Business inventory damage claims represent a significant challenge for businesses of all sizes. Understanding the various types of damage, implementing effective prevention strategies, and navigating the insurance claim process are crucial for minimizing financial losses and ensuring operational continuity. This guide provides a comprehensive overview of these critical aspects, offering practical advice and actionable steps to protect your valuable assets.
From preventing damage through proper storage and handling to effectively documenting incidents and pursuing insurance claims, we explore each stage of the process. We delve into the legal and regulatory considerations, highlighting the importance of accurate record-keeping and inventory valuation. Furthermore, we examine how technological solutions can enhance damage prevention and tracking, offering a holistic approach to managing this complex issue.
Types of Business Inventory Damage
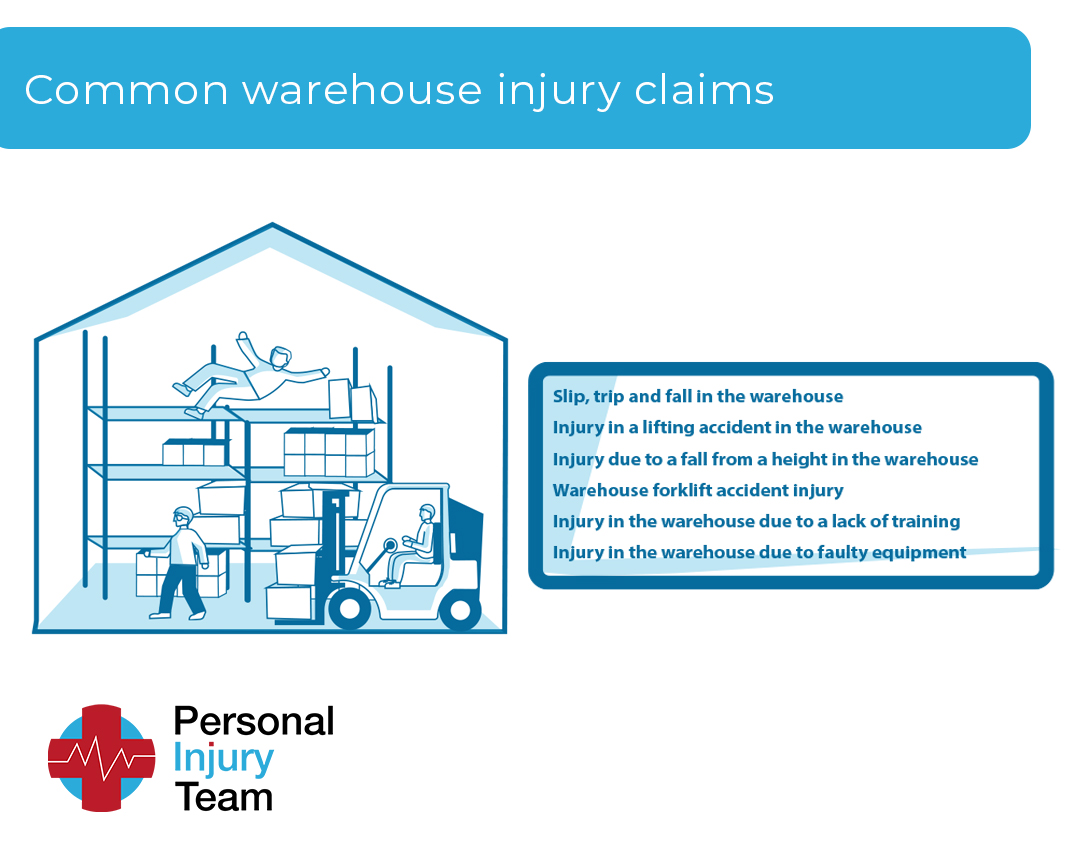
Inventory damage represents a significant operational and financial challenge for businesses of all sizes. Understanding the various types of damage, their causes, and their impact is crucial for effective loss prevention and accurate claims processing. This section categorizes common inventory damage types and explores their characteristics.
Categorization of Inventory Damage
The following table categorizes common types of inventory damage, detailing their causes and providing illustrative examples. Accurate classification is vital for insurance claims and internal loss analysis.
Type | Description | Causes | Examples |
---|---|---|---|
Physical Damage | Damage affecting the physical integrity of the product, rendering it unusable or significantly reducing its value. | Internal: Mishandling, improper storage, faulty equipment; External: Transportation accidents, natural disasters, theft. | Scratched furniture, dented cans, broken electronics, water-damaged books. |
Spoilage/Perishability | Deterioration of goods due to natural processes or improper storage conditions, leading to loss of quality and value. | Internal: Inadequate refrigeration, incorrect temperature control, expired shelf life; External: Power outages, extreme weather conditions. | Rotten produce, expired pharmaceuticals, spoiled dairy products, moldy bread. |
Theft | Unauthorized removal of inventory, resulting in complete loss of goods. | Internal: Employee theft, internal fraud; External: Burglary, shoplifting, robbery. | Missing electronics, stolen clothing, vanished raw materials, pilfered cash register funds. |
Obsolescence | Loss of value due to technological advancements, changes in consumer demand, or the introduction of superior alternatives. | Internal: Poor inventory management, overstocking of slow-moving items; External: Rapid technological change, shifting market trends. | Outdated computer hardware, discontinued clothing styles, obsolete software licenses. |
Damage in Transit | Inventory damage that occurs during shipping or transportation. | Improper packaging, rough handling, accidents during transport, inadequate climate control during transport. | Crushed boxes, broken glass items, damaged electronics due to poor handling, spoiled food due to improper temperature control during shipping. |
Impact of Inventory Damage on Business Operations
Inventory damage significantly impacts business operations in several ways. Direct losses include the cost of the damaged goods, while indirect losses encompass lost sales, increased operational costs, and potential damage to brand reputation. For example, a restaurant experiencing a refrigerator malfunction leading to spoiled food faces immediate losses in the cost of the food, potential loss of revenue due to menu item unavailability, and increased costs associated with waste disposal and restocking.
A significant incident could also affect customer trust, leading to long-term consequences.
Causes of Inventory Damage: Internal vs. External Factors
Understanding the root causes of inventory damage is essential for implementing effective preventive measures. Internal factors are often controllable, while external factors may require proactive risk management strategies. Internal factors include inadequate storage facilities, poor employee training, inefficient inventory management systems, and lack of regular inspections. External factors encompass natural disasters, theft, supplier negligence, and transportation issues. A proactive approach involves implementing robust inventory management systems, providing adequate employee training, investing in secure storage facilities, and purchasing insurance to mitigate potential losses from external factors.
Damage Prevention Strategies
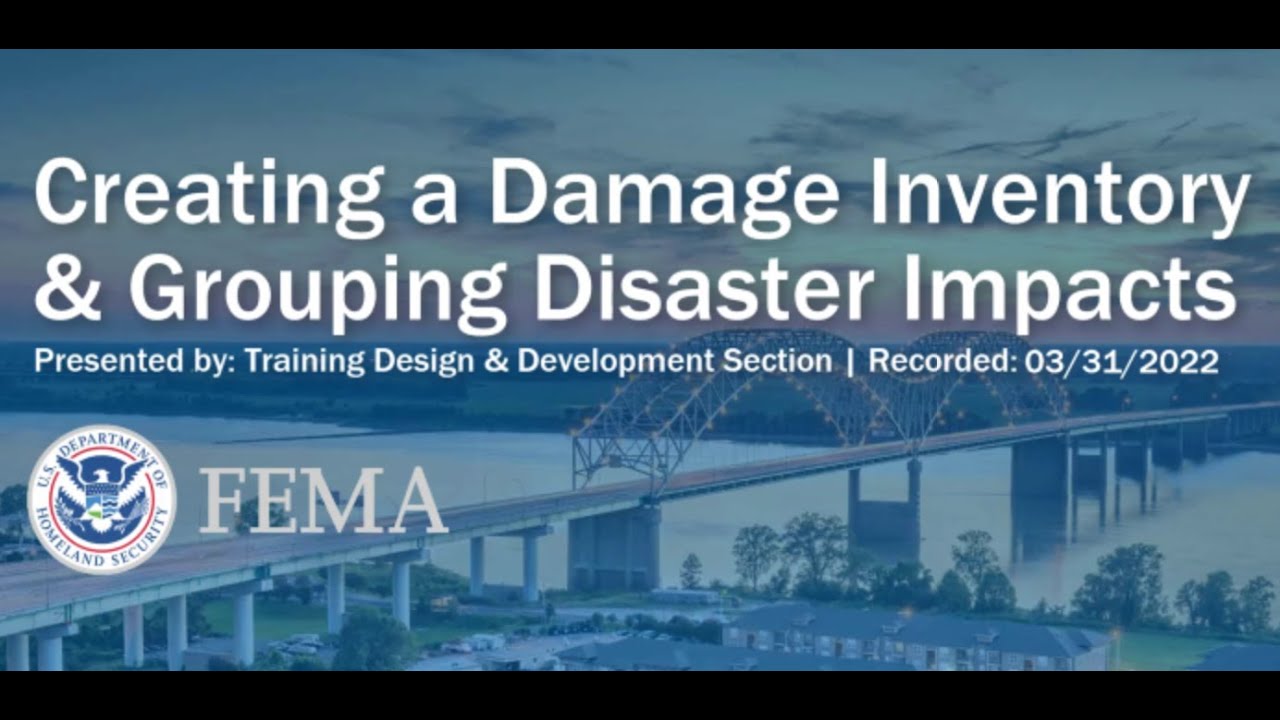
Minimizing inventory damage is crucial for maintaining profitability and operational efficiency. A proactive approach, incorporating preventative maintenance, robust organizational practices, and diligent inspection procedures, significantly reduces losses and improves overall warehouse management. This section details strategies to achieve this.
Preventative Maintenance Plan
A comprehensive preventative maintenance plan is essential for minimizing damage to inventory. Regular upkeep of equipment and facilities directly impacts the condition of stored goods. Neglecting maintenance can lead to malfunctions, accidents, and ultimately, significant inventory damage. The following plan Artikels key areas requiring attention:
- Forklift Maintenance: Regular inspections, including checks of hydraulic systems, brakes, and tires, are critical. Scheduled maintenance, including fluid changes and component replacements, should adhere to manufacturer recommendations. Operator training and certification are also crucial for preventing accidents.
- Racking System Inspections: Regular visual inspections of racking systems should identify any signs of damage, such as bending or warping. Load capacity limits should be strictly adhered to, and damaged racking should be immediately repaired or replaced.
- Environmental Controls: Maintaining appropriate temperature and humidity levels is crucial for preventing damage to temperature-sensitive goods. Regular checks of HVAC systems and environmental monitoring equipment are essential. Consider installing backup power systems to maintain temperature control during power outages.
- Pest Control: Regular pest control measures, including inspections and treatments, are vital to protect inventory from infestation. Proper sanitation practices and sealing of entry points are also important.
- Building Maintenance: Regular inspections of the warehouse building itself, including the roof, walls, and doors, should be conducted to identify and address any potential issues that could lead to damage. This includes addressing leaks, cracks, or structural weaknesses.
Warehouse Organization and Inventory Management Best Practices
Effective warehouse organization and inventory management significantly reduce the risk of damage. Implementing best practices ensures efficient storage, easy accessibility, and minimizes the handling required, thus protecting inventory.
- Proper Storage Techniques: Utilize appropriate shelving and racking systems for different product types and sizes. Ensure adequate spacing between pallets to allow for easy access and movement. Heavy items should be stored on lower shelves, and fragile items should be placed in designated areas and properly protected.
- First-In, First-Out (FIFO) System: Implementing a FIFO system ensures that older inventory is used before newer inventory, reducing the risk of spoilage or obsolescence. This is particularly important for perishable goods.
- Clear Labeling and Identification: Clearly labeling all inventory items with relevant information, such as product name, quantity, and date of receipt, helps to prevent misplacement and accidental damage. This facilitates quick identification and efficient stock management.
- Designated Areas for Damaged Goods: Establish a designated area for damaged goods to separate them from undamaged inventory. This prevents further damage and facilitates efficient handling of damaged items.
- Inventory Tracking System: Implementing a robust inventory tracking system allows for real-time monitoring of stock levels, identifying potential issues and preventing stockouts or overstocking which can lead to damage.
Regular Inspection and Preventative Measures Checklist
Regular inspections are key to identifying and addressing potential damage risks before they escalate. This checklist provides a framework for consistent monitoring and preventative action.
- Daily Inspections: Check for any signs of damage to inventory, equipment, or the warehouse structure. Address any immediate hazards.
- Weekly Inspections: Inspect racking systems for stability and damage. Check environmental controls (temperature, humidity). Verify pest control measures.
- Monthly Inspections: Conduct a more thorough inspection of the entire warehouse, including equipment maintenance records and safety protocols.
- Annual Inspections: Comprehensive inspection of the warehouse building and all equipment, including structural integrity checks and major maintenance.
Proper Packaging and Handling
Proper packaging and handling are crucial for protecting inventory during storage and transportation. Inadequate packaging can lead to significant damage, especially during transit.
- Appropriate Packaging Materials: Use sturdy and appropriate packaging materials for different product types, considering weight, fragility, and environmental conditions. This includes selecting suitable boxes, cushioning materials, and protective films.
- Proper Packing Techniques: Items should be securely packed to prevent shifting or breakage during transport. Use sufficient cushioning materials to protect fragile items. Proper labeling and handling instructions should be clearly visible.
- Careful Handling Procedures: Train staff on proper lifting and handling techniques to minimize the risk of damage. Use appropriate equipment for heavy items and ensure careful handling of fragile goods.
- Secure Transportation: Ensure goods are properly secured during transportation to prevent damage from vibration or impact. Use appropriate vehicles and secure the load effectively.
Documentation and Reporting Procedures: Business Inventory Damage Claims
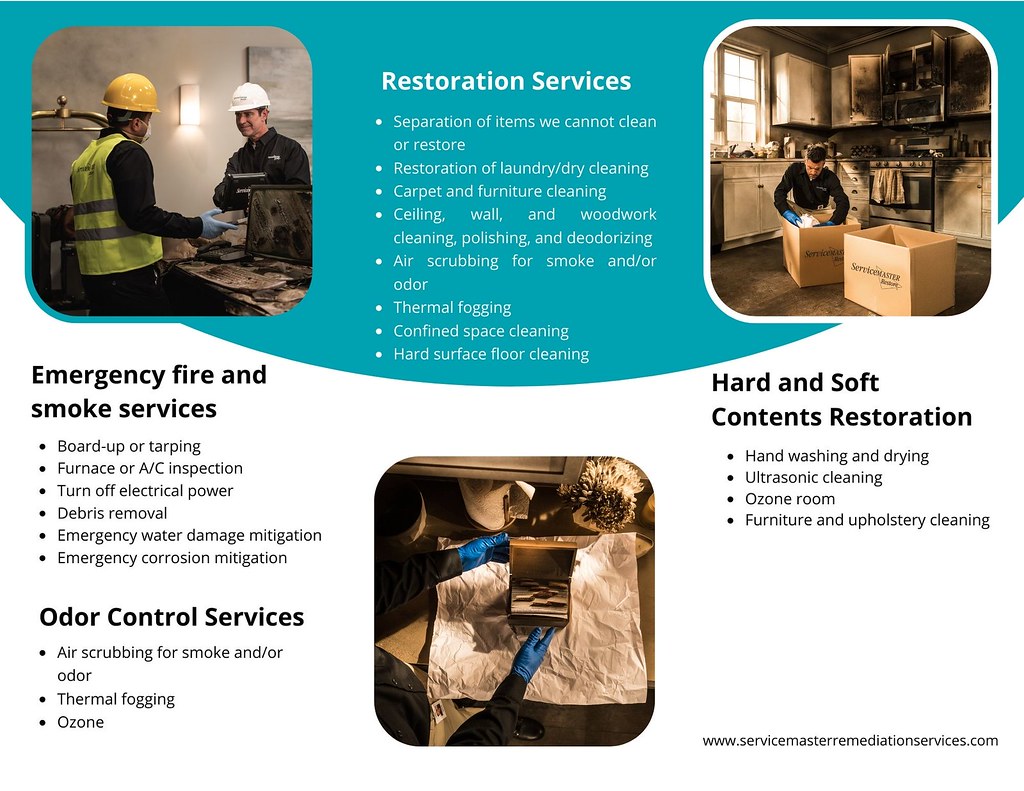
Meticulous documentation and reporting are crucial for successful inventory damage claims. Accurate records provide irrefutable evidence of the damage, its extent, and the resulting financial losses. This significantly strengthens your claim and increases the likelihood of a swift and fair settlement from your insurance provider. Failing to maintain proper documentation can lead to delays, claim denials, or even partial reimbursements.Proper record-keeping is essential for insurance claims.
Detailed documentation supports your claim by providing objective evidence of the damage, its cause, and the associated costs. This evidence minimizes disputes and speeds up the claims process. The absence of comprehensive records can significantly weaken your claim, potentially resulting in a reduced payout or claim rejection.
Inventory Damage Incident Documentation Procedure
A systematic approach to documenting inventory damage is vital. This procedure ensures all necessary information is collected and preserved, facilitating a smooth insurance claim process. The following steps Artikel a recommended procedure.
- Immediate Assessment: Immediately after discovering the damage, assess the situation. Note the date, time, and location of the incident. Take photographs or videos of the damaged inventory from multiple angles, clearly showing the extent of the damage.
- Detailed Inventory Listing: Create a detailed list of all damaged items. Include item descriptions, quantities, model numbers (if applicable), and purchase dates. If possible, cross-reference with your existing inventory management system.
- Damage Description: Provide a precise description of the damage sustained by each item. Use clear and concise language, avoiding subjective terms. For example, instead of “slightly damaged,” specify “small dent on the side panel.”
- Cost Estimation: Estimate the cost of repair or replacement for each damaged item. Use receipts, invoices, or market prices as references. Include any additional costs associated with the damage, such as disposal fees or lost revenue.
- Witness Statements: If there were any witnesses to the incident, obtain their written statements. Include their contact information.
- Secure Evidence: Preserve all damaged items, photographs, videos, and other relevant documentation in a safe and organized manner. This evidence will be essential for your insurance claim.
Example Damage Report
The following table illustrates a sample damage report, highlighting the key information to include.
Date | Item | Damage Description | Estimated Cost |
---|---|---|---|
2024-10-27 | Laptop – Model XYZ123 | Cracked screen, non-functional | $800 |
2024-10-27 | Office Chair – Model ABC456 | Broken leg, unusable | $150 |
2024-10-27 | Packaging Supplies (Boxes) | Water damaged, unusable | $50 |
2024-10-26 | Inventory A | Scratches on the surface | $20 |
Reporting Damage to Insurance Providers
Promptly reporting the damage to your insurance provider is critical. Follow these steps to ensure a smooth claims process.
- Review Policy: Review your insurance policy to understand the claims procedure and required documentation.
- Contact Insurance: Contact your insurance provider immediately to report the incident. Obtain a claim number and follow their instructions carefully.
- Submit Documentation: Submit all collected documentation to your insurance provider. This includes the damage report, photographs, videos, invoices, and witness statements.
- Follow Up: Follow up with your insurance provider regularly to check on the status of your claim. Keep detailed records of all communication.
Insurance Claim Process
Filing a successful insurance claim after inventory damage requires a methodical approach. Understanding the process and preparing thoroughly will significantly increase your chances of receiving fair compensation. This section Artikels the typical steps involved, offers advice on maximizing reimbursement, and highlights the crucial role of documentation.
The insurance claim process can vary slightly depending on your insurer and the specifics of your policy, but the general steps remain consistent. Careful preparation and detailed documentation are key to a smooth and successful claim.
Steps Involved in Filing a Business Inventory Damage Claim
Following these steps will help ensure a smooth and efficient claims process. Accurate and timely reporting is vital for a successful outcome.
- Report the Damage Immediately: Contact your insurance provider as soon as possible after discovering the damage. Many policies have reporting deadlines, so prompt action is crucial.
- Document the Damage: Thoroughly document the damage with photographs, videos, and detailed descriptions of each damaged item. Include dates, times, and locations where applicable.
- File a Formal Claim: Complete the necessary claim forms provided by your insurer. Be accurate and thorough in providing all requested information.
- Provide Supporting Documentation: Submit all relevant documentation, including receipts, invoices, inventory lists, and appraisals. This supports the value of your lost or damaged inventory.
- Cooperate with the Adjuster: Fully cooperate with the insurance adjuster assigned to your claim. Provide access to the damaged inventory and answer their questions honestly and completely.
- Review the Settlement Offer: Carefully review the settlement offer from your insurer. Negotiate if necessary to ensure you receive fair compensation for your losses.
Preparing a Compelling Claim
A well-prepared claim significantly increases your chances of a favorable outcome. Consider these strategies to strengthen your claim.
- Detailed Inventory Records: Maintain accurate and up-to-date inventory records, including purchase dates, costs, and descriptions. This facilitates a quick and accurate assessment of your losses.
- Professional Appraisal: For high-value items, consider obtaining a professional appraisal to establish their value before the damage occurred. This provides objective evidence of worth.
- Comprehensive Documentation: Gather all relevant documentation, including photos, videos, police reports (if applicable), and witness statements. The more evidence you provide, the stronger your claim will be.
- Accurate Cost Calculations: Carefully calculate the cost of replacing or repairing the damaged inventory. Include all relevant expenses, such as disposal fees and potential lost profits.
Role of Documentation and Evidence
Documentation is the cornerstone of a successful insurance claim. Strong evidence substantiates your claim and minimizes disputes.
Examples of crucial documentation include:
- Photographs and Videos: High-quality images and videos clearly showing the extent of the damage.
- Inventory Lists: Detailed lists of all damaged items, including descriptions, quantities, and purchase prices.
- Receipts and Invoices: Proof of purchase for all damaged items.
- Police Reports: If the damage resulted from a theft or other crime.
- Witness Statements: Statements from anyone who witnessed the damage or has relevant information.
Comparison of Insurance Policies and Coverage, Business inventory damage claims
Inventory insurance policies vary widely in their coverage. Understanding the differences is crucial for selecting the right policy for your business needs.
Key factors to consider include:
- Coverage Limits: The maximum amount the insurer will pay for a single claim or over a policy period.
- Types of Covered Damages: Some policies cover specific types of damage (e.g., fire, water, theft), while others offer broader coverage.
- Deductibles: The amount you must pay out-of-pocket before the insurance coverage kicks in.
- Policy Exclusions: Specific events or circumstances that are not covered by the policy.
For example, a standard business owner’s policy might offer limited inventory coverage, while a specialized inland marine policy provides more comprehensive protection for goods in transit or storage. Carefully compare policies and their coverage details before selecting one for your business.
Cost Assessment and Loss Mitigation
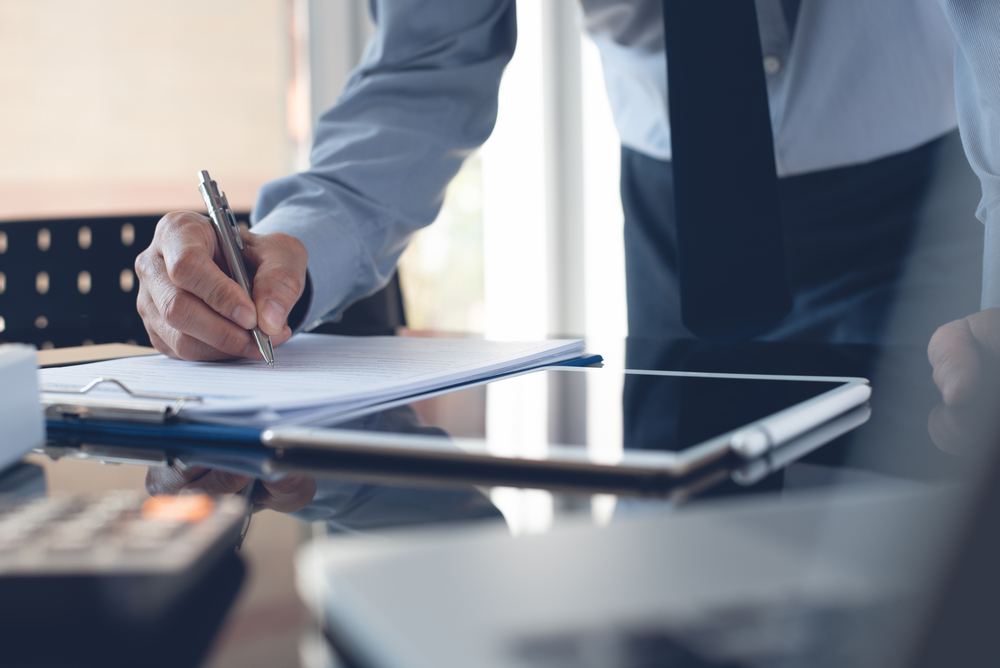
Accurately assessing the financial impact of inventory damage is crucial for effective claim processing and business continuity. Understanding the total cost, encompassing not only the immediate damage but also subsequent expenses, allows for better resource allocation and minimizes future losses. This section details methods for calculating these costs and strategies for mitigating the overall financial impact.Accurate cost assessment requires a systematic approach.
This involves a detailed inventory of damaged goods, determining their original cost, and calculating the cost of disposal and replacement.
Calculating Total Cost of Damage
Calculating the total cost of damage involves several steps. First, determine the value of the damaged inventory. This is typically done by referencing purchase invoices or inventory management software. Next, calculate the disposal costs. This might include the cost of waste removal, recycling fees, or specialized disposal services for hazardous materials.
Finally, determine the replacement cost. This includes the cost of purchasing new inventory, factoring in any potential price increases since the original purchase. The total cost of damage is the sum of the original inventory value, disposal costs, and replacement costs. For example, if 100 units of a product costing $10 each were damaged, disposal cost $50, and replacement cost is $12 per unit, the total cost would be ($1000 + $50 + $1200) = $2250.
Loss Mitigation Strategies
Effective loss mitigation begins immediately after the damage event. Quick action can significantly reduce the overall financial impact. This involves securing the damaged area, preventing further damage, and initiating the damage assessment process as quickly as possible. A well-defined emergency response plan should be in place to guide these initial steps.
Salvaging Damaged Inventory
Not all damaged inventory is a total loss. Depending on the nature and extent of the damage, some items may be salvaged and resold at a reduced price, used for parts, or repurposed. For example, slightly damaged goods might be sold as “seconds” or “blemished” products, while components from severely damaged items might be reused. A thorough assessment of the salvageable inventory should be undertaken to maximize recovery.
This assessment should consider the cost of repair or refurbishment versus the potential resale value. Thorough documentation of the salvage process is crucial for insurance claims.
Legal and Regulatory Considerations
Navigating the complexities of business inventory damage claims often involves understanding and adhering to various legal and regulatory requirements. Failure to comply can lead to significant financial and legal repercussions, impacting your business’s reputation and bottom line. This section Artikels key legal considerations and the importance of precise inventory valuation and effective communication with insurance adjusters.Accurate record-keeping and compliance with relevant regulations are paramount in successfully processing inventory damage claims.
These regulations vary by location and industry, encompassing aspects like safety standards, reporting requirements, and tax implications related to losses. Understanding these regulations is crucial for ensuring a smooth claims process and avoiding potential legal disputes.
Relevant Legal and Regulatory Requirements
Numerous laws and regulations impact how businesses handle inventory damage and insurance claims. These vary depending on the jurisdiction, the nature of the business, and the type of inventory involved. For example, regulations concerning hazardous materials will differ significantly from those governing retail clothing. Compliance often involves maintaining detailed records of inventory, adhering to safety protocols to prevent damage, and promptly reporting incidents to relevant authorities and insurers.
Failure to meet these requirements can result in penalties, delays in claim processing, and even denial of coverage. Specific examples include OSHA regulations regarding workplace safety and environmental regulations related to disposal of damaged goods.
Implications of Non-Compliance
Non-compliance with legal and regulatory requirements related to inventory damage can have severe consequences. These can range from financial penalties and legal action to reputational damage and loss of insurance coverage. Delays in reporting damage or inadequate record-keeping can weaken your claim, making it harder to prove the extent of your losses and receive fair compensation. In some cases, non-compliance can even lead to criminal charges, particularly if the damage involves hazardous materials or deliberate negligence.
For instance, a business failing to properly report a chemical spill that damaged inventory might face significant fines and legal repercussions.
Accurate Inventory Valuation for Insurance Purposes
Accurate inventory valuation is crucial for determining the amount of compensation you can receive for damaged goods. Insurance policies typically require businesses to maintain detailed and up-to-date inventory records, including purchase dates, costs, and current market values. Methods like the first-in, first-out (FIFO) or last-in, first-out (LIFO) methods can be used to determine the cost of goods sold and the value of remaining inventory.
Using outdated or inaccurate valuation methods can lead to underinsurance and a reduced payout in the event of a loss. A comprehensive inventory management system, regularly updated, is essential for accurate valuation. For example, using a barcode system to track inventory allows for a quick and precise assessment of losses.
Working with Insurance Adjusters
Effective communication and collaboration with insurance adjusters are essential for a successful claim. Adjusters will investigate the damage, review your documentation, and determine the extent of the insurer’s liability. Providing them with complete and accurate information promptly will streamline the claims process. This includes detailed damage reports, supporting documentation such as purchase invoices and inventory records, and any relevant photographs or videos.
Open communication and proactive cooperation with the adjuster can significantly improve the chances of a fair and timely settlement. Maintaining a detailed record of all communications with the adjuster is also recommended.
Technological Solutions for Damage Prevention and Tracking
Technology plays a crucial role in minimizing inventory damage and enhancing the efficiency of damage tracking within a business. By implementing various technological solutions, companies can significantly reduce losses, improve operational efficiency, and strengthen their overall inventory management capabilities. This section explores several key technological advancements and their applications in preventing and tracking inventory damage.
Inventory Management Software and Damage Tracking Features
Modern inventory management software offers a range of features specifically designed to track and prevent inventory damage. These systems provide real-time visibility into inventory levels, location, and condition, enabling proactive damage prevention and efficient claims processing. For instance, some software allows users to record damage details directly within the system, linking the damage to specific inventory items and potentially even to the responsible party or event.
This detailed record-keeping simplifies the insurance claims process and allows for better analysis of damage patterns, helping identify areas for improvement in warehouse operations or handling procedures. Popular examples include Fishbowl Inventory, Zoho Inventory, and NetSuite, each offering varying levels of functionality and integration with other business systems. These systems often include features like automated alerts for low stock levels, which can help prevent damage from improper storage or handling due to overcrowding.
RFID and Barcode Systems for Inventory Tracking and Damage Detection
Radio-Frequency Identification (RFID) and barcode systems are powerful tools for real-time inventory tracking and damage detection. RFID tags, unlike barcodes, do not require line-of-sight scanning, allowing for faster and more accurate tracking of inventory movement within a warehouse. This technology enables automated detection of damaged goods through the integration of sensors that detect changes in weight, temperature, or other relevant parameters.
Similarly, advanced barcode systems can be integrated with inventory management software to automatically flag damaged items based on scans that reveal discrepancies in expected versus actual condition. For example, a barcode scan might indicate a package is damaged upon arrival, automatically triggering an alert within the inventory management system. This immediate notification enables faster response times, minimizing secondary damage and facilitating efficient claims processing.
Technological Solutions for Improving Warehouse Security and Reducing Damage Risks
Several technological solutions enhance warehouse security and mitigate damage risks. These solutions include:
- Surveillance Systems: Closed-circuit television (CCTV) cameras provide visual monitoring of warehouse activities, deterring theft and vandalism, and enabling identification of the cause of damage events. Advanced systems might incorporate analytics to detect unusual patterns or activities that could indicate potential damage risks.
- Access Control Systems: Restricting access to authorized personnel only reduces the risk of accidental or intentional damage. This can be achieved through card readers, biometric authentication, or other controlled entry systems.
- Environmental Monitoring Systems: Sensors monitor temperature, humidity, and other environmental factors that can contribute to inventory damage. Automated alerts notify staff of deviations from optimal conditions, allowing for timely intervention.
- Automated Guided Vehicles (AGVs): AGVs reduce the risk of damage caused by human error during material handling. Their precise movements minimize collisions and ensure efficient transport of goods.
Implementing these technologies helps create a safer and more efficient warehouse environment, reducing the likelihood of inventory damage and streamlining the claims process. The combination of these solutions provides a comprehensive approach to minimizing damage and optimizing warehouse operations.
Final Wrap-Up
Effectively managing business inventory damage claims requires a proactive and multi-faceted approach. By implementing preventative measures, maintaining meticulous records, and understanding the insurance claim process, businesses can significantly reduce financial losses and operational disruptions. This guide has provided a framework for navigating this complex area, empowering businesses to protect their assets and maintain profitability. Remember, preparedness and proactive management are key to minimizing the impact of inventory damage.
Query Resolution
What types of insurance cover inventory damage?
Several policies, including business interruption insurance, property insurance, and specialized inventory insurance, can cover inventory damage. Coverage varies depending on the policy and the cause of the damage.
What if my insurance company denies my claim?
If your claim is denied, review the policy details carefully and gather additional supporting documentation. You may need to appeal the decision or consult with a legal professional.
How do I determine the value of damaged inventory for insurance purposes?
Accurate valuation involves considering factors like purchase price, replacement cost, and any depreciation. Maintaining detailed inventory records is essential for accurate assessment.
What is the role of an insurance adjuster in a damage claim?
An adjuster investigates the claim, assesses the damage, and determines the amount of compensation to be paid. Cooperation with the adjuster is crucial for a smooth claims process.