Business inventory control definition – Business inventory control definition: Efficient inventory management is crucial for business success. Understanding the core principles, from defining what inventory control actually
-is* to implementing effective strategies, is paramount for profitability and operational efficiency. This guide explores the multifaceted world of inventory control, encompassing its definition, key components, various methods, and the role of technology in optimizing this critical business function.
We’ll delve into both manual and automated approaches, highlighting the advantages and disadvantages of each, and ultimately demonstrate how mastering inventory control can significantly impact a company’s bottom line.
We will cover essential concepts like FIFO, LIFO, and weighted average cost methods, illustrating their practical applications and helping you choose the most suitable approach for your specific business needs. Further, we will examine the importance of accurate data, explore the challenges businesses often encounter, and offer solutions to common problems like stockouts and overstocking. The goal is to provide a clear, concise, and actionable understanding of business inventory control, empowering you to make informed decisions and optimize your inventory management practices.
Defining Business Inventory Control
Inventory control is a crucial aspect of successful business operations. It involves the systematic management of goods, from the moment they are acquired until they are sold or used. Effective inventory control minimizes waste, maximizes efficiency, and ultimately contributes to improved profitability. This involves a careful balancing act between ensuring sufficient stock to meet demand and avoiding overstocking which ties up capital and increases storage costs.Business inventory control is the process of overseeing and managing the flow of goods within a business, from acquisition to sale or use.
This encompasses all stages, including planning, procurement, storage, tracking, and distribution. The goal is to optimize inventory levels to meet customer demand while minimizing costs and waste.
A Concise Definition of Business Inventory Control
Business inventory control is the strategic management of a company’s goods, encompassing planning, acquisition, storage, tracking, and distribution, to optimize stock levels, meet customer demand, and minimize costs.
Real-World Examples of Effective Inventory Control
Effective inventory control systems are used across various industries. For example, a large retail chain like Walmart utilizes sophisticated software and data analytics to predict demand, optimize stock levels across its vast network of stores, and minimize stockouts. This allows them to maintain a wide selection of products while minimizing storage costs and preventing obsolete inventory. Similarly, a manufacturer of automotive parts employs a just-in-time (JIT) inventory system to receive components only as needed for assembly.
This drastically reduces storage space requirements and minimizes the risk of parts becoming obsolete. Finally, a small bakery uses a simple inventory tracking system to monitor the use of ingredients and prevent spoilage. By closely monitoring flour, sugar, and other perishables, they minimize waste and ensure they have enough ingredients to meet daily demand.
Key Objectives of a Robust Inventory Control System
A robust inventory control system aims to achieve several key objectives. These include minimizing storage costs by avoiding overstocking, reducing the risk of stockouts by maintaining sufficient inventory to meet demand, improving order fulfillment speed and accuracy, reducing waste due to spoilage or obsolescence, and increasing overall profitability by optimizing inventory levels and reducing costs. Accurate tracking and forecasting are critical to achieving these objectives.
Furthermore, a well-designed system enhances operational efficiency, allowing businesses to allocate resources more effectively and respond swiftly to changes in market demand.
Components of an Inventory Control System
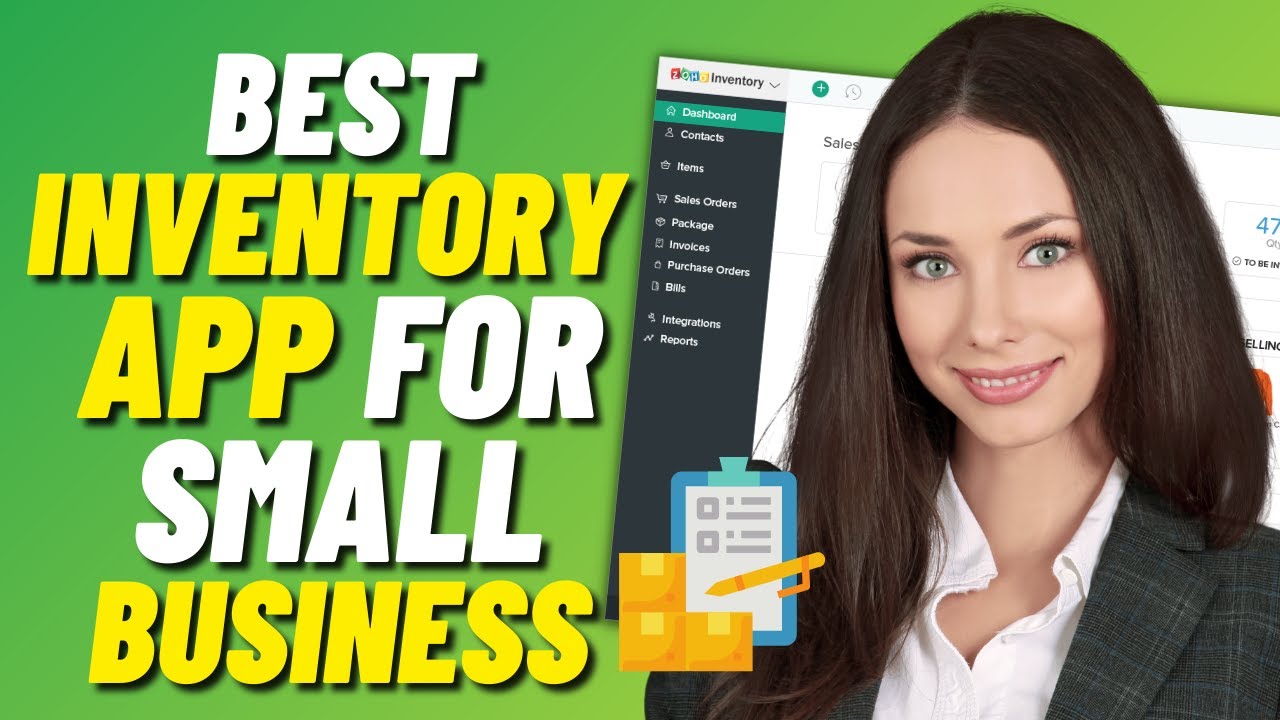
Effective inventory control is not simply about tracking items; it’s about optimizing the entire process, from procurement to sales. A robust system requires several key components working in harmony to ensure efficiency and accuracy. These components contribute to minimizing waste, maximizing profitability, and meeting customer demands consistently.
Essential Components of an Inventory Control System
A typical inventory control system comprises several interconnected elements. These elements work together to provide a holistic view of inventory levels, allowing for informed decision-making regarding purchasing, production, and sales. These elements are not mutually exclusive and often overlap in their functionality.
- Inventory Tracking: This fundamental component involves meticulously recording the movement of goods – from receiving to storage to sales. This requires accurate data entry and regular updates.
- Demand Forecasting: Predicting future demand allows businesses to proactively manage inventory levels, avoiding both stockouts and overstocking. Sophisticated forecasting methods utilize historical data and market trends.
- Ordering and Procurement: This involves establishing efficient processes for ordering new inventory, negotiating with suppliers, and managing lead times. Streamlining this process minimizes delays and reduces costs.
- Storage and Warehousing: Proper storage is crucial to maintain product quality and prevent damage or loss. This includes effective space utilization and organized storage systems.
- Inventory Valuation: Accurately valuing inventory is essential for financial reporting. Various methods exist, such as FIFO (First-In, First-Out) and LIFO (Last-In, First-Out), each with its own implications.
- Reporting and Analysis: Regular reporting and analysis of inventory data provide valuable insights into performance, helping identify areas for improvement and informing strategic decisions.
The Role of Technology in Modern Inventory Control
Technology has revolutionized inventory control, enabling greater accuracy, efficiency, and scalability. Modern systems leverage sophisticated software and hardware to automate many aspects of the process, reducing manual effort and human error.
- Inventory Management Software (IMS): IMS provides a centralized platform for tracking inventory, managing orders, and generating reports. Features often include barcode scanning, real-time tracking, and integration with other business systems.
- Radio-Frequency Identification (RFID): RFID tags attached to products allow for automated tracking of inventory movement, providing real-time visibility across the supply chain. This technology is particularly beneficial in large warehouses or for high-volume items.
- Warehouse Management Systems (WMS): WMS software optimizes warehouse operations, improving efficiency in receiving, putaway, picking, and shipping. This often includes features such as automated guided vehicles (AGVs) and robotic picking systems.
- Data Analytics and Machine Learning: Advanced analytics tools can process large datasets to identify trends, predict demand, and optimize inventory levels. Machine learning algorithms can further enhance forecasting accuracy and automate decision-making.
Manual vs. Automated Inventory Control Methods
The choice between manual and automated inventory control depends on factors such as business size, budget, and inventory complexity. While manual systems are simpler and less expensive upfront, automated systems offer significant advantages in terms of accuracy, efficiency, and scalability.
Factor | Manual Inventory Control | Automated Inventory Control |
---|---|---|
Cost | Low initial investment, high labor costs | High initial investment, lower labor costs in the long run |
Accuracy | Prone to human error | Highly accurate, minimizing errors |
Efficiency | Time-consuming and labor-intensive | Highly efficient, automating many tasks |
Scalability | Difficult to scale with business growth | Easily scalable to accommodate increasing inventory |
Simplified Inventory Control System Flowchart
A simplified inventory control system can be visualized using a flowchart. This illustrates the basic steps involved, from receiving inventory to fulfilling customer orders. The flowchart would start with a “Receive Inventory” box, followed by “Update Inventory Records,” then “Store Inventory,” followed by a decision point: “Is there a customer order?”. If yes, it proceeds to “Pick and Pack Order,” then “Update Inventory Records” (again), and finally “Ship Order.” If no, the process loops back to “Receive Inventory,” showing the continuous nature of inventory management.
Inventory Control Methods and Techniques
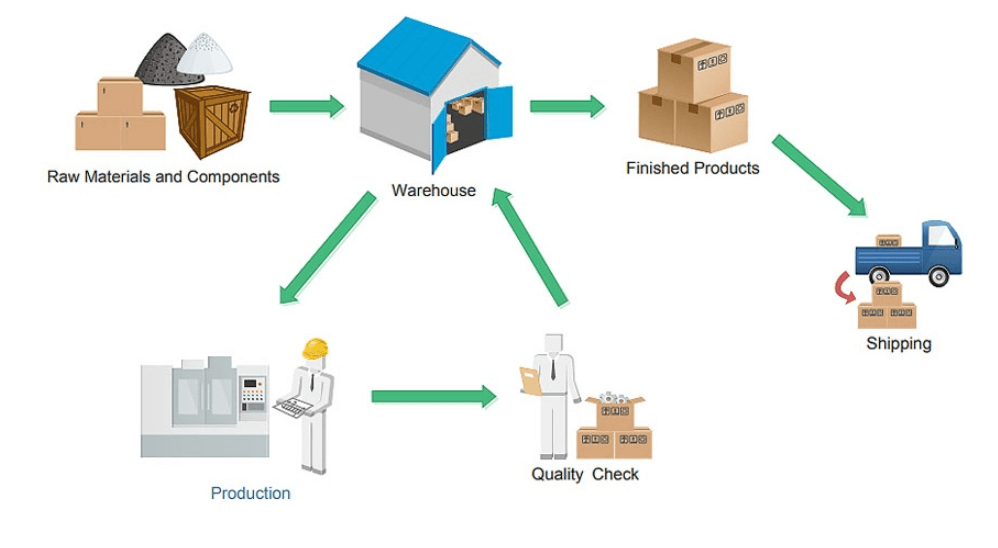
Effective inventory management relies on accurate tracking and valuation methods. Choosing the right method significantly impacts financial reporting, tax liabilities, and overall profitability. Several established techniques exist, each with strengths and weaknesses depending on the nature of the business and the goods being managed.
Different methods exist for tracking inventory and assigning costs to goods sold. These methods directly influence the reported cost of goods sold (COGS) and the value of ending inventory on the balance sheet. Understanding these methods is crucial for accurate financial reporting and effective decision-making.
Inventory Costing Methods: FIFO, LIFO, and Weighted Average
Three common inventory costing methods are First-In, First-Out (FIFO), Last-In, First-Out (LIFO), and Weighted-Average Cost. These methods differ in how they assign costs to goods sold and remaining inventory.
- FIFO (First-In, First-Out): This method assumes that the oldest inventory items are sold first. The cost of goods sold reflects the cost of the oldest items, while the ending inventory value reflects the cost of the newest items. This method is generally preferred when dealing with perishable goods or items that quickly become obsolete.
- LIFO (Last-In, First-Out): This method assumes that the newest inventory items are sold first. The cost of goods sold reflects the cost of the newest items, while the ending inventory value reflects the cost of the oldest items. LIFO is less commonly used due to tax implications and its potential to misrepresent inventory value in inflationary periods. Note: LIFO is not permitted under IFRS (International Financial Reporting Standards).
- Weighted-Average Cost: This method calculates the average cost of all inventory items available for sale during a period. This average cost is then used to determine the cost of goods sold and the value of ending inventory. It provides a smoother representation of inventory costs compared to FIFO and LIFO, particularly useful when inventory items are homogenous.
Comparison of Inventory Costing Methods
The suitability of each inventory costing method depends on various factors. The following table summarizes the key differences and their implications for different business types.
Method | Suitable for | Advantages | Disadvantages |
---|---|---|---|
FIFO | Businesses with perishable goods, fast-moving items | Reflects current market prices, simple to understand and implement | Higher tax liability during inflation |
LIFO | Businesses with slow-moving items, stable prices (Note: not permitted under IFRS) | Lower tax liability during inflation | Can lead to understated inventory value, complex to implement |
Weighted Average | Businesses with homogenous inventory, stable prices | Simple to calculate, smooths out price fluctuations | May not accurately reflect the cost of specific items |
Inventory Turnover and its Importance
Inventory turnover is a crucial ratio that measures how efficiently a business manages its inventory. It indicates how many times a company sells and replaces its inventory during a specific period. A high inventory turnover generally suggests strong sales and efficient inventory management, while a low turnover may indicate overstocking, slow-moving inventory, or weak demand.
Calculating Inventory Turnover
Inventory turnover is calculated using the following formula:
Inventory Turnover = Cost of Goods Sold / Average Inventory
Example: A company had a cost of goods sold of $100,000 during the year. Its beginning inventory was $20,000, and its ending inventory was $30,000. The average inventory is ($20,000 + $30,000) / 2 = $25,000. Therefore, the inventory turnover is $100,000 / $25,000 = 4. This means the company sold and replaced its inventory four times during the year.
Inventory Management Software and Tools: Business Inventory Control Definition
Efficient inventory control relies heavily on effective software and tools. These systems automate many manual processes, leading to significant improvements in accuracy, speed, and overall efficiency. Choosing the right software is crucial for businesses of all sizes, from small startups to large enterprises.Inventory management software streamlines various aspects of inventory control, from tracking stock levels and predicting demand to managing orders and automating reporting.
This automation reduces the risk of human error, minimizes stockouts and overstocking, and ultimately contributes to improved profitability. Different software solutions cater to various business needs and budgets, offering a range of features and functionalities.
Features of Common Inventory Management Software
Common features found in most inventory management software packages include real-time tracking of inventory levels across multiple locations, automated reorder point calculations, barcode and RFID scanning integration, detailed reporting and analytics capabilities, and robust search and filtering options for quick access to inventory data. Many also offer advanced features such as demand forecasting, lot and serial number tracking, and integration with e-commerce platforms.
Sophisticated systems may include features like warehouse management capabilities and integration with supply chain partners.
Integration with Other Business Systems
Effective inventory management software seamlessly integrates with other crucial business systems. For example, integration with accounting software automates the recording of inventory transactions, reducing manual data entry and minimizing errors. Integration with point-of-sale (POS) systems provides real-time updates on inventory levels as sales occur, ensuring accurate stock counts. This real-time data flow eliminates discrepancies between physical inventory and recorded inventory, a common problem in businesses lacking integrated systems.
Furthermore, integration with enterprise resource planning (ERP) systems offers a holistic view of the entire business, improving decision-making across various departments. A company using a POS system like Square could integrate it with inventory software like Zoho Inventory, providing immediate updates on sales and stock levels.
Best Practices for Selecting and Implementing Inventory Management Software
Selecting and implementing inventory management software requires careful planning. Businesses should first assess their specific needs and requirements, considering factors such as business size, inventory complexity, and budget constraints. A thorough evaluation of different software options, including demos and trials, is essential. Furthermore, it’s crucial to ensure the chosen software is scalable to accommodate future growth. Implementation should involve thorough training for staff to maximize adoption and utilization of the new system.
Post-implementation support and ongoing maintenance are also vital for long-term success. A phased rollout approach, starting with a pilot program in a specific department or location, can minimize disruption and allow for adjustments before a full-scale deployment.
Key Benefits of Using Inventory Management Software
- Reduced inventory costs: Optimize stock levels to minimize storage costs and reduce waste from obsolescence or spoilage.
- Improved accuracy: Minimize errors in inventory tracking, leading to more reliable data for decision-making.
- Increased efficiency: Automate manual tasks, freeing up staff time for other crucial activities.
- Better forecasting: Predict future demand more accurately, optimizing purchasing and production planning.
- Enhanced customer satisfaction: Reduce stockouts and ensure timely order fulfillment.
- Improved profitability: Optimize inventory levels, reducing costs and maximizing sales.
- Streamlined operations: Integrate various business processes for a more efficient workflow.
Challenges and Solutions in Inventory Control
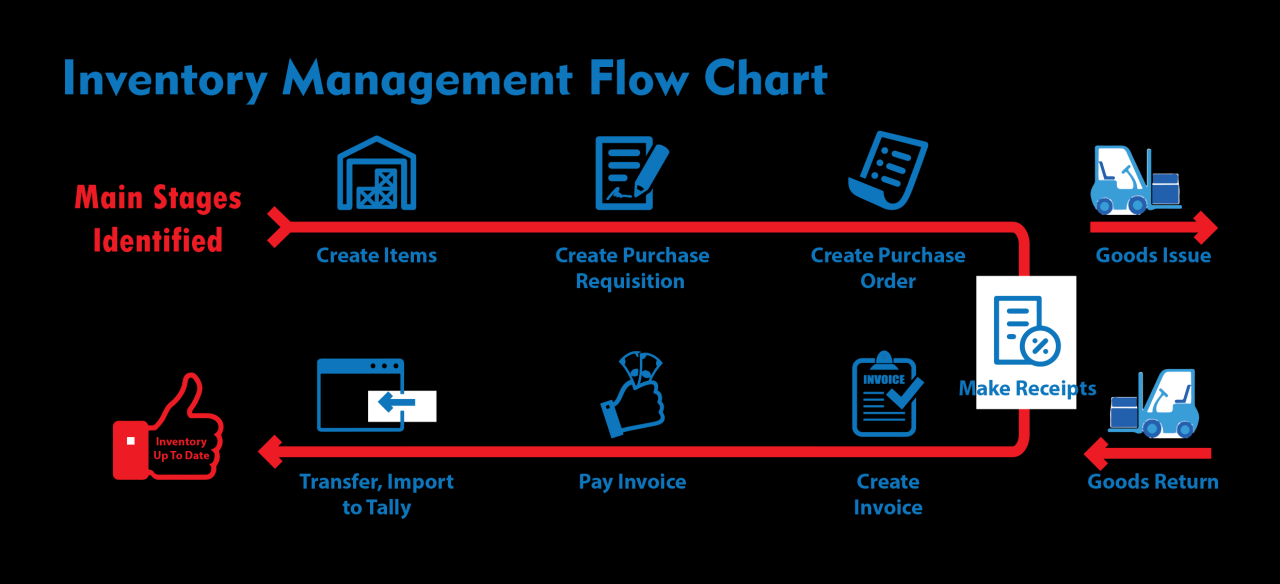
Effective inventory control is crucial for business success, but numerous challenges can hinder its efficiency. These challenges, if left unaddressed, can significantly impact profitability and operational smoothness. Understanding these obstacles and implementing appropriate solutions is key to optimizing inventory management.
Impact of Inaccurate Inventory Data
Inaccurate inventory data is a pervasive problem with far-reaching consequences. Discrepancies between physical inventory and recorded stock levels lead to poor decision-making across various business functions. For example, inaccurate data can result in stockouts, leading to lost sales and dissatisfied customers. Conversely, overstocking due to inflated inventory counts ties up capital in unsold goods, increasing storage costs and potentially leading to obsolescence or spoilage.
This ultimately affects profitability, as businesses may be forced to offer discounts to clear excess inventory or write off obsolete items entirely. The cascading effect of inaccurate data impacts forecasting, production planning, and customer service, hindering overall operational efficiency.
Minimizing Inventory Shrinkage and Waste
Inventory shrinkage, the difference between the recorded inventory and the actual physical count, is a common problem stemming from theft, damage, obsolescence, and errors in recording. Minimizing shrinkage requires a multi-pronged approach. Implementing robust security measures, such as access controls and surveillance systems, can deter theft. Regular cycle counting, a process of verifying inventory levels throughout the year rather than relying on annual physical counts, helps identify discrepancies early.
Implementing a first-in, first-out (FIFO) inventory management system helps minimize waste from spoilage or obsolescence by ensuring that older items are used first. Furthermore, proper storage and handling procedures, including appropriate temperature and humidity control for perishable goods, can significantly reduce damage and spoilage. Investing in robust inventory management software with features like automated alerts for low stock levels or approaching expiry dates can further minimize waste.
Addressing Stockouts and Overstocking
Stockouts, the inability to meet customer demand due to insufficient inventory, and overstocking, holding excessive inventory, represent opposite ends of the same spectrum – both negatively impacting profitability. Stockouts lead to lost sales, customer dissatisfaction, and potential damage to brand reputation. Overstocking, on the other hand, ties up capital, increases storage costs, and risks obsolescence or spoilage. Effective demand forecasting, using historical sales data and market trends, is crucial in mitigating both problems.
Implementing a just-in-time (JIT) inventory system, where goods are received only as needed, can minimize overstocking. Furthermore, establishing strong supplier relationships and utilizing efficient transportation and logistics networks can ensure timely replenishment of inventory and prevent stockouts. Regularly reviewing sales data and adjusting inventory levels accordingly is also crucial. For example, a retailer might analyze seasonal sales patterns to ensure sufficient stock during peak periods while avoiding overstocking during slower times.
The use of sophisticated inventory management software with forecasting capabilities can greatly enhance the accuracy of predictions and optimize inventory levels.
The Importance of Accurate Inventory Data
Accurate inventory data is the bedrock of efficient business operations. It provides the foundation for informed decision-making across various aspects of the business, directly impacting profitability and overall financial health. Without accurate data, businesses risk significant financial losses and operational inefficiencies.Accurate inventory data contributes significantly to improved decision-making by providing a clear and reliable picture of current stock levels.
This allows businesses to make informed choices regarding purchasing, production planning, and sales forecasting. For example, knowing precisely how much of a product is in stock prevents overstocking, minimizing storage costs and reducing the risk of obsolescence. Conversely, accurate data prevents stockouts, avoiding lost sales and potential damage to customer relationships. This clear understanding of inventory levels empowers businesses to optimize their supply chain, leading to smoother operations and improved customer satisfaction.
Impact on Profitability and Cash Flow, Business inventory control definition
Accurate inventory data directly impacts profitability and cash flow. Overstocking ties up capital that could be used elsewhere, leading to increased storage costs, insurance, and potential losses due to spoilage or obsolescence. Conversely, understocking results in lost sales opportunities, potentially damaging brand reputation and reducing revenue. Accurate inventory data allows businesses to maintain optimal stock levels, minimizing storage costs while maximizing sales opportunities.
This optimized inventory management improves cash flow by reducing unnecessary expenditure on excess inventory and ensuring that capital is available for other business needs. Precise inventory data also facilitates accurate cost accounting, leading to more realistic pricing strategies and improved profit margins.
Examples of Financial Losses Due to Inaccurate Inventory Data
Inaccurate inventory data can lead to a variety of financial losses. For instance, a business might overestimate its stock levels, leading to delayed or cancelled purchase orders. This can disrupt production schedules and damage relationships with suppliers. Conversely, underestimating stock can result in lost sales opportunities and dissatisfied customers. Further, inaccurate data can lead to incorrect valuation of inventory, resulting in inaccurate financial reporting and potential tax implications.
Spoilage or obsolescence of excess inventory due to poor forecasting based on inaccurate data represents a direct loss of capital. Finally, the costs associated with rectifying inaccurate inventory data, such as conducting a full physical inventory count, can be substantial.
Case Study: “The Cozy Coffee Shop”
The Cozy Coffee Shop, a small independent café, struggled with inconsistent inventory management. Their manual tracking system was prone to errors, leading to frequent stockouts of popular items like their signature blend coffee beans and certain pastries. This resulted in lost sales and frustrated customers. After implementing an inventory management software, they achieved accurate real-time inventory data.
This allowed them to optimize their ordering process, minimizing waste and ensuring sufficient stock of popular items. Within six months, they saw a 15% increase in sales and a 10% reduction in inventory-related costs. The improved efficiency also freed up the owner’s time, allowing them to focus on other aspects of the business, like marketing and customer service.
This example demonstrates how accurate inventory data can translate into tangible improvements in profitability and operational efficiency, even for small businesses.
Outcome Summary
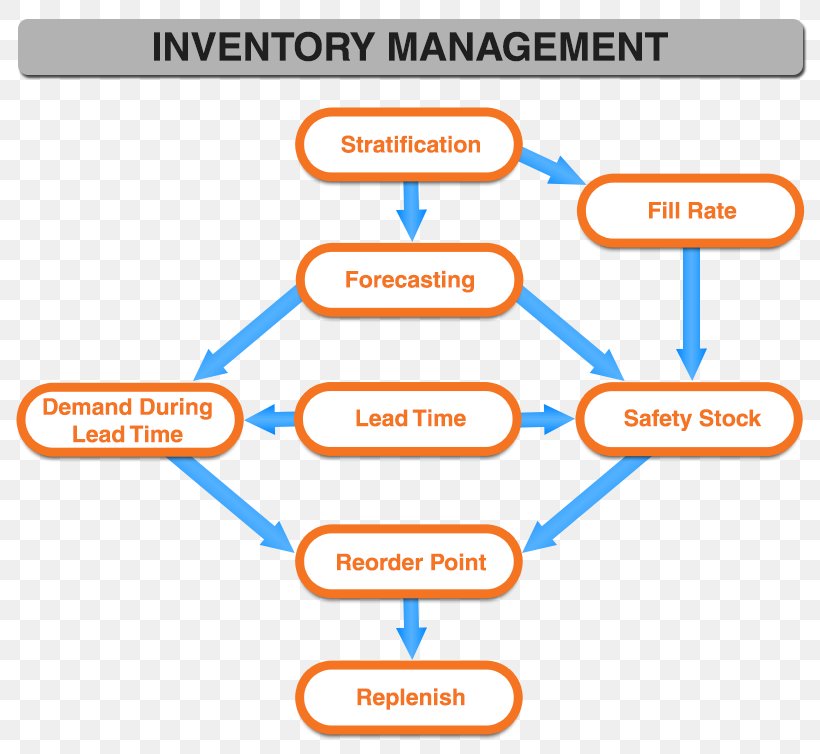
Effective business inventory control is not merely about tracking stock; it’s about strategically managing assets to maximize profitability and minimize waste. By understanding the core definitions, implementing appropriate methods, and leveraging available technology, businesses can significantly improve efficiency, reduce costs, and enhance overall operational performance. From defining inventory control to selecting the right software, this guide provides a foundational understanding to help businesses of all sizes optimize their inventory management and achieve greater success.
Remember that continuous monitoring and adaptation are key to maintaining a robust and effective inventory control system.
Popular Questions
What is the difference between inventory control and inventory management?
Inventory control focuses on the day-to-day tracking and monitoring of inventory levels. Inventory management is a broader term encompassing planning, forecasting, and strategic decision-making related to inventory.
How often should inventory be counted?
The frequency depends on factors like inventory turnover rate, product value, and risk of theft or damage. Regular cycle counting (counting a portion of inventory regularly) is often preferred over a complete annual physical count.
What are some common indicators of poor inventory control?
High stockout rates, excessive inventory holding costs, frequent discrepancies between recorded and physical inventory, and difficulty in accurately forecasting demand are all signs of poor inventory control.