are essential to maintain the security posture of the inventory accounting system. The policy should also include procedures for handling data breaches, including notification procedures and remedial actions.
Cost Considerations and ROI
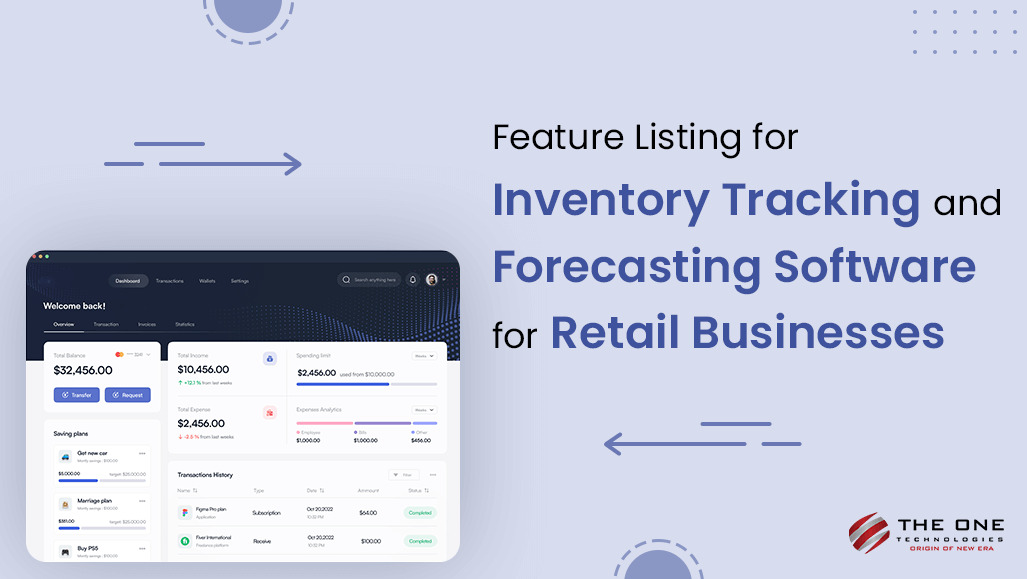
Implementing an inventory accounting tool requires careful consideration of various costs and a clear understanding of the potential return on investment. This section details the financial aspects, enabling informed decision-making regarding the selection and utilization of such a tool. A comprehensive cost-benefit analysis is crucial for justifying the expense and ensuring optimal resource allocation.
Software Licensing Costs, Business inventory accounting tool
Software licenses represent a significant initial investment. Costs vary widely depending on the chosen software, the number of users, and the features included. Some tools offer tiered pricing based on the scale of the business’s inventory, while others charge a flat fee per user. For example, a small business might find a suitable solution for a few hundred dollars per year, whereas a large enterprise could spend tens of thousands annually.
It’s crucial to obtain detailed pricing information from vendors and factor in any potential upgrade or maintenance fees.
Training and Implementation Costs
The cost of training employees to use the new inventory accounting software should not be overlooked. This includes the time spent on training sessions, the cost of training materials, and the potential loss of productivity during the learning curve. Effective training minimizes errors and maximizes the tool’s efficiency, justifying the investment. Consider whether the vendor offers training resources, or if you need to hire external consultants for specialized support.
A realistic budget should allocate for both internal and external training needs.
Ongoing Support and Maintenance Costs
Ongoing support and maintenance are vital for ensuring the smooth operation of the inventory accounting tool. This may include technical support, software updates, and bug fixes. Vendors often offer different levels of support packages, with varying costs. It’s important to evaluate the level of support needed based on your technical capabilities and the complexity of the software.
Consider the potential costs of downtime due to technical issues and weigh that against the cost of a robust support package.
Return on Investment (ROI) Calculation
Calculating the ROI for an inventory accounting tool involves comparing the costs of implementation and maintenance against the benefits realized. A simplified ROI calculation can be expressed as:
ROI = (Net Benefits – Total Costs) / Total Costs
Net benefits can include reduced inventory holding costs, minimized stockouts, improved inventory accuracy, and increased efficiency. Total costs encompass software licensing, training, implementation, and ongoing support. For example, if a company invests $10,000 in a new inventory system and realizes $20,000 in cost savings within a year, the ROI would be 100%.
Cost Comparison of Different Inventory Accounting Tools
Comparing the costs and benefits of different tools requires a thorough analysis of features, pricing, and support options. Consider factors such as scalability, integration capabilities, and reporting functionalities. Spreadsheet software offers a basic, cost-effective solution for small businesses with minimal inventory. However, more sophisticated solutions with advanced features such as barcode scanning and real-time inventory tracking may be more suitable for larger businesses and come with higher price tags.
A clear understanding of your business needs and scale is critical for selecting a tool that offers the right balance of functionality and cost.
Best Practices for Optimizing Tool Use to Reduce Costs
Optimizing the use of an inventory accounting tool can significantly reduce costs. This includes proper training of employees to ensure accurate data entry and efficient use of the software’s features. Regular data backups and security measures prevent data loss and associated costs. Integrating the tool with other business systems streamlines workflows and minimizes manual data entry, reducing errors and saving time.
Finally, periodic reviews of the tool’s performance and functionality can identify areas for improvement and cost optimization.
Cost-Benefit Analysis Template
Item | Cost | Benefit |
---|---|---|
Software License | [Insert Cost] | [Insert Benefit, e.g., Improved Inventory Accuracy] |
Training | [Insert Cost] | [Insert Benefit, e.g., Reduced Errors] |
Implementation | [Insert Cost] | [Insert Benefit, e.g., Streamlined Processes] |
Support & Maintenance | [Insert Cost] | [Insert Benefit, e.g., System Uptime] |
Total Costs | [Sum of Costs] | [Sum of Benefits] |
Net Benefit | [Sum of Benefits – Sum of Costs] | |
ROI | [(Sum of Benefits – Sum of Costs) / Sum of Costs] |
Last Word: Business Inventory Accounting Tool
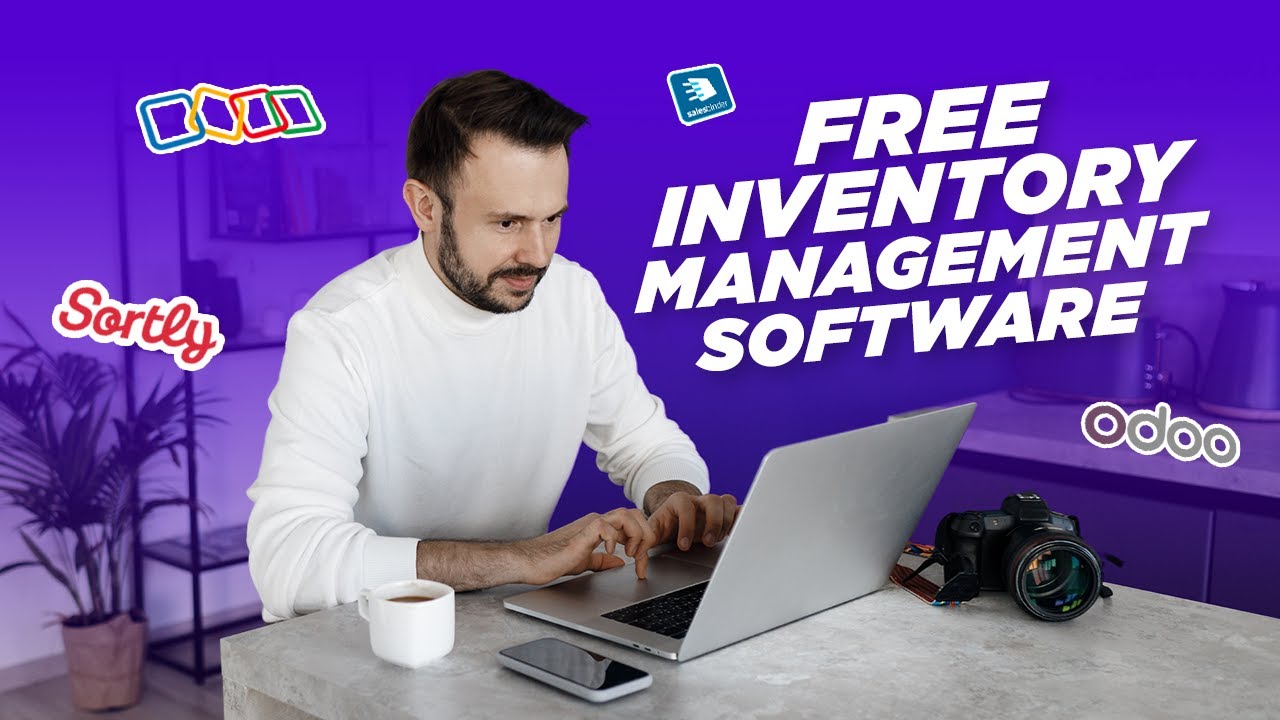
Implementing a business inventory accounting tool represents a significant step towards enhancing operational efficiency and financial control. By carefully considering the various factors discussed—from choosing the right software and understanding costing methods to prioritizing data security and calculating ROI—businesses can optimize their inventory management processes. The resulting improvements in accuracy, efficiency, and informed decision-making ultimately contribute to a healthier bottom line and sustainable growth.
FAQ Compilation
What are the legal implications of inaccurate inventory records?
Inaccurate inventory records can lead to issues with tax reporting, potentially resulting in penalties or audits. They can also impact financial reporting accuracy and investor confidence.
How often should I perform a physical inventory count?
The frequency depends on your business and inventory turnover rate. Some businesses perform counts monthly, while others do them quarterly or annually. High-value or perishable items may require more frequent counts.
Can I use a spreadsheet for inventory management?
Spreadsheets can work for very small businesses, but they become cumbersome and error-prone as inventory grows. Dedicated inventory accounting tools offer superior scalability, accuracy, and reporting capabilities.
What is the typical implementation timeline for an inventory accounting tool?
Implementation time varies depending on the complexity of the system and your business’s needs. Expect a few weeks to several months, including data migration, training, and testing.