Business inventory control is the backbone of efficient operations for any business, regardless of size or industry. Effective inventory management ensures optimal stock levels, minimizing storage costs while preventing stockouts that can disrupt sales and damage customer relationships. This guide explores the core principles, methods, and technologies crucial for mastering this critical business function, ultimately leading to improved profitability and sustainable growth.
From understanding different inventory valuation methods like FIFO and LIFO to leveraging software solutions and optimizing stock levels using techniques like Economic Order Quantity (EOQ), we will delve into the intricacies of inventory control. We’ll also examine the crucial role inventory plays within the broader supply chain, highlighting its impact on customer service and overall business efficiency. By the end, you’ll have a comprehensive understanding of how to implement and maintain a robust inventory control system tailored to your specific business needs.
Defining Business Inventory Control
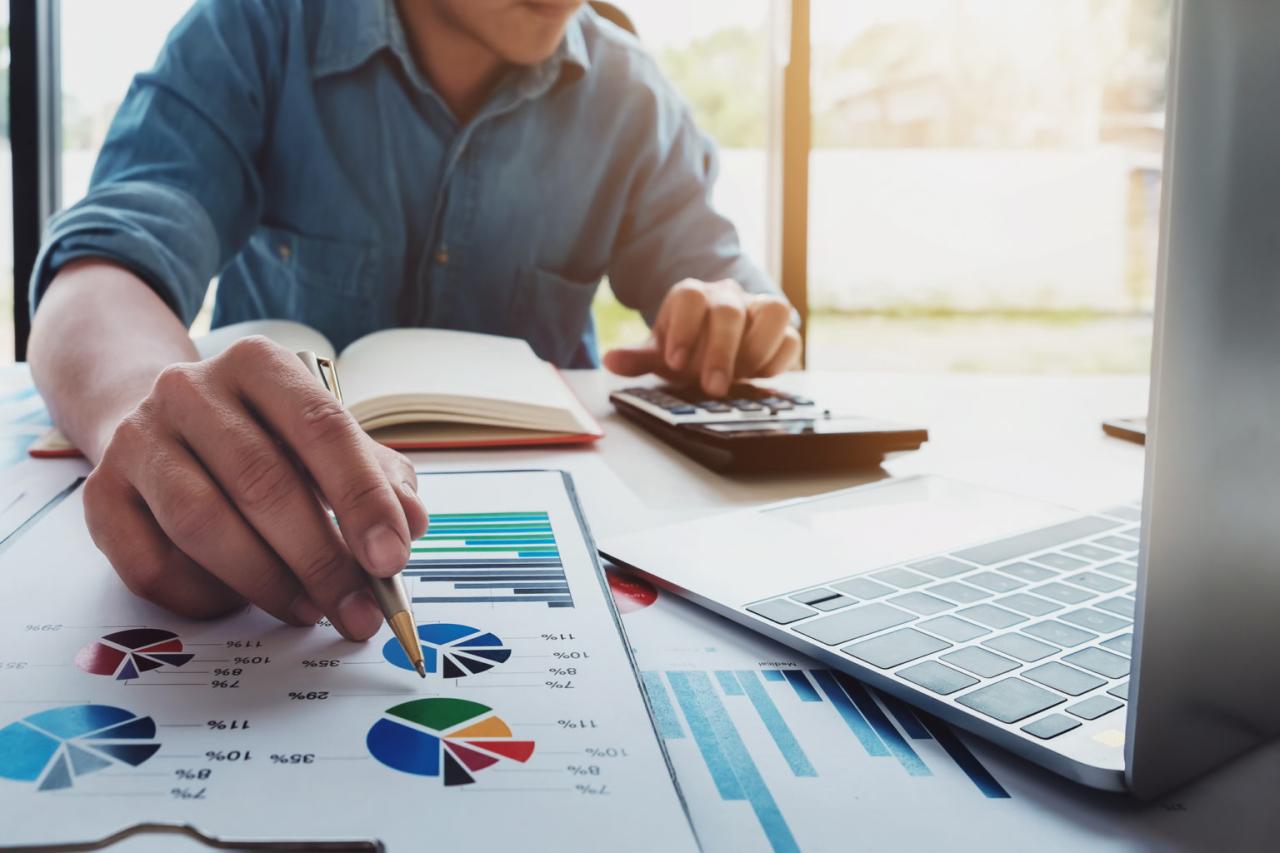
Effective inventory control is the backbone of a successful business, ensuring the right products are available at the right time and in the right quantities. It’s a crucial process that impacts profitability, customer satisfaction, and overall operational efficiency. Without a well-defined system, businesses risk stockouts, excess inventory, and ultimately, financial losses.Effective inventory management hinges on several core principles.
First, accurate demand forecasting is critical to predict future needs and avoid overstocking or shortages. Second, efficient storage and handling practices minimize waste and damage. Third, a robust tracking system provides real-time visibility into inventory levels, allowing for proactive adjustments. Finally, regular inventory audits verify the accuracy of records and identify discrepancies.
Types of Inventory and Their Characteristics
Different types of inventory exist, each with unique characteristics impacting management strategies. Raw materials are the basic inputs used in production. Work-in-progress (WIP) represents partially completed goods. Finished goods are ready for sale. Maintenance, repair, and operating supplies (MRO) are items used to support operations but not directly incorporated into products.
Obsolete inventory refers to items that are no longer in demand. Each type requires different storage conditions, tracking methods, and security measures. For example, raw materials might need specific temperature controls, while finished goods require secure storage to prevent theft.
Businesses Benefiting Most from Robust Inventory Control Systems
Businesses with high inventory turnover rates, those dealing with perishable goods, or those operating in just-in-time (JIT) manufacturing environments benefit immensely from strong inventory control. Retailers, particularly those with large product catalogs and numerous locations, need accurate tracking to avoid stockouts and optimize shelf space. Manufacturing companies, especially those with complex supply chains, depend on precise inventory control to maintain production schedules and minimize delays.
Pharmaceutical companies, handling temperature-sensitive and high-value products, require stringent inventory management to ensure product quality and safety.
Inventory Valuation Methods
Different methods exist for valuing inventory, each impacting the cost of goods sold and ultimately, profitability. The choice depends on factors such as industry, tax regulations, and accounting practices.
Method | Description | Advantages | Disadvantages |
---|---|---|---|
FIFO (First-In, First-Out) | Assumes the oldest inventory is sold first. | Simple to understand and implement; reflects current market prices. | Can lead to higher taxes during periods of inflation. |
LIFO (Last-In, First-Out) | Assumes the newest inventory is sold first. | Can result in lower taxes during periods of inflation; matches current costs with current revenues. | Can be more complex to implement; may not accurately reflect the physical flow of goods. |
Weighted Average | Calculates a weighted average cost for all inventory items. | Smooths out price fluctuations; relatively simple to calculate. | May not accurately reflect the cost of specific items; less responsive to price changes. |
Inventory Control Methods and Techniques
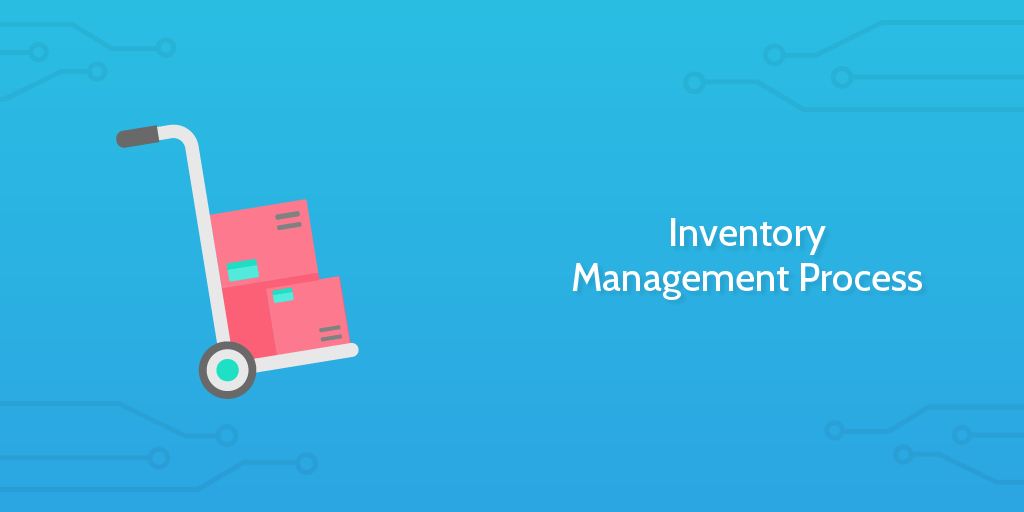
Effective inventory control is crucial for business success, impacting profitability, customer satisfaction, and operational efficiency. Understanding and implementing appropriate inventory control methods and techniques is paramount for optimizing inventory levels and minimizing costs. This section will explore several key methods and their applications.
Just-in-Time (JIT) Inventory Management
Just-in-Time (JIT) inventory management aims to minimize inventory holding costs by receiving materials only when needed for production. This system relies heavily on efficient production scheduling and strong relationships with suppliers.
Advantages of JIT include reduced storage costs, minimized waste from obsolescence or spoilage, and improved cash flow. However, disadvantages exist. JIT is highly susceptible to supply chain disruptions; delays from suppliers can halt production. It also requires a high degree of coordination and precise demand forecasting, demanding significant investment in information technology and strong supplier relationships. Furthermore, the lack of buffer stock leaves the business vulnerable to unexpected surges in demand.
Perpetual and Periodic Inventory Systems
Perpetual and periodic inventory systems represent two distinct approaches to tracking inventory levels. A perpetual system continuously monitors inventory levels, updating records with each transaction. A periodic system, in contrast, involves counting physical inventory at fixed intervals to determine stock levels.
Perpetual systems offer real-time inventory visibility, facilitating better demand forecasting and reducing stockouts. However, they require sophisticated inventory management software and can be costly to implement and maintain. Periodic systems are simpler and less expensive, requiring less technological investment. However, they provide only a snapshot of inventory at specific points in time, leading to potential inaccuracies and difficulties in identifying slow-moving or obsolete items.
The accuracy of periodic systems depends heavily on the thoroughness and frequency of physical counts.
The Role of Forecasting in Accurate Inventory Planning
Accurate forecasting is essential for effective inventory planning. By predicting future demand, businesses can optimize inventory levels, reducing holding costs while minimizing stockouts. Various forecasting techniques exist, ranging from simple moving averages to sophisticated statistical models.
For example, a company selling seasonal clothing might use historical sales data and weather patterns to forecast demand for winter coats. Inaccurate forecasting can lead to significant financial losses. Overstocking ties up capital and increases storage costs, while understocking results in lost sales and dissatisfied customers. The selection of an appropriate forecasting method depends on factors such as data availability, forecast horizon, and the level of accuracy required.
Spreadsheet-Based Inventory Tracking System
A simple inventory tracking system can be designed using a spreadsheet program like Microsoft Excel or Google Sheets. This system can track key information such as item ID, description, quantity on hand, reorder point, and cost per unit.
Consider a spreadsheet with columns for: Item ID (A), Description (B), Quantity on Hand (C), Reorder Point (D), Cost per Unit (E), Total Value (F). The formula for Total Value (column F) would be: =C2*E2
(assuming data for the first item starts in row 2). To calculate the reorder point, one might use a formula incorporating lead time and average daily demand.
For example, if the average daily demand is 10 units and the lead time is 5 days, the reorder point (column D) would be: =10*5
or 50 units. This simple system allows for tracking inventory levels and triggering reorders when necessary.
Inventory Management Software and Tools
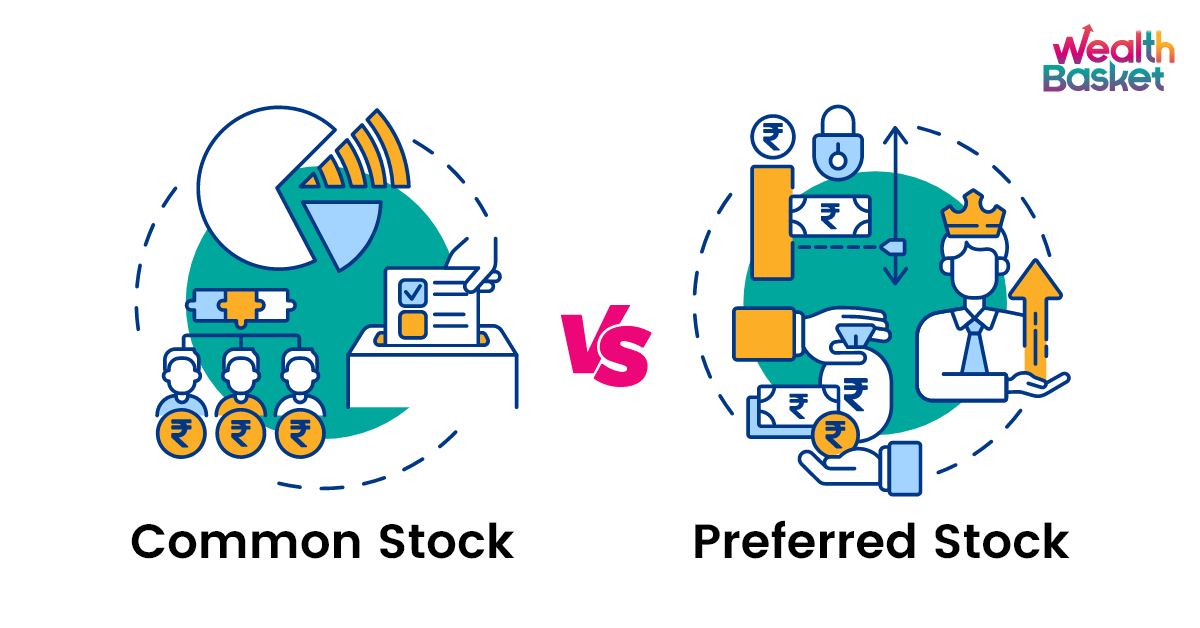
Effective inventory management relies heavily on utilizing appropriate software and tools. These systems automate many manual processes, improving accuracy, efficiency, and ultimately, profitability. Choosing the right system depends on the size and complexity of your business, as well as your specific needs and budget.
Popular Inventory Management Software Solutions
Several software solutions cater to various business needs. Three popular examples include Zoho Inventory, QuickBooks Online, and Fishbowl Inventory. Zoho Inventory offers a comprehensive suite of features suitable for small to medium-sized businesses, including order management, inventory tracking, and reporting. QuickBooks Online, while primarily an accounting software, integrates robust inventory management capabilities for businesses needing integrated financial and inventory data.
Fishbowl Inventory is a more specialized solution particularly well-suited for manufacturing and distribution businesses, offering advanced features like bill of materials management and work order tracking. Each system offers a unique set of strengths and weaknesses, making careful consideration of specific requirements crucial.
Cloud-Based versus On-Premise Inventory Systems
Cloud-based inventory systems store data on remote servers, accessible via the internet. This offers advantages such as accessibility from anywhere with an internet connection, automatic updates, and reduced IT infrastructure costs. On-premise systems, conversely, store data on servers located within the business’s own facilities. This provides greater control over data security and potentially higher performance, but requires significant investment in hardware, software, and IT support.
The choice depends on factors like budget, security concerns, and IT expertise. Cloud-based systems are generally more cost-effective and scalable for businesses lacking extensive IT infrastructure. On-premise systems may be preferred by businesses with extremely sensitive data or specific performance requirements.
Benefits of Integrating Inventory Management Software with Other Business Systems, Business inventory control
Integrating inventory management software with other business systems, such as Point of Sale (POS) systems and accounting software, significantly streamlines operations and improves data accuracy. For example, integrating with a POS system automatically updates inventory levels in real-time as sales occur, eliminating manual data entry and reducing the risk of discrepancies. Integration with accounting software automates the generation of financial reports, providing a clear picture of inventory costs and profitability.
This integrated approach eliminates data silos, leading to improved decision-making and overall business efficiency. A seamless flow of information across different systems is key to effective inventory management.
Essential Features to Consider When Selecting Inventory Management Software
Choosing the right inventory management software requires careful consideration of several key features. The following list Artikels essential aspects to evaluate:
- Real-time Inventory Tracking: Accurate and up-to-the-minute visibility of stock levels.
- Order Management: Efficient processing of orders from placement to fulfillment.
- Reporting and Analytics: Comprehensive reporting capabilities to track key metrics like inventory turnover, stock levels, and profitability.
- Scalability: Ability to adapt to changing business needs and growth.
- Integration Capabilities: Seamless integration with other business systems (POS, accounting, CRM).
- User-Friendliness: Intuitive interface and ease of use for all employees.
- Security: Robust security measures to protect sensitive inventory data.
- Customer Support: Reliable and responsive customer support to address any issues.
- Cost: Consider both the initial cost and ongoing subscription fees.
Optimizing Inventory Levels
Effective inventory management hinges on optimizing stock levels. Maintaining optimal inventory balances requires a delicate dance between minimizing holding costs and ensuring sufficient stock to meet customer demand and avoid stockouts. This involves understanding key concepts like Economic Order Quantity and the role of safety stock, as well as implementing strategies to reduce storage and associated expenses.
Economic Order Quantity (EOQ)
Economic Order Quantity (EOQ) is a crucial inventory management model that determines the ideal order size to minimize the total inventory costs. These costs encompass ordering costs (like processing fees and transportation) and holding costs (like storage, insurance, and obsolescence). The EOQ formula balances these opposing costs, aiming to find the sweet spot where neither is excessively high. A smaller order quantity reduces holding costs but increases ordering frequency and associated costs.
Conversely, a larger order quantity minimizes ordering costs but increases holding costs due to larger storage needs and potential for stock obsolescence. The EOQ formula is:
EOQ = √[(2DS)/H]
where:* D = Annual demand
- S = Ordering cost per order
- H = Holding cost per unit per year
For example, consider a company with an annual demand (D) of 10,000 units, an ordering cost (S) of $100 per order, and a holding cost (H) of $5 per unit per year. Applying the EOQ formula:
EOQ = √[(2
- 10,000
- $100) / $5] = 2000 units
This suggests the company should order 2000 units at a time to minimize total inventory costs. It’s important to remember that the EOQ model relies on several assumptions, such as constant demand and lead times, which may not always hold true in real-world scenarios. However, it provides a valuable starting point for optimizing order quantities.
Safety Stock and its Impact
Safety stock acts as a buffer against unexpected fluctuations in demand or lead times. While it increases inventory holding costs, it significantly reduces the risk of stockouts, protecting service levels and customer satisfaction. The level of safety stock depends on factors like demand variability, lead time variability, and the desired service level. Higher safety stock levels equate to higher holding costs but also a lower probability of stockouts.
Conversely, lower safety stock levels minimize holding costs but increase the risk of stockouts and potentially lost sales or dissatisfied customers. A company might choose to maintain higher safety stock for high-demand, critical items to avoid disruptions, while maintaining lower safety stock for less critical, slower-moving items.
Minimizing Inventory Holding Costs
Reducing inventory holding costs is a key objective in inventory optimization. Several strategies can be employed to achieve this. These include:
- Negotiating better storage rates with warehouses.
- Improving warehouse efficiency to minimize space usage.
- Implementing a just-in-time (JIT) inventory system to reduce the amount of stock held.
- Improving demand forecasting accuracy to reduce the need for excessive safety stock.
- Regularly reviewing and disposing of obsolete or slow-moving items.
Implementing these strategies can significantly reduce overall inventory holding costs, freeing up capital and improving profitability.
Calculating Reorder Points
The reorder point (ROP) signifies the inventory level at which a new order should be placed to avoid stockouts. The calculation considers lead time demand (the expected demand during the lead time) and safety stock. The formula is:
ROP = (Lead Time Demand) + Safety Stock
Lead time demand is calculated by multiplying the average daily demand by the lead time in days. For instance, if average daily demand is 10 units and the lead time is 5 days, the lead time demand is 50 units. Safety stock is determined based on the desired service level and demand variability. A higher service level necessitates a larger safety stock.
The ROP for each item will vary based on its individual demand characteristics and lead time. Regularly reviewing and adjusting reorder points based on actual demand patterns and lead time performance is crucial for maintaining optimal inventory levels. Accurate forecasting and efficient inventory management systems are essential for precise reorder point calculations.
Inventory Control and Supply Chain Management: Business Inventory Control

Effective inventory control is not merely an internal process; it’s a cornerstone of a smoothly functioning and efficient supply chain. The relationship between precise inventory management and overall supply chain performance is deeply intertwined, impacting everything from production scheduling to customer satisfaction. A well-managed inventory system directly translates to reduced costs, improved responsiveness, and enhanced profitability across the entire supply chain.Inventory control significantly impacts supply chain efficiency by minimizing storage costs, reducing waste from obsolescence or spoilage, and optimizing the flow of goods.
Efficient inventory management ensures that the right amount of materials is available at the right time and place, preventing production delays and meeting customer demands promptly. Conversely, poor inventory control can lead to stockouts, excess inventory, and increased logistical challenges, ultimately hindering the overall efficiency of the supply chain.
Challenges of Managing Inventory Across Multiple Locations
Managing inventory across geographically dispersed locations presents a unique set of complexities. These challenges include increased transportation costs, the need for sophisticated tracking systems, the risk of discrepancies in inventory data between locations, and the potential for higher levels of obsolescence due to differing demand patterns in various markets. Effective communication and coordination between different warehouse locations are critical to overcome these challenges.
Centralized inventory management systems, employing real-time data updates and robust reporting capabilities, are crucial for maintaining accuracy and visibility across all locations. For example, a retail chain with stores nationwide must manage inventory levels for each store, considering local demand fluctuations and seasonal trends. This requires a system that can track inventory in real-time, predict demand, and optimize shipments to minimize holding costs and prevent stockouts.
Effective Inventory Control and Improved Customer Service
Effective inventory control directly contributes to enhanced customer service. Accurate inventory data allows businesses to fulfill orders promptly, reducing lead times and improving order fulfillment rates. By avoiding stockouts, companies can maintain customer loyalty and build a strong reputation for reliability. For instance, an online retailer that uses real-time inventory tracking can provide accurate delivery estimates to customers, managing expectations and reducing order cancellations.
Furthermore, effective inventory management allows businesses to offer a wider selection of products while maintaining optimal stock levels, catering to diverse customer needs and preferences. Proactive inventory management also allows businesses to anticipate demand surges and prepare accordingly, ensuring they can meet increased customer orders during peak seasons or promotional events, thus preventing lost sales opportunities.
Inventory Control Process Flowchart within a Supply Chain
The following describes a flowchart illustrating the inventory control process within a supply chain. The process begins with forecasting demand, which informs procurement and production planning. Then, goods are received and inspected, followed by storage and warehousing. Inventory levels are continuously monitored and updated using a chosen inventory management system. This data informs replenishment decisions, triggering orders for new stock when necessary.
Finally, goods are shipped to customers, and the entire cycle repeats. The system incorporates feedback loops to continuously refine demand forecasting and optimize inventory levels based on actual sales data and market trends. This iterative process ensures the system adapts to changing market conditions and customer demand.
Inventory Accuracy and Auditing
Maintaining accurate inventory records is crucial for efficient business operations. Inaccurate data leads to lost sales, increased costs, and poor decision-making. Regular audits and robust tracking systems are essential to ensure inventory counts reflect reality.Accurate inventory data is the bedrock of effective inventory management. Without it, businesses operate blindly, risking stockouts, overstocking, and ultimately, financial losses. Regular auditing processes, combined with appropriate technology, help mitigate these risks and improve overall operational efficiency.
Importance of Regular Inventory Audits and Cycle Counting
Regular inventory audits and cycle counting are vital for identifying and correcting discrepancies between recorded inventory levels and physical stock. Audits provide a comprehensive overview of inventory accuracy at a specific point in time, while cycle counting involves regularly counting a smaller subset of inventory items. This allows for more frequent monitoring and earlier detection of errors. The frequency of both audits and cycle counting should be determined based on factors such as inventory turnover rate, item value, and risk of loss or damage.
For example, a business with high-value, low-volume items might opt for more frequent cycle counting and less frequent full audits. Conversely, a business with high-volume, low-value items may prioritize annual audits supplemented by periodic cycle counting of high-demand items.
Methods for Identifying and Resolving Inventory Discrepancies
Identifying discrepancies involves comparing physical counts to recorded inventory levels. Differences may arise from various sources, including data entry errors, theft, damage, obsolescence, or inaccurate receiving processes. Investigating discrepancies requires a systematic approach. For instance, if a significant shortage is identified for a particular item, the receiving process should be reviewed to determine if items were received but not properly recorded.
Similarly, if there is an excess of stock, a thorough check of sales and returns data is necessary. Resolution may involve adjusting inventory records, investigating potential causes, implementing corrective actions, and potentially writing off obsolete or damaged goods. Documentation of the entire process is crucial for future reference and improvement.
The Role of Barcode Scanning and RFID Technology in Improving Inventory Accuracy
Barcode scanning and Radio-Frequency Identification (RFID) technology significantly enhance inventory accuracy. Barcode scanning automates data entry, reducing manual errors. RFID technology goes further by automatically tracking items throughout the supply chain, providing real-time visibility into inventory levels and location. This reduces the time and effort required for physical inventory counts and enables more frequent updates to inventory records.
For example, a warehouse using RFID can track the movement of pallets in real-time, providing an immediate and accurate inventory count. This eliminates the need for manual counting and significantly reduces the risk of human error.
Best Practices for Maintaining Accurate Inventory Records
Maintaining accurate inventory records requires a combination of robust processes and technology. This includes implementing a well-defined receiving process, ensuring accurate data entry, using a reliable inventory management system, and regularly conducting audits and cycle counting. Staff training on proper inventory procedures is also essential. Clear guidelines on handling damaged or obsolete items, along with regular reviews of inventory levels and sales data, are also vital.
Furthermore, implementing a system of checks and balances, such as requiring two people to verify inventory counts or using a secure inventory management system, helps prevent errors and potential fraud. Regular reconciliation of inventory records with financial records helps identify any significant discrepancies and potential issues.
The Impact of Inventory Control on Profitability
Effective inventory control is not merely a logistical exercise; it’s a cornerstone of profitability. By optimizing inventory levels and minimizing waste, businesses can significantly improve their bottom line. This section explores the direct relationship between efficient inventory management and increased financial success.Efficient inventory management directly contributes to increased profitability through several key mechanisms. Firstly, it minimizes the costs associated with holding excess inventory.
Storage fees, insurance, and the risk of obsolescence or damage all represent significant expenses that can eat into profit margins. Secondly, well-managed inventory ensures that businesses have the right products available at the right time to meet customer demand. This prevents lost sales opportunities due to stockouts, a critical factor in maintaining revenue streams. Finally, streamlined inventory processes reduce labor costs associated with managing inventory manually, freeing up resources for more profitable activities.
Inventory Shrinkage’s Impact on Profitability
Inventory shrinkage, the difference between the recorded inventory and the actual physical inventory, significantly impacts a company’s profitability. This discrepancy can result from theft, damage, spoilage, errors in record-keeping, or inaccurate counting. The financial consequences can be substantial, as unsold or lost inventory represents a direct loss of revenue and an increase in the cost of goods sold. For instance, a retail store experiencing a 1% shrinkage rate on a $1 million inventory value would see a $10,000 loss, directly impacting its net profit.
Effective inventory control measures, such as robust security systems, regular stock counts, and improved tracking systems, are essential in mitigating shrinkage and protecting profitability.
Reducing Waste and Spoilage Through Inventory Control
Effective inventory control plays a crucial role in minimizing waste and spoilage, particularly in industries dealing with perishable goods or products with limited shelf lives. Implementing a first-in, first-out (FIFO) inventory management system ensures that older products are sold before they expire or become obsolete, reducing waste and maintaining product quality. Regular inventory audits and monitoring of expiration dates help identify and address potential spoilage issues proactively.
For example, a grocery store using FIFO can significantly reduce food waste, saving money on spoiled products and improving its environmental impact, thereby positively affecting its bottom line. Investing in proper storage facilities and maintaining optimal temperature and humidity control also minimizes spoilage and extends product shelf life.
Key Performance Indicators (KPIs) for Inventory Control Effectiveness
Measuring the effectiveness of inventory control requires tracking several key performance indicators. These metrics provide insights into the efficiency and profitability of inventory management strategies.
The following KPIs are crucial for assessing the performance of inventory control systems:
- Inventory Turnover Ratio: This indicates how efficiently a company is selling its inventory. A higher ratio generally suggests better inventory management.
- Gross Profit Margin: This reflects the profitability of sales after deducting the cost of goods sold. Efficient inventory control directly impacts the cost of goods sold and therefore the gross profit margin.
- Inventory Holding Costs: This measures the total cost of storing and maintaining inventory, including storage fees, insurance, and obsolescence costs. Lower holding costs indicate better inventory management.
- Shrinkage Rate: This measures the percentage of inventory lost due to theft, damage, or other causes. A lower shrinkage rate indicates improved inventory security and control.
- Order Fill Rate: This indicates the percentage of orders fulfilled on time and in full. Higher order fill rates demonstrate efficient inventory management that meets customer demand.
- Days Sales of Inventory (DSI): This metric indicates the number of days it takes to sell the average inventory. A lower DSI suggests efficient inventory turnover.
Summary
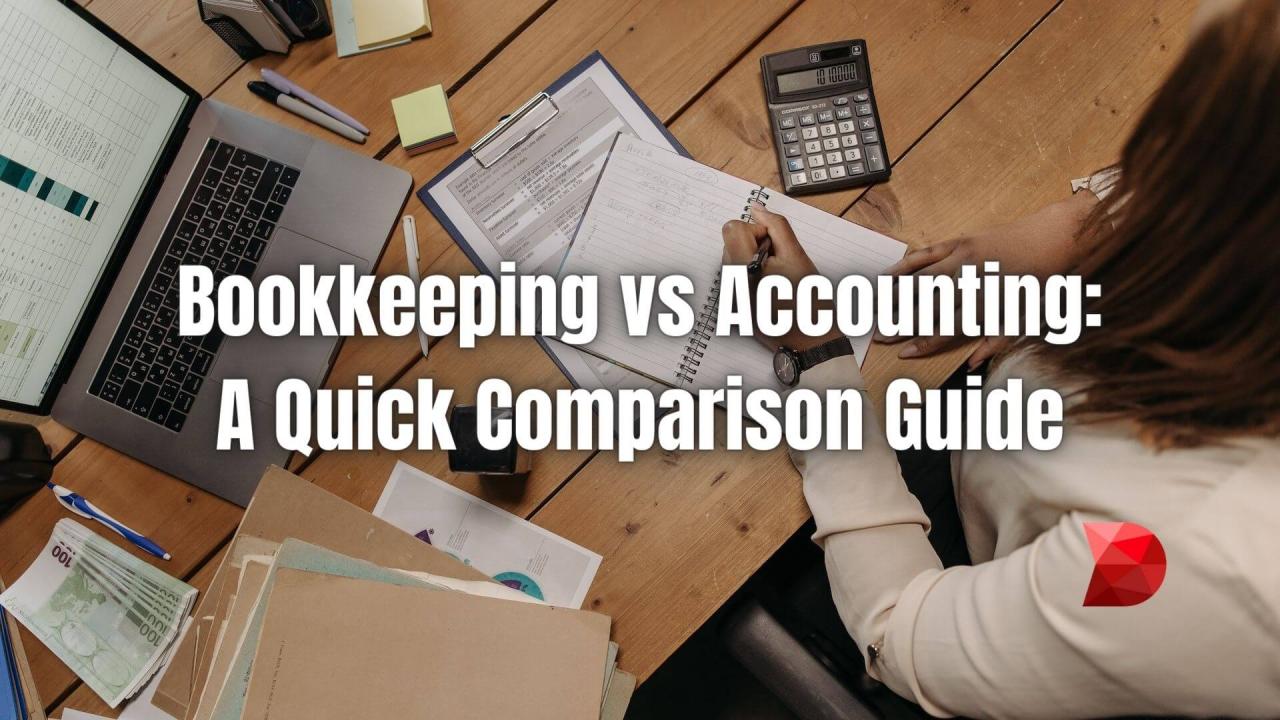
Mastering business inventory control is not merely about tracking items; it’s about strategic resource management that directly impacts profitability and customer satisfaction. By implementing the strategies and technologies discussed, businesses can streamline operations, reduce waste, and enhance their overall competitiveness. Regular audits, proactive forecasting, and the adoption of suitable software are key components of a successful inventory control system.
Continuous improvement and adaptation to changing market demands are crucial for long-term success in this critical area of business management.
Questions and Answers
What is the difference between FIFO and LIFO?
FIFO (First-In, First-Out) assumes the oldest inventory is sold first. LIFO (Last-In, First-Out) assumes the newest inventory is sold first. These methods affect cost of goods sold and ending inventory values on financial statements.
How often should I conduct inventory audits?
The frequency of inventory audits depends on factors like inventory turnover rate and risk tolerance. Regular cycle counting, perhaps weekly or monthly, supplemented by full physical audits annually or semi-annually, is a common approach.
What are some common causes of inventory shrinkage?
Common causes include theft, damage, spoilage, errors in record-keeping, and inaccurate inventory counts. Implementing strong security measures and using technology like barcode scanning can help mitigate shrinkage.
How can I choose the right inventory management software?
Consider factors like business size, budget, required features (e.g., forecasting, reporting), integration capabilities with other systems, and ease of use. Start with a trial period to assess the software’s suitability.