Business Inventory Checklist: Efficient inventory management is the backbone of a successful business, regardless of size or industry. From the bustling kitchen of a popular restaurant meticulously tracking its daily supplies to the vast warehouses of an e-commerce giant managing thousands of products, understanding and optimizing inventory is crucial for profitability and growth. This guide delves into the essential components of a robust business inventory checklist, offering practical strategies and insights to streamline your processes and enhance your bottom line.
We will explore various inventory management techniques, including FIFO, LIFO, and weighted average cost, highlighting their advantages and disadvantages. The importance of accurate inventory tracking, addressing discrepancies, and leveraging technology for improved efficiency will be thoroughly examined. We’ll also discuss the role of data visualization in making informed decisions and ensuring legal and regulatory compliance.
Defining Business Inventory
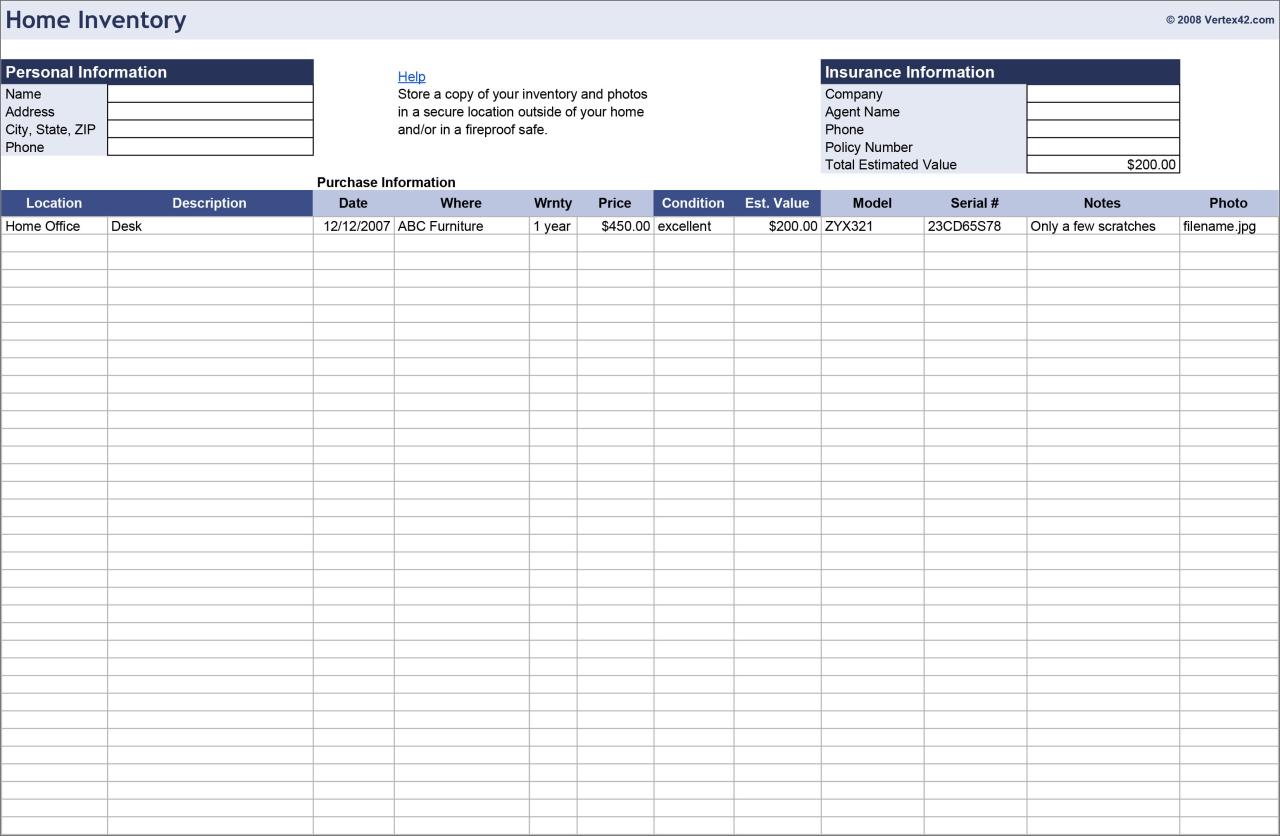
Inventory represents the goods and materials a business holds for the purpose of sale or use in production. Understanding and managing your inventory is crucial for profitability and operational efficiency. Effective inventory management ensures you have enough stock to meet customer demand without tying up excessive capital in unsold goods.
Different types of business inventory exist, each serving a unique purpose within the supply chain. Raw materials are the basic inputs used in the production process. Work-in-progress (WIP) refers to partially finished goods undergoing manufacturing. Finished goods are completed products ready for sale. Finally, Maintenance, Repair, and Operations (MRO) inventory includes supplies necessary for keeping equipment and facilities running smoothly.
Types of Business Inventory
Accurate inventory tracking is vital for various business models. For retailers, precise inventory levels prevent stockouts (lost sales due to unavailability) and overstocking (excess inventory leading to storage costs and potential obsolescence). Manufacturers rely on accurate inventory data to schedule production efficiently, minimizing waste and delays. Service businesses, while often less inventory-intensive, still need to track supplies and equipment to ensure service continuity.
Accurate data allows for better forecasting, improved resource allocation, and optimized pricing strategies across all business models.
Examples of Businesses with Varying Inventory Needs
Consider the contrasting inventory needs of a restaurant versus an online retailer. A restaurant’s inventory is perishable, requiring frequent replenishment and careful management to minimize waste. Their inventory primarily consists of food ingredients, beverages, and disposable supplies. An online retailer, on the other hand, deals with a wider variety of goods, potentially requiring significant warehousing space and sophisticated logistics for managing inventory across various locations and fulfillment centers.
The online retailer’s inventory may range from electronics and clothing to books and home goods, encompassing a much larger scale and diverse product range.
Comparison of Perpetual and Periodic Inventory Systems
Businesses employ different methods to track inventory. Two common approaches are perpetual and periodic inventory systems. The choice depends on factors such as business size, inventory complexity, and budget constraints. Each system has its own advantages and disadvantages.
Feature | Perpetual Inventory System | Periodic Inventory System |
---|---|---|
Inventory Tracking | Continuous tracking of inventory levels using point-of-sale (POS) systems or similar technologies. | Inventory counted at fixed intervals (e.g., monthly, quarterly). |
Cost of Implementation | Higher initial investment in technology and software. | Lower initial investment; simpler to implement. |
Accuracy | Generally more accurate, providing real-time inventory data. | Less accurate; relies on physical counts, which can be time-consuming and prone to errors. |
Cost of Goods Sold (COGS) Calculation | COGS calculated continuously. | COGS calculated at the end of the period based on the physical count. |
Components of a Comprehensive Checklist
A robust business inventory checklist is crucial for efficient operations and accurate financial reporting. It ensures that all assets are accounted for, preventing losses due to theft, damage, or obsolescence. A well-designed checklist streamlines the inventory process, saving time and resources while improving overall accuracy.Regularly scheduled inventory counts are vital for maintaining an accurate record of your inventory levels.
Inaccurate inventory data can lead to significant problems, such as stockouts, overstocking, and ultimately, financial losses. Consistent inventory checks allow businesses to identify discrepancies early on, enabling timely adjustments to purchasing and sales strategies.
Inventory Checklist Elements
A comprehensive inventory checklist should include details about each item in your inventory. This includes a unique identifier (e.g., SKU), a description of the item, its location within your warehouse or storage space, the quantity on hand, and its current condition. Additionally, it’s beneficial to include the item’s cost, purchase date, and supplier information for better tracking and analysis.
Including details such as expiration dates for perishable goods or warranty information for equipment is also important.
Scheduled Inventory Counts and Their Significance
Regularly scheduled inventory counts, whether daily, weekly, monthly, or annually, are essential for maintaining accurate inventory records. The frequency depends on the nature of the business and the type of inventory. For example, a grocery store might conduct daily counts of perishable items, while a furniture store might perform monthly counts. These regular counts help identify discrepancies, prevent stockouts, and optimize ordering practices.
The data collected allows for analysis of sales trends, helping businesses predict future demand and adjust inventory levels accordingly. For instance, a consistent increase in demand for a specific product would prompt an increase in its stock levels. Conversely, consistently low sales might indicate a need to reduce stock to avoid holding excess inventory.
Integrating Physical and Digital Inventory Tracking
Modern inventory management systems effectively combine physical and digital methods. A physical inventory count involves manually checking and counting items. This is often done using a barcode scanner or handheld device to record data directly into the system. Simultaneously, a digital system maintains a real-time record of inventory levels. This system updates automatically when items are added or removed.
For example, a point-of-sale (POS) system automatically deducts items from inventory as they are sold. The combination of physical and digital methods provides a robust system of checks and balances, minimizing errors and enhancing accuracy. Discrepancies between physical counts and digital records highlight potential issues that need immediate attention.
Organizing and Storing the Inventory Checklist
Effective organization and storage of the inventory checklist are crucial for easy access and efficient inventory management. A well-structured checklist should be easily searchable and readily available to authorized personnel. Digital storage using cloud-based platforms or a secure internal server provides easy access and facilitates collaboration among team members. Regular backups are crucial to prevent data loss.
For physical checklists, a designated storage location with clear labeling and indexing is necessary. Using a filing system that is logical and easily understandable ensures that checklists are quickly retrievable when needed. Version control is also important to track changes and ensure everyone uses the most up-to-date version.
Inventory Management Techniques
Effective inventory management is crucial for a business’s profitability and operational efficiency. Choosing the right inventory costing method significantly impacts the reported cost of goods sold (COGS) and, consequently, the gross profit. This section will explore several common inventory management techniques, highlighting their advantages, disadvantages, and effects on profitability.
First-In, First-Out (FIFO)
FIFO assumes that the oldest inventory items are sold first. This method aligns well with the actual flow of goods for perishable items or those with short shelf lives. In periods of inflation, FIFO results in a lower cost of goods sold and a higher gross profit because older, cheaper inventory is being sold.
- Advantage: Reflects the actual physical flow of goods for many businesses, leading to a more accurate valuation of ending inventory.
- Advantage: Results in higher gross profit during inflationary periods.
- Disadvantage: Can lead to higher taxes in inflationary periods due to higher reported profits.
- Example: A bakery uses FIFO. The first loaves of bread baked are the first sold. If flour prices increase, the cost of goods sold will reflect the lower cost of the older flour, boosting reported profits.
Last-In, First-Out (LIFO)
LIFO assumes that the newest inventory items are sold first. This method is generally used for non-perishable goods. During inflationary periods, LIFO leads to a higher cost of goods sold and lower gross profit because the more expensive, recently purchased inventory is being expensed.
- Advantage: Reduces taxable income during inflationary periods, resulting in lower tax liabilities.
- Advantage: Better reflects the current cost of replacing inventory.
- Disadvantage: Can lead to a lower gross profit and potentially undervalue ending inventory.
- Disadvantage: Not permitted under IFRS (International Financial Reporting Standards).
- Example: A hardware store using LIFO would report the cost of its most recently purchased nails as the cost of goods sold, even if older, cheaper nails remain in stock.
Weighted Average Cost
The weighted average cost method calculates the average cost of all inventory items available for sale during a period. This average cost is then used to determine the cost of goods sold and the value of ending inventory. This method smooths out price fluctuations and simplifies accounting.
- Advantage: Simple to calculate and understand.
- Advantage: Smooths out price fluctuations, providing a more stable cost of goods sold.
- Disadvantage: May not accurately reflect the actual cost of goods sold, especially during periods of significant price changes.
- Example: A retailer purchases 10 units at $10 each and later 20 units at $12 each. The weighted average cost is (($10
– 10) + ($12
– 20)) / 30 = $11.33 per unit.
Addressing Inventory Discrepancies
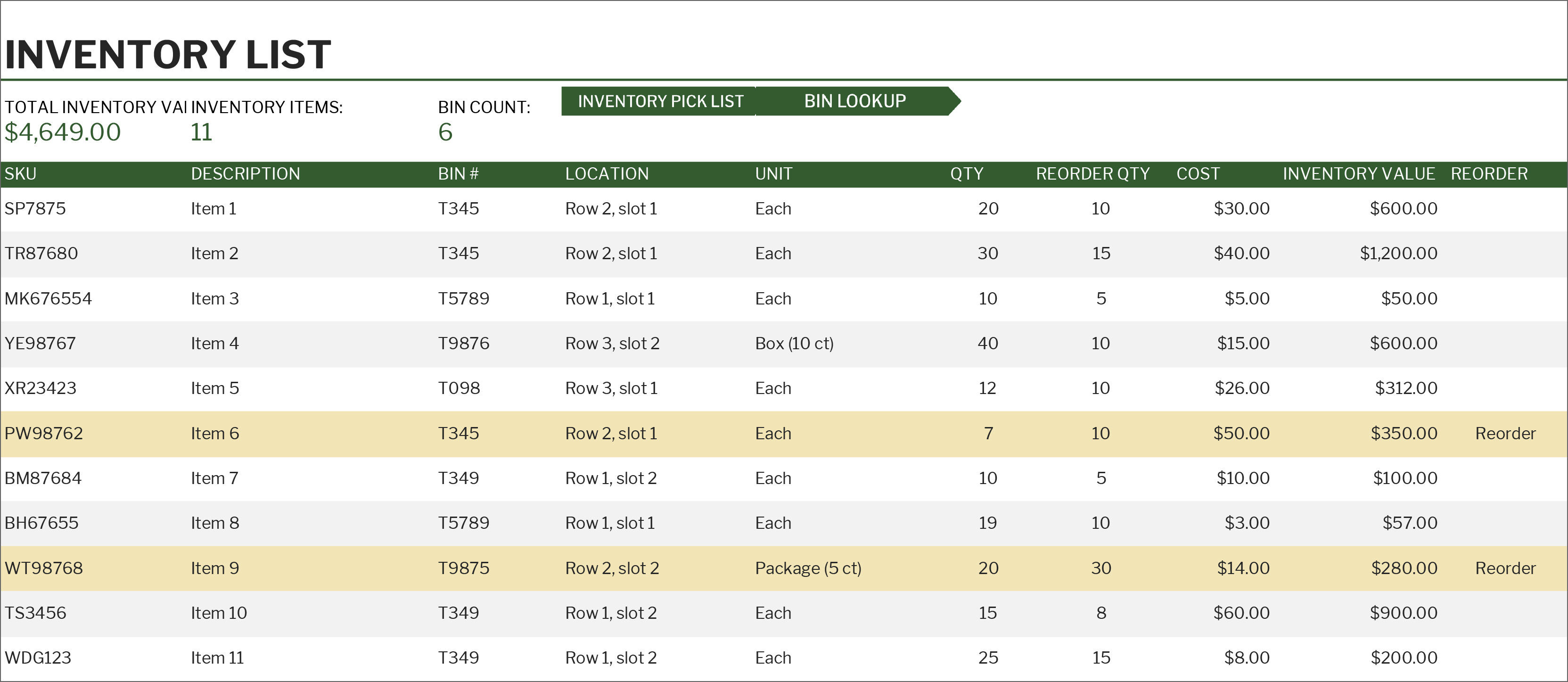
Inventory discrepancies, the difference between recorded inventory and actual physical inventory, are a common challenge for businesses of all sizes. These discrepancies can lead to inaccurate financial reporting, lost sales opportunities due to stockouts, and increased costs associated with managing excess inventory. Understanding the causes, implementing effective investigation methods, and employing preventative strategies are crucial for maintaining accurate inventory records and optimizing operational efficiency.Inventory discrepancies arise from a variety of sources, often intertwined and difficult to isolate.
This necessitates a systematic approach to both investigation and prevention.
Common Causes of Inventory Discrepancies
Several factors contribute to inventory discrepancies. These include human error in data entry or stock counting, theft or pilferage, damage or spoilage of goods, and issues with receiving or shipping processes. For example, a misplaced decimal point during data entry could significantly inflate or deflate the recorded quantity of a particular item. Similarly, damaged goods might be overlooked during stocktaking, leading to an inaccurate count.
Theft, while less easily quantifiable, represents a significant loss for many businesses.
Methods for Investigating and Resolving Inventory Discrepancies
Investigating discrepancies requires a methodical approach. Begin by comparing the physical count to the recorded inventory data, identifying specific items with significant differences. Next, trace the movement of the affected items through the inventory management system, reviewing purchase orders, sales records, and transfer documents. Interviews with warehouse staff can provide valuable insights into potential causes, such as damage, misplacement, or theft.
Reconciling these discrepancies may involve adjusting inventory records, initiating disciplinary actions if theft is suspected, or implementing improved inventory control measures. A thorough investigation helps to pinpoint the root cause and implement targeted solutions.
Strategies for Preventing Future Discrepancies
Preventing future discrepancies relies on a combination of technological and procedural improvements. Implementing a robust inventory management system with real-time tracking capabilities significantly reduces the risk of errors. Regular cycle counting, a process of counting a smaller portion of inventory regularly rather than a complete count less frequently, helps identify discrepancies early. Improved staff training on inventory procedures, including proper handling, storage, and data entry, minimizes human error.
Security measures, such as surveillance cameras and access controls, deter theft and unauthorized access to inventory. Implementing a system of checks and balances, where multiple individuals are involved in key inventory processes, helps to catch errors and prevent fraud. Regular audits of inventory processes and procedures further enhance accuracy and identify areas for improvement.
Using Data Analysis to Identify Trends and Patterns
Analyzing inventory data over time can reveal trends and patterns in discrepancies. By tracking the frequency, type, and magnitude of discrepancies, businesses can identify recurring issues. For example, consistently high discrepancies for a specific product line might indicate a problem with its storage or handling. Similarly, a sudden increase in discrepancies might signal theft or a breakdown in inventory control procedures.
Data analysis techniques, such as statistical process control and trend analysis, can help to identify these patterns and predict future discrepancies. This proactive approach allows for timely interventions and prevents further losses. For instance, if data reveals a consistent pattern of discrepancies related to a specific employee, it might warrant a review of their work practices or additional training.
Technology and Inventory Management
Integrating technology into inventory management significantly enhances efficiency and accuracy, reducing costs and improving overall business operations. Effective inventory management software, coupled with technologies like barcode scanning and RFID, provides real-time visibility into stock levels, minimizes discrepancies, and streamlines ordering processes. This leads to better decision-making and optimized resource allocation.Inventory management software automates many manual tasks associated with tracking inventory, significantly improving efficiency.
Features such as automated ordering, real-time stock updates, and reporting capabilities free up valuable employee time, allowing them to focus on other crucial aspects of the business. Furthermore, these systems reduce human error inherent in manual processes, resulting in more accurate inventory data and improved forecasting.
Inventory Management Software Features
Different inventory management software packages offer a range of features tailored to various business needs and sizes. Basic systems might focus on simple tracking and reporting, while more advanced solutions incorporate features such as forecasting, demand planning, and integration with other business systems like accounting and e-commerce platforms. Key features often include: stock tracking, purchase order management, sales order processing, reporting and analytics, and integration capabilities.
Some software also offers advanced features such as lot tracking, serial number tracking, and warehouse management capabilities.
Barcode Scanning and RFID Technology
Barcode scanning and Radio-Frequency Identification (RFID) technology offer powerful tools for streamlining inventory processes. Barcode scanners quickly and accurately capture product information, facilitating efficient stock checks, receiving, and shipping. RFID technology, on the other hand, provides a more automated and less labor-intensive solution. RFID tags attached to products can be read remotely, allowing for real-time tracking of inventory movement throughout the entire supply chain, even without line-of-sight.
This technology is particularly beneficial for high-volume environments or those dealing with a large number of SKUs. For example, a large retail chain could use RFID to track individual items as they move through the warehouse, onto shelves, and ultimately, to the point of sale. This level of granularity allows for very accurate inventory counts and helps identify theft or shrinkage quickly.
Comparison of Inventory Management Software
The choice of inventory management software depends heavily on the specific needs and budget of a business. The following table compares several popular options, though the market is constantly evolving, and features and pricing are subject to change.
Software | Cost (approx. monthly/user) | Key Features | Scalability |
---|---|---|---|
Zoho Inventory | $50 – $250+ | Stock management, order management, supplier management, reporting | Small to medium businesses |
Fishbowl Inventory | $499 – $1999+ | Manufacturing, inventory, and accounting software integration | Small to medium businesses |
NetSuite | Variable, enterprise-level pricing | Comprehensive ERP system including inventory management, financials, CRM | Large enterprises |
Katana MRP | $99 – $499+ | Manufacturing focused, includes planning, scheduling and inventory control | Small to medium manufacturers |
Visualizing Inventory Data
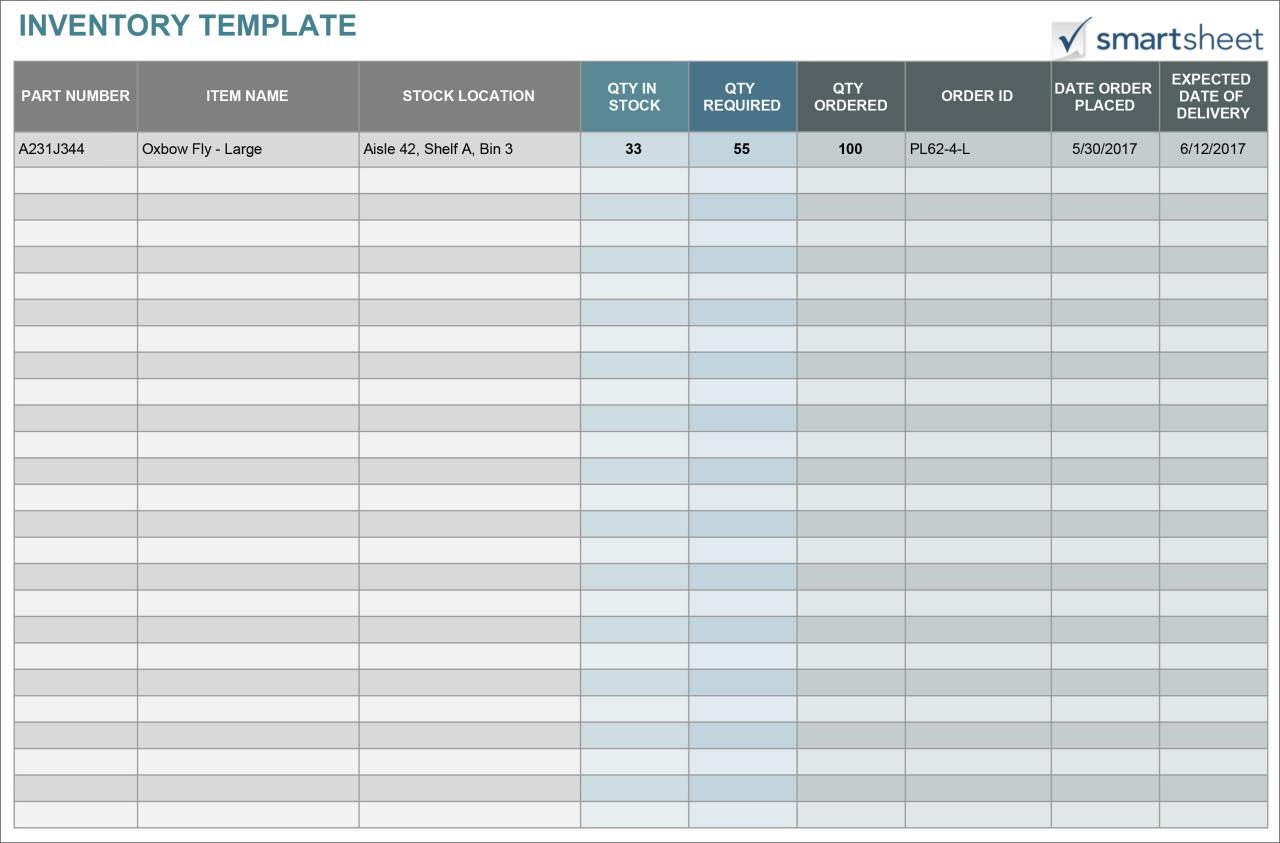
Effective inventory management relies heavily on the ability to understand and interpret data. Visualizing this data through reports and charts is crucial for identifying trends, spotting inefficiencies, and making informed decisions that optimize stock levels and minimize waste. A well-designed visualization system transforms raw inventory data into actionable insights.Visualizing key inventory metrics allows for a quick and comprehensive understanding of the current inventory situation.
This facilitates better decision-making and proactive adjustments to inventory strategies.
Sample Inventory Report
The following sample report illustrates how key inventory metrics can be presented visually. This example uses a combination of tables and charts to provide a comprehensive overview.
Product | Stock Level | Reorder Point | Turnover Rate (per year) | Value |
---|---|---|---|---|
Product A | 150 | 100 | 6 | $15,000 |
Product B | 25 | 50 | 2 | $5,000 |
Product C | 500 | 400 | 12 | $20,000 |
Product D | 10 | 20 | 1 | $1,000 |
A bar chart could visually represent stock levels against reorder points for each product, clearly highlighting items nearing or below their reorder points. A separate pie chart could display the percentage contribution of each product to the total inventory value. Finally, a line graph could track turnover rates over time for each product, showing trends and seasonality. This multi-faceted approach offers a complete picture.
Interpreting Inventory Data for Decision Making
By analyzing the data presented in the sample report (and similar reports generated regularly), businesses can identify several key areas for improvement. For example, Product B is consistently below its reorder point, suggesting potential stockouts and lost sales. Conversely, Product C has a high turnover rate, indicating strong demand and potentially justifying increased stock levels to meet this demand.
Product D, with a low turnover rate and low stock levels, might suggest a need for a review of its market viability or pricing strategy. The total inventory value provides an overview of the capital tied up in inventory, allowing for informed decisions regarding financing and investment.
Utilizing Charts and Graphs for Effective Data Representation
Different chart types are suited to different data visualization tasks. Bar charts effectively compare discrete values, such as stock levels across different products. Line graphs are ideal for showing trends over time, such as turnover rates over several months. Pie charts effectively show the proportion of different components within a whole, for instance, the percentage contribution of each product to the total inventory value.
Scatter plots can reveal correlations between different variables, such as stock levels and sales. The choice of chart depends on the specific data and the insights one wants to convey.
Optimizing Ordering and Minimizing Waste through Data Analysis
Analyzing inventory data, as presented in the sample report, enables businesses to optimize ordering and minimize waste in several ways. For example, by identifying slow-moving items (low turnover rates), businesses can adjust their ordering strategies to reduce excess stock. Predictive analytics, based on historical sales data and trend analysis, can help forecast future demand and optimize order quantities accordingly, reducing both stockouts and excess inventory.
Regularly reviewing turnover rates helps identify obsolete or near-obsolete items, allowing for timely disposal or clearance sales to minimize losses.
Security and Inventory Control
Maintaining a secure inventory is crucial for minimizing losses and ensuring the smooth operation of any business. Losses due to theft, damage, or obsolescence can significantly impact profitability and operational efficiency. Implementing robust security measures and control procedures is therefore essential for protecting your valuable assets. This section Artikels strategies and best practices for enhancing inventory security.Implementing effective security measures requires a multi-faceted approach encompassing physical security, access control, and procedural safeguards.
These measures work in concert to protect against various threats, from internal theft to external damage. Regular review and adaptation of these measures are also vital, as threats and vulnerabilities can evolve over time.
Physical Security Measures
Physical security plays a vital role in preventing inventory loss or damage. This involves implementing measures such as installing security cameras in strategic locations throughout the warehouse or storage area, providing clear and well-lit pathways to deter potential intruders, and securing access points with locks and alarms. Regular security patrols, both during and outside of operating hours, can also significantly deter theft and vandalism.
The use of robust shelving and racking systems prevents damage from collapses, while proper environmental controls (temperature and humidity) safeguard sensitive inventory.
Damaged or Obsolete Inventory Handling
Procedures for handling damaged or obsolete inventory should be clearly defined and consistently followed. This involves regular inventory checks to identify damaged or obsolete items. A formal process for documenting the condition of damaged goods, including photographs and descriptions, should be established. Depending on the nature of the damage and the type of goods, options such as repair, refurbishment, or disposal (following proper environmental regulations) should be considered.
Maintaining accurate records of damaged or obsolete inventory helps in tracking losses and informing future purchasing decisions. Regular audits of these processes ensure efficiency and compliance.
Inventory Security Across Multiple Locations
Managing inventory security across multiple locations presents unique challenges. Consistent security protocols must be implemented across all locations to maintain a uniform level of protection. This includes using standardized security systems, access control procedures, and inventory tracking software. Regular communication and collaboration between different locations are essential to share best practices, identify potential vulnerabilities, and respond effectively to security incidents.
Centralized monitoring of security systems across all locations can also provide a comprehensive overview of security status and facilitate quicker response to potential threats.
Security Protocols for Different Inventory Types, Business inventory checklist
Effective inventory security requires tailored approaches depending on the type of inventory. The following Artikels security protocols for different inventory categories:
- High-Value Items: These require enhanced security measures such as individual item tracking, secured storage areas with restricted access, and potentially specialized insurance.
- Perishable Goods: Maintaining proper temperature and humidity control is paramount, along with regular stock rotation to prevent spoilage. Stricter quality control measures are also necessary.
- Hazardous Materials: These require adherence to strict safety regulations, including specialized storage facilities, handling procedures, and potentially licensed personnel.
- Electronic Equipment: Protecting against theft and damage necessitates secure storage, possibly including anti-theft devices and environmental controls to prevent damage from temperature fluctuations or humidity.
Legal and Regulatory Compliance
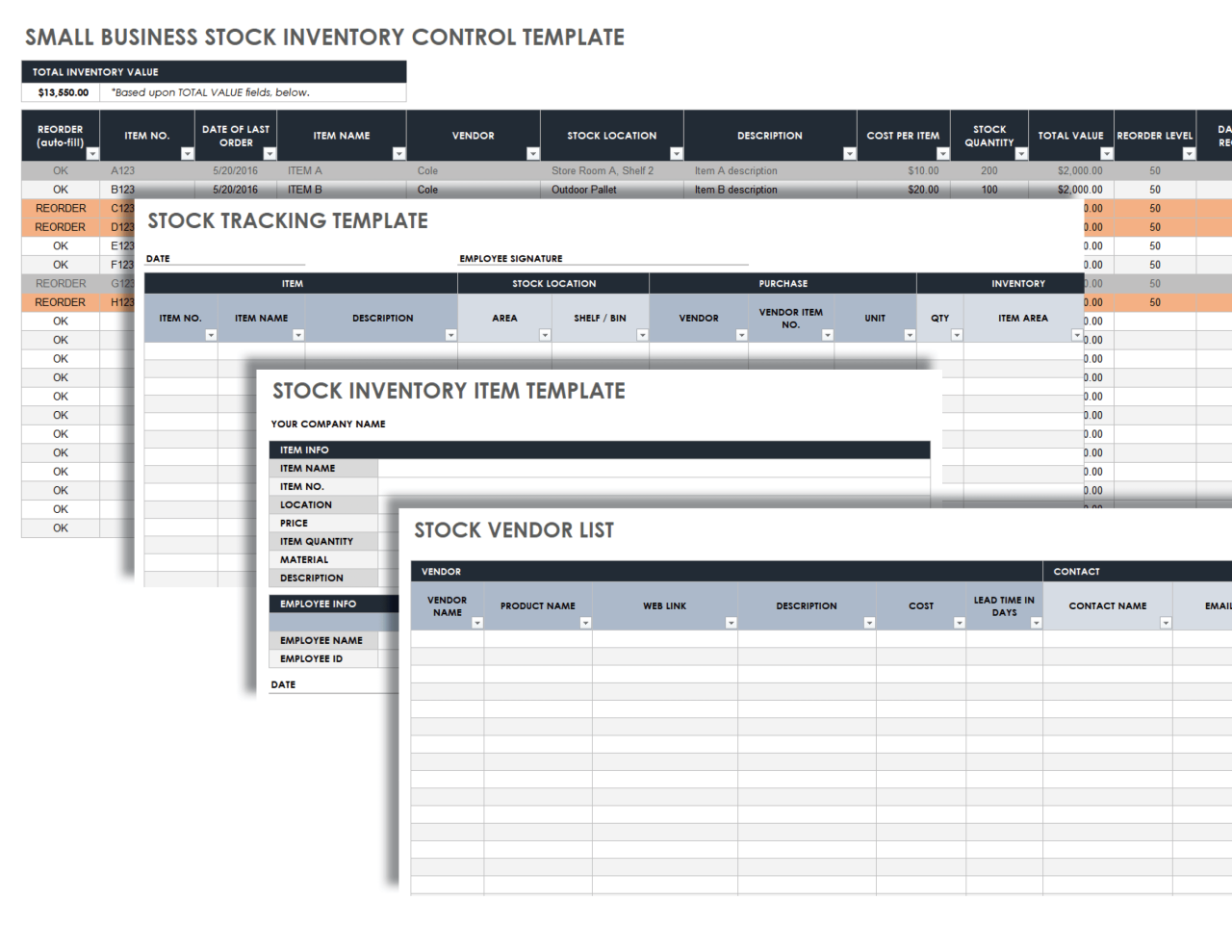
Maintaining accurate and compliant inventory records is crucial for any business, regardless of size or industry. Failure to comply with relevant regulations can lead to significant financial penalties, legal repercussions, and damage to reputation. This section Artikels key legal and regulatory considerations for effective inventory management.Accurate inventory records are the cornerstone of legal compliance. They provide the verifiable data needed to meet various regulatory requirements, including tax reporting, audits, and product safety standards.
Maintaining these records involves employing consistent inventory tracking methods, regular stocktaking, and the use of reliable inventory management systems.
Relevant Legal and Regulatory Requirements
Various laws and regulations govern inventory management, depending on the industry and location. These often address aspects such as product labeling, traceability, storage conditions, and disposal of obsolete or damaged goods. For example, the Food and Drug Administration (FDA) in the United States has stringent regulations concerning the handling and tracking of food and pharmaceutical products, demanding detailed record-keeping to ensure product safety and traceability throughout the supply chain.
Similarly, environmental regulations may dictate the proper disposal of hazardous materials within an inventory.
Maintaining Accurate Inventory Records for Compliance
Accurate inventory record-keeping is achieved through a combination of methods. This includes regular physical stock counts, cycle counting (regularly counting subsets of inventory), and the use of barcode or RFID technology for automated tracking. Data should be entered consistently and accurately into the inventory management system, and regular reconciliation between physical counts and system records should be performed to identify and correct any discrepancies.
This process requires clear procedures, staff training, and the use of appropriate software to minimize errors and ensure data integrity. Regular audits of inventory records should also be conducted to verify accuracy and compliance.
Consequences of Non-Compliance
Non-compliance with inventory management regulations can result in a range of severe consequences. These can include hefty fines, legal action from regulatory bodies, product recalls, reputational damage, and even business closure in extreme cases. For example, a company failing to accurately report inventory for tax purposes could face significant tax penalties and legal repercussions. In the food industry, failure to maintain proper inventory control and temperature records could lead to foodborne illnesses, resulting in product recalls, lawsuits, and substantial financial losses.
Industries with Specific Inventory Management Regulations
Several industries are subject to particularly strict inventory management regulations. The pharmaceutical industry, as mentioned, faces rigorous requirements for tracking medications from manufacturing to dispensing, ensuring quality, safety, and preventing counterfeiting. The food and beverage industry is similarly heavily regulated, with rules governing food safety, traceability, and proper storage conditions to prevent spoilage and contamination. The aerospace industry has strict regulations concerning the tracking and management of parts and materials used in aircraft manufacturing, to ensure safety and compliance with airworthiness standards.
The chemical industry also faces stringent regulations due to the hazardous nature of many of the materials handled, focusing on safety and environmental protection.
Closing Summary
Implementing a comprehensive business inventory checklist, as Artikeld in this guide, is a proactive step towards optimizing your operations and maximizing profitability. By mastering inventory management techniques, leveraging technology, and prioritizing accuracy and security, businesses can significantly reduce waste, improve efficiency, and gain a competitive edge. Remember that regular review and adaptation of your checklist are essential to ensure its continued effectiveness in meeting the evolving needs of your business.
FAQ Overview: Business Inventory Checklist
What is the difference between perpetual and periodic inventory systems?
Perpetual systems track inventory in real-time, while periodic systems involve counting inventory at fixed intervals.
How often should I conduct a physical inventory count?
Frequency depends on your business, but monthly or quarterly counts are common. High-value or perishable items may require more frequent checks.
What should I do if I discover a significant inventory discrepancy?
Investigate the cause (theft, damage, errors), adjust records, implement preventative measures, and potentially conduct a full inventory recount.
What are some common inventory management software options?
Popular options include Zoho Inventory, QuickBooks, and Fishbowl Inventory, each offering varying features and pricing.