Business inventory for real estate construction presents unique challenges and opportunities. Effective management of materials, equipment, and supplies is crucial for on-time and within-budget project completion. This exploration delves into the intricacies of inventory control within the dynamic world of real estate development, examining strategies, technologies, and risk mitigation techniques essential for success.
From defining the specific types of inventory involved in real estate construction to exploring the impact on project costs and profitability, we will cover a wide range of topics. We will also discuss the role of technology in optimizing inventory management, including the use of BIM, barcode systems, and specialized software. Finally, we’ll examine legal and regulatory aspects, as well as the growing importance of sustainability in managing construction materials.
Defining Business Inventory in Real Estate Construction: Business Inventory For Real Estate Construction
Business inventory in real estate construction represents the tangible assets a construction company owns and intends to use in its projects. Unlike retail inventory, which focuses on finished goods for sale, construction inventory comprises materials, equipment, and supplies used in the building process. Effective management of this inventory is crucial for project profitability and timely completion.
Real estate construction inventory encompasses a wide array of items, each playing a vital role in the project lifecycle. Proper categorization and tracking of these items are essential for efficient resource allocation and cost control.
Types of Real Estate Construction Inventory
Construction inventory is diverse and can be broadly classified into several categories. These categories aid in organizing, tracking, and managing the considerable volume of materials and equipment involved in large-scale projects. Effective inventory management hinges on a clear understanding of these different types.
These categories include:
- Raw Materials: This includes basic building components such as lumber, cement, steel, bricks, and aggregates. The quantity and quality of these materials directly impact project timelines and costs.
- Work-in-Progress (WIP): This refers to partially completed components or assemblies, such as prefabricated wall sections or roof trusses. Tracking WIP inventory is critical for monitoring project progress and identifying potential bottlenecks.
- Finished Goods: While less common than in other industries, finished goods in construction could include prefabricated modules or custom-designed elements ready for installation.
- Equipment and Machinery: This comprises heavy machinery (e.g., excavators, cranes), smaller tools (e.g., drills, saws), and specialized equipment specific to the project. Maintenance and proper allocation of equipment are key factors in project efficiency.
- Supplies and Consumables: This category includes items such as fasteners, paint, adhesives, and protective gear. While individually inexpensive, these items collectively represent a significant cost component.
Distinguishing Characteristics of Real Estate Construction Inventory
Real estate construction inventory differs significantly from other types of business inventory due to several key characteristics. Understanding these differences is vital for choosing the appropriate inventory management strategies.
Key distinguishing features include:
- High Value and Perishability: Certain materials, like specialized concrete mixes or certain types of lumber, can have a short shelf life or be subject to spoilage, impacting their value and usability.
- Project Specificity: Inventory is often tailored to specific projects, limiting its reusability on other projects and increasing the risk of obsolescence or waste.
- Site-Specific Location: Inventory is frequently dispersed across multiple construction sites, posing challenges for accurate tracking and control.
- Large Volume and Variety: Construction projects involve a vast quantity and diversity of materials, demanding robust inventory management systems.
- High Risk of Theft and Damage: The nature of construction sites increases the vulnerability of inventory to theft, damage, and loss.
Comparison of Inventory Management Systems
Several inventory management systems can be adapted for real estate construction. The choice depends on the size and complexity of the projects, budget, and technological capabilities.
Inventory Management System | Pros | Cons | Suitability for Real Estate Construction |
---|---|---|---|
Spreadsheet-based System | Simple, low cost, readily available | Limited scalability, prone to errors, lacks advanced features | Suitable for small projects with limited inventory |
Enterprise Resource Planning (ERP) System | Comprehensive functionality, integration with other business systems, scalability | High initial cost, complex implementation, requires specialized expertise | Suitable for large construction firms managing multiple projects |
Cloud-based Inventory Management Software | Accessibility from anywhere, real-time data, cost-effective | Dependence on internet connectivity, potential security concerns | Suitable for medium to large projects requiring remote access and collaboration |
Barcoding and RFID Systems | Accurate tracking, real-time inventory visibility, reduced manual data entry | Higher initial investment, requires specialized equipment and training | Suitable for large projects requiring precise inventory control and traceability |
Inventory Management Strategies for Real Estate Construction
Effective inventory management is crucial for success in real estate construction, impacting project timelines, budgets, and overall profitability. A well-defined strategy minimizes waste, reduces storage costs, and ensures materials are available when needed. The optimal approach, however, varies significantly depending on the project’s scale and complexity.
Inventory Management Strategies for Small-Scale Projects
Small-scale projects, such as single-family homes or small renovations, often benefit from a simplified inventory management approach. This typically involves a less formal system relying heavily on close communication between the contractor and suppliers.
This strategy prioritizes just-in-time delivery, minimizing storage space and reducing the risk of material obsolescence or damage. However, it necessitates meticulous planning and reliable supplier relationships to ensure timely delivery and avoid project delays. The advantages include lower storage costs and reduced risk of waste. Disadvantages include a higher dependence on supplier reliability and a potential for delays if deliveries are not met.
Inventory Management Strategies for Medium-Scale Projects
Medium-scale projects, such as multi-family dwellings or small commercial buildings, require a more structured inventory management system. This might involve utilizing spreadsheets or simple inventory management software to track materials, monitor consumption rates, and forecast future needs.
A balanced approach combining just-in-time delivery for some materials with a small stockpile of commonly used items is often effective. This allows for flexibility while mitigating the risk of delays associated with solely relying on just-in-time delivery. Advantages include improved control over inventory levels and better forecasting capabilities. Disadvantages include increased storage costs compared to a purely just-in-time system and the potential for some stock to become obsolete.
Inventory Management Strategies for Large-Scale Projects
Large-scale projects, such as high-rise buildings or large-scale developments, demand sophisticated inventory management systems. These often incorporate dedicated inventory management software with features like automated ordering, real-time tracking, and reporting capabilities. A robust system is essential to manage the vast quantities of materials involved.
These projects often utilize a combination of just-in-time delivery for specialized or less frequently used materials and significant stockpiles for commonly used materials to ensure a consistent supply and minimize disruption. Advantages include enhanced visibility into inventory levels, improved forecasting accuracy, and minimized project delays. Disadvantages include high initial investment in software and infrastructure, and substantial storage costs associated with holding large stockpiles.
The risk of obsolescence or material damage also increases with larger stockpiles.
Just-in-Time Inventory versus Stockpiling
The choice between a just-in-time inventory system and holding significant stockpiles represents a crucial decision in real estate construction inventory management. Just-in-time minimizes storage costs and reduces the risk of waste but increases reliance on supplier reliability and potentially introduces project delays. Stockpiling provides a buffer against delays and ensures material availability but increases storage costs and the risk of obsolescence or damage.
The optimal approach often involves a hybrid strategy, balancing the advantages and disadvantages of both systems. For instance, a large project might use just-in-time for specialized items and stockpile common materials.
Best Practices for Optimizing Inventory Levels
Optimizing inventory levels requires a multifaceted approach. Accurate forecasting based on historical data and project specifications is essential. Regular inventory audits help identify discrepancies and prevent losses. Implementing a robust system for tracking material usage and waste helps refine forecasting models and identify areas for improvement. Strong supplier relationships are crucial for ensuring timely delivery and managing potential supply chain disruptions.
Finally, the use of technology, such as barcoding and RFID tracking, enhances accuracy and efficiency in inventory management.
Impact of Inventory on Real Estate Construction Project Costs
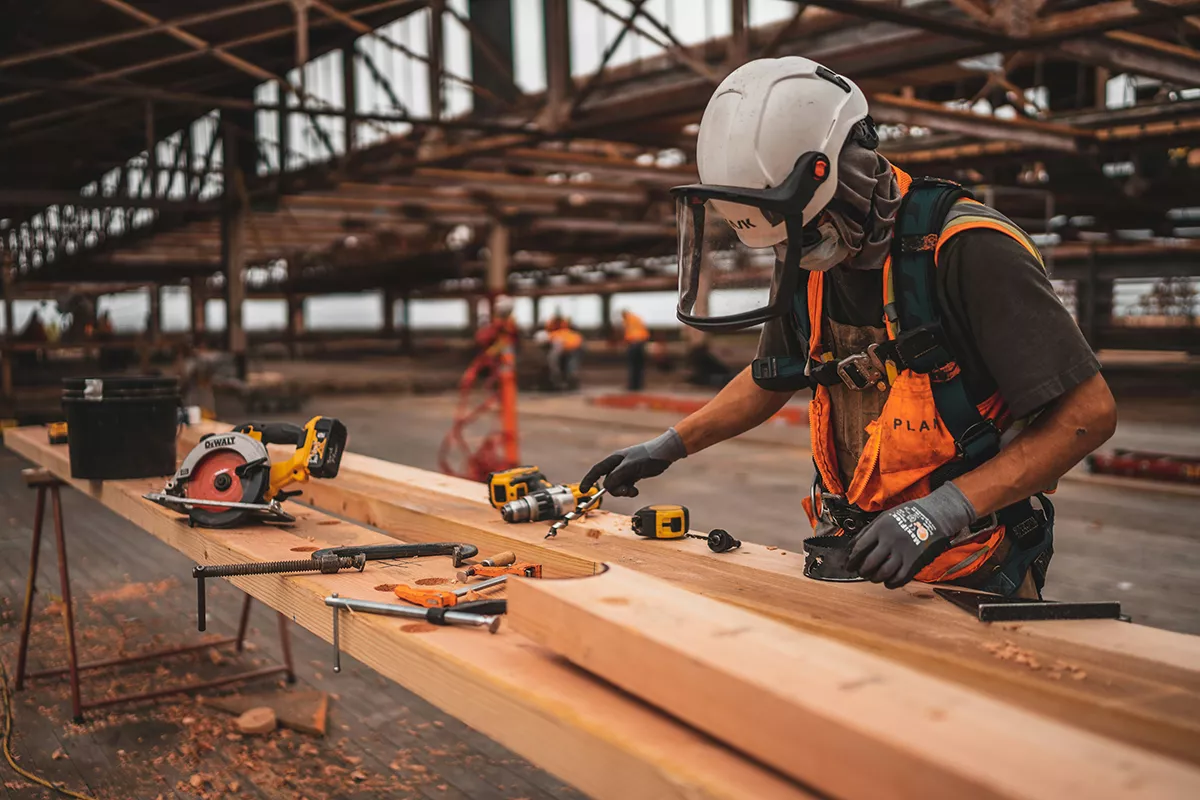
Effective inventory management is crucial for successful real estate construction projects. Poorly managed inventory can significantly inflate project costs and erode profitability, while a well-structured system can lead to substantial savings and improved project timelines. This section will explore the key cost drivers associated with inventory in construction and demonstrate how optimized management can lead to better financial outcomes.Inventory in construction projects encompasses a wide range of materials, from lumber and concrete to specialized fixtures and fittings.
The costs associated with managing this inventory are multifaceted and can impact the bottom line significantly. Understanding these costs and implementing strategies to mitigate them is essential for project success.
Key Cost Drivers Associated with Inventory Management
Several factors contribute to the overall cost of managing inventory in real estate construction. These include the direct costs of purchasing materials, the indirect costs of storage and handling, and the potential for losses due to obsolescence, damage, or theft. Effective management minimizes these costs, maximizing profitability. For instance, overstocking leads to increased storage costs and the risk of materials becoming obsolete before use, while understocking can cause project delays and increased labor costs.
Inventory Holding Costs and Project Profitability
Holding costs represent a significant portion of the total inventory cost. These costs encompass storage fees (rent for warehousing, on-site storage space), insurance premiums to protect against loss or damage, and the cost of obsolescence, where materials become outdated or unusable before they can be incorporated into the project. These holding costs directly reduce project profitability. For example, a large construction project might incur significant storage costs for materials held on-site for extended periods, eating into the project’s overall profit margin.
The longer materials are held, the higher the risk of obsolescence, further impacting profitability. Accurate forecasting and efficient procurement are critical to minimize these costs.
Effective Inventory Management and Cost Reduction
Effective inventory management strategies directly contribute to cost reduction and improved profitability in real estate construction. By implementing a robust system that tracks materials, predicts demand accurately, and optimizes procurement, construction companies can significantly reduce waste and improve project efficiency. This translates to lower overall project costs and higher profit margins. For example, a just-in-time inventory system can significantly reduce storage costs by ensuring materials arrive on-site only when needed.
Furthermore, reducing waste through careful planning and accurate quantity estimations contributes to lower material costs.
Strategies for Minimizing Inventory-Related Costs
Implementing a combination of strategies is key to minimizing inventory-related costs. This includes focusing on waste reduction and implementing efficient procurement practices.A crucial aspect is waste reduction. This involves careful planning during the design phase, precise quantity estimations based on detailed blueprints and specifications, and the use of Building Information Modeling (BIM) software to optimize material usage and minimize waste generation.
Efficient procurement practices, including negotiating favorable pricing with suppliers, establishing strong supplier relationships, and utilizing technology to streamline the purchasing process, also contribute significantly to cost savings. Strategies like bulk purchasing (when appropriate and storage capacity allows) can leverage economies of scale. Regular inventory audits and the use of barcodes or RFID tracking systems for precise inventory control also play a significant role in efficient management.
Technological Solutions for Real Estate Construction Inventory
Effective inventory management is crucial for successful real estate construction projects. Timely access to materials, accurate tracking of quantities, and efficient waste reduction all contribute to on-time and within-budget project completion. Technological solutions offer significant advancements in streamlining these processes, improving efficiency, and reducing costs.
Building Information Modeling (BIM) for Inventory Tracking and Management
Building Information Modeling (BIM) offers a powerful approach to integrating inventory management into the broader project lifecycle. BIM software creates a digital representation of the physical and functional characteristics of a building. This digital twin allows for precise tracking of materials, from initial procurement through to installation. By linking material quantities within the BIM model to actual inventory levels, project managers gain real-time visibility into material availability and potential shortages.
This allows for proactive ordering and minimizes project delays caused by missing materials. For example, a BIM model can automatically generate a materials list based on the design, which can then be compared to actual inventory, highlighting discrepancies. This proactive approach ensures that materials are ordered in advance, preventing delays and ensuring that the construction process remains on schedule.
Barcode and RFID Technologies for Real-Time Inventory Monitoring
Barcode and Radio-Frequency Identification (RFID) technologies provide real-time tracking capabilities for construction materials. Barcodes, applied to individual items or packages, allow for quick scanning and identification using handheld scanners. RFID tags, however, offer a more advanced solution. They can be read without line-of-sight, allowing for automated tracking of materials as they move through the construction site. This provides a more accurate and efficient way to monitor inventory levels, reducing the risk of manual errors and improving the overall accuracy of inventory counts.
Imagine a scenario where RFID tags are attached to every pallet of lumber. As the pallets move across the site, their location and quantity are automatically updated in a central database, giving project managers a continuous, accurate picture of their inventory.
Software Solutions for Real Estate Construction Inventory Management
Several software solutions are specifically designed to manage inventory in the real estate construction sector. These platforms typically integrate with other project management tools and often include features such as automated ordering, real-time tracking, and reporting capabilities. Examples include platforms that offer cloud-based solutions allowing for multiple users to access and update inventory information simultaneously from various locations on the construction site.
Such software can also generate reports on material usage, waste, and cost, providing valuable insights for optimizing future projects. These platforms often incorporate features such as alerts for low stock levels, ensuring that materials are ordered promptly, preventing delays.
Benefits and Limitations of Technological Solutions
- Building Information Modeling (BIM):
- Benefits: Improved accuracy in material tracking, enhanced collaboration among stakeholders, reduced material waste, improved cost estimation.
- Limitations: Requires skilled professionals to implement and maintain, can be expensive to implement, data accuracy depends on the quality of input data.
- Barcode and RFID Technologies:
- Benefits: Real-time inventory tracking, improved accuracy of inventory counts, reduced manual effort, enhanced security.
- Limitations: Initial investment costs, potential for tag damage or malfunction, requires specialized equipment and software.
- Software Solutions:
- Benefits: Centralized data management, automated reporting, improved communication and collaboration, enhanced efficiency.
- Limitations: Implementation costs, integration challenges with existing systems, reliance on technology and internet connectivity, potential for data breaches.
Risk Management and Inventory in Real Estate Construction
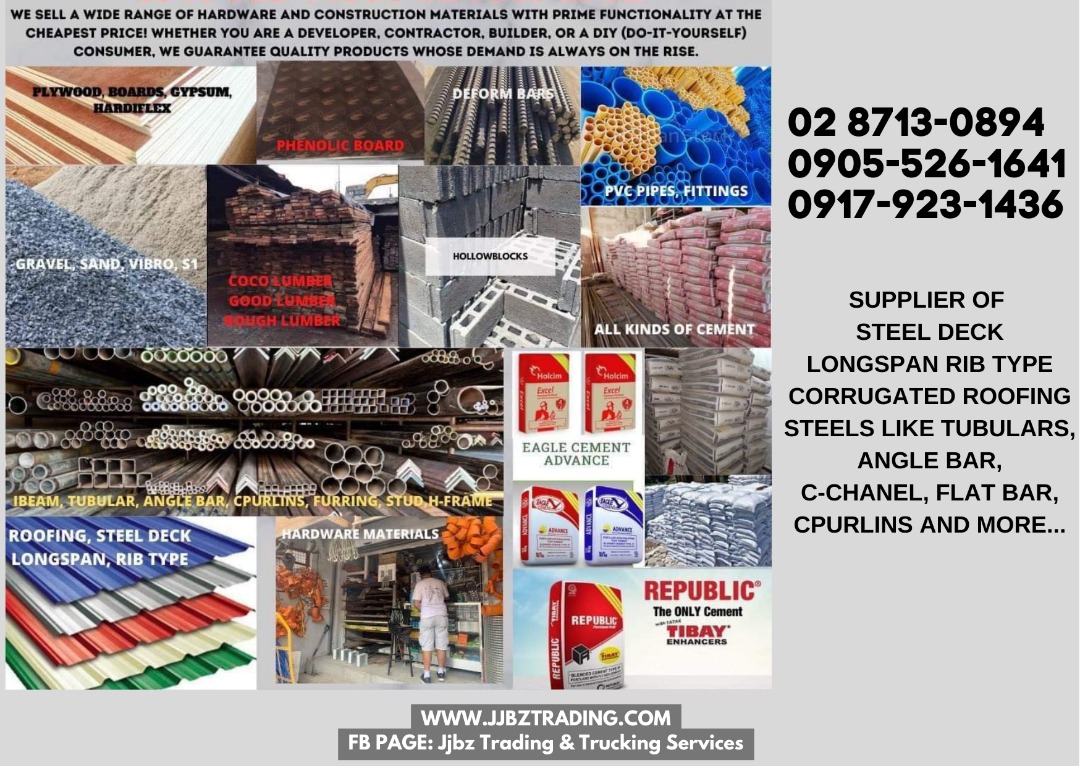
Effective inventory management is crucial for mitigating risks in real estate construction. Inadequate management can lead to significant project delays, cost overruns, and ultimately, project failure. This section explores the potential risks, mitigation strategies, and the role of insurance in protecting against these challenges.
Potential Risks Associated with Inadequate Inventory Management
Poor inventory control introduces numerous risks to construction projects. Material shortages, stemming from inaccurate forecasting or unreliable suppliers, can cause significant delays in the construction schedule. This delay directly translates into increased labor costs, extended financing periods, and potential penalties for late completion. Conversely, overstocking ties up valuable capital in materials that may become obsolete, damaged, or simply unnecessary due to design changes.
This leads to wasted resources and financial losses. Furthermore, poor tracking can result in theft or loss of materials, adding further cost and disruption. The lack of real-time visibility into inventory levels hampers accurate project planning and forecasting, increasing the likelihood of unforeseen problems and escalating costs.
Mitigation Strategies for Inventory-Related Risks
Implementing robust inventory management strategies is essential for mitigating the risks Artikeld above. This involves several key steps. First, accurate forecasting of material needs based on detailed project plans and historical data is critical. Second, establishing strong relationships with reliable suppliers who can provide timely delivery and quality assurance is crucial. Third, implementing a comprehensive inventory tracking system, either manual or automated, allows for real-time monitoring of stock levels and identification of potential shortages.
Regular physical inventory checks should be conducted to verify the accuracy of records. Furthermore, establishing clear procedures for material handling, storage, and security minimizes the risk of loss or damage. Finally, implementing a just-in-time (JIT) inventory system can reduce storage costs and minimize the risk of obsolescence, although this requires exceptionally precise forecasting and reliable supplier relationships.
The Role of Insurance in Managing Inventory-Related Risks
Insurance plays a vital role in protecting against financial losses associated with inventory risks. Builders risk insurance, for example, covers damage or loss of materials due to unforeseen events such as fire, theft, or vandalism. This insurance helps mitigate the financial impact of such incidents, ensuring the project can continue without significant setbacks. However, it’s important to note that insurance policies typically have specific clauses and limitations, and comprehensive coverage requires careful consideration of potential risks and appropriate policy selection.
The cost of insurance should be factored into the overall project budget.
Examples of Effective Inventory Management Contributing to Project Risk Reduction
A large-scale residential development project that implemented a sophisticated inventory management system, utilizing barcode scanning and real-time data analysis, experienced a 15% reduction in material waste and a 10% decrease in project completion time compared to previous projects. This demonstrated the direct positive impact of effective inventory control on cost savings and schedule adherence. Another example involves a commercial construction project that used a cloud-based inventory platform to manage materials across multiple sites.
This system allowed for efficient tracking and allocation of resources, preventing delays caused by material shortages and streamlining the procurement process. These examples highlight how proactive inventory management contributes to a significant reduction in overall project risks and enhances the likelihood of successful project delivery.
Legal and Regulatory Aspects of Real Estate Construction Inventory
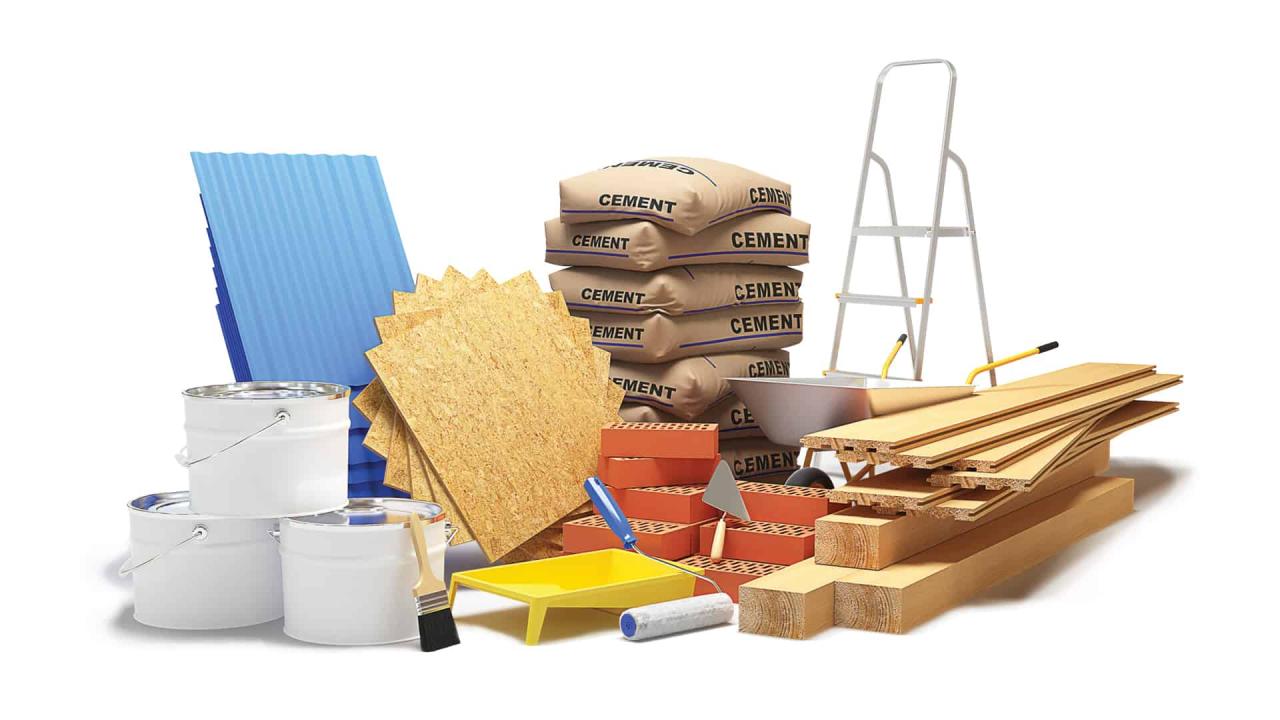
Managing inventory in real estate construction projects necessitates careful consideration of various legal and regulatory frameworks. These regulations aim to ensure worker safety, environmental protection, and the overall quality of constructed buildings. Compliance is crucial for avoiding penalties and maintaining project integrity.
Relevant Legal and Regulatory Frameworks
Numerous laws and regulations influence inventory management within the real estate construction sector. These vary by jurisdiction but commonly encompass building codes, environmental regulations, zoning ordinances, and occupational safety and health standards. Building codes dictate material specifications and quality, impacting the types of materials that can be stored and used. Environmental regulations address the handling and disposal of hazardous materials, requiring specific storage and waste management protocols for inventory.
Zoning ordinances might restrict the storage of certain materials on-site, influencing inventory location and quantity. Occupational safety and health regulations focus on safe storage practices to prevent accidents and injuries during material handling and storage. For example, the Occupational Safety and Health Administration (OSHA) in the United States sets standards for workplace safety, including requirements for the storage of construction materials to prevent hazards like falls or collapses.
Compliance and its Effects on Inventory Practices
Adherence to these regulations significantly shapes inventory practices. It necessitates meticulous record-keeping of material quantities, origins, and handling procedures. Regular inventory audits are crucial to ensure compliance and prevent the use of substandard or prohibited materials. Furthermore, compliance necessitates investment in appropriate storage facilities and equipment to ensure safe and compliant storage. For instance, a construction company might need to invest in specialized containers for hazardous waste, segregated storage areas for different material types, and safety training for personnel handling inventory.
The implementation of robust inventory management systems, incorporating features such as material tracking and traceability, becomes essential.
Implications of Non-Compliance
Failure to comply with relevant regulations can lead to severe consequences. This includes hefty fines, project delays due to stop-work orders, legal disputes, and reputational damage. In extreme cases, non-compliance can result in project cancellation and even criminal charges. For example, using substandard materials that don’t meet building codes could lead to structural issues, resulting in costly repairs or even building collapse.
Improper disposal of hazardous materials could lead to environmental contamination and significant legal repercussions. The use of materials without proper certification could invalidate building permits and lead to legal challenges.
Key Legal and Regulatory Requirements Related to Construction Materials and Inventory
Regulation Type | Specific Requirement | Impact on Inventory | Non-Compliance Penalty |
---|---|---|---|
Building Codes | Material specifications (e.g., fire resistance, strength) | Requires storage of approved materials only; regular quality checks | Project delays, fines, legal action |
Environmental Regulations | Proper disposal of hazardous waste (e.g., asbestos, lead paint) | Specialized storage and handling procedures; waste tracking | Significant fines, environmental remediation costs, legal action |
Occupational Safety and Health (OSHA) | Safe storage practices (e.g., preventing falls, fire hazards) | Secure storage areas, proper material stacking, employee training | Fines, workplace shutdowns, injuries |
Zoning Ordinances | Restrictions on material storage on-site | Limits on inventory quantity and location; off-site storage may be required | Fines, stop-work orders |
Sustainability and Inventory Management in Real Estate Construction
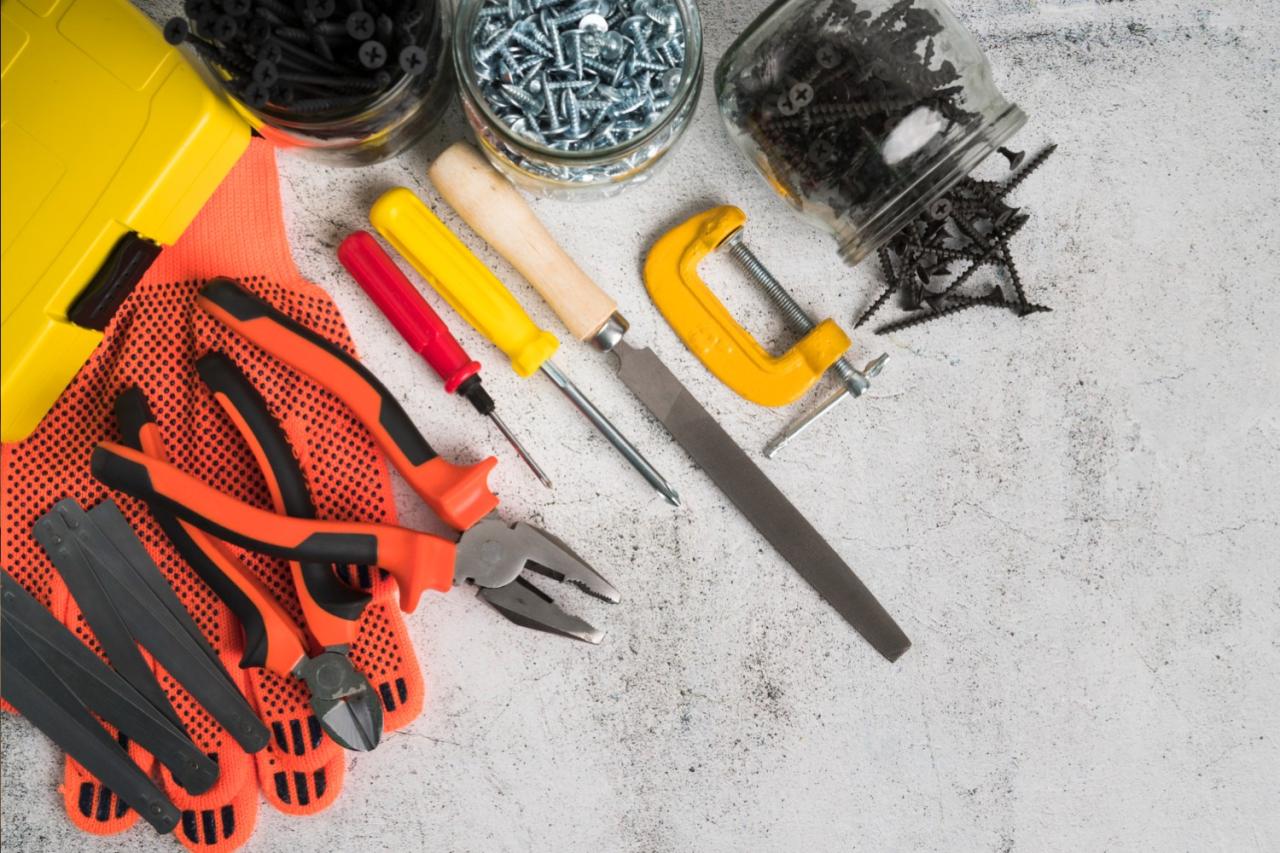
Sustainable inventory management is crucial for environmentally responsible real estate construction. Inefficient practices lead to significant waste and environmental damage, impacting project costs and the overall sustainability of the built environment. This section explores strategies for minimizing waste, promoting sustainable practices, and aligning inventory management with green building standards.
Environmental Impact of Inefficient Inventory Management
Inefficient inventory management in construction significantly contributes to environmental problems. Excess materials end up in landfills, contributing to greenhouse gas emissions and depleting natural resources. The transportation of materials generates further carbon emissions, especially when materials are unnecessarily moved or stored for extended periods. Waste from inaccurate ordering and poor material tracking also contributes to pollution and resource depletion.
For example, a project that overestimates its need for lumber by 20% results in a considerable amount of excess wood that ends up being disposed of, representing a significant environmental cost and lost financial resources. The improper disposal of construction waste, such as concrete, asphalt, and drywall, also leads to soil and water contamination.
Strategies for Minimizing Waste and Promoting Sustainable Practices
Minimizing waste and promoting sustainability requires a multi-pronged approach to inventory management. This includes implementing accurate forecasting techniques to optimize material ordering, utilizing Building Information Modeling (BIM) for precise quantity takeoffs, and employing just-in-time delivery systems to reduce storage needs and material spoilage. Implementing robust tracking systems allows for real-time monitoring of material usage and identification of potential waste.
Prioritizing the use of recycled and locally sourced materials reduces transportation emissions and supports sustainable manufacturing. Furthermore, encouraging material reuse and repurposing within the project, or even on subsequent projects, further minimizes waste. For instance, reclaiming wood from demolition projects for use in new structures can significantly reduce the demand for newly harvested timber.
Sustainable Inventory Management and LEED Certification
Sustainable inventory management practices directly contribute to achieving LEED (Leadership in Energy and Environmental Design) certification or other green building standards. LEED points can be earned through strategies such as waste reduction and diversion, the use of recycled content materials, and efficient material management. Accurate inventory tracking and waste reduction documentation provide the evidence needed to demonstrate compliance with LEED requirements.
For example, a project that meticulously tracks its waste and demonstrates a high percentage of diverted waste can earn significant points towards LEED certification. The use of sustainably sourced wood or recycled steel can also contribute to LEED points, demonstrating a commitment to environmental responsibility.
Checklist for Incorporating Sustainable Practices into Inventory Management, Business inventory for real estate construction
A comprehensive checklist ensures the integration of sustainable practices into the inventory management process. This should be a living document, regularly reviewed and updated based on project performance and industry best practices.
Step | Action |
---|---|
1 | Conduct a thorough material analysis to identify opportunities for waste reduction and the use of sustainable materials. |
2 | Implement accurate forecasting and ordering systems to minimize overstocking and understocking. |
3 | Utilize BIM for precise quantity takeoffs and material tracking. |
4 | Employ just-in-time delivery systems to reduce storage needs and material spoilage. |
5 | Establish a robust waste management plan, including material reuse and recycling programs. |
6 | Regularly monitor and report on material usage, waste generation, and sustainability performance. |
7 | Prioritize the use of recycled and locally sourced materials. |
8 | Document all sustainability efforts for LEED certification or other green building standards. |
Summary
Successfully navigating the complexities of business inventory in real estate construction requires a multifaceted approach. By implementing effective strategies, leveraging technological advancements, and adhering to legal and regulatory requirements, construction firms can significantly improve project outcomes. Optimizing inventory management not only reduces costs and mitigates risks but also contributes to environmentally responsible practices and overall project success. The key takeaway is that proactive and well-informed inventory management is not merely a cost-saving measure but a cornerstone of efficient and sustainable real estate development.
Quick FAQs
What are the common causes of inventory discrepancies in real estate construction?
Common causes include inaccurate tracking, theft or loss, damage during transport or storage, and poor communication between teams.
How can I prevent material obsolescence in my inventory?
Implement a robust forecasting system, prioritize fast-moving items, and consider using just-in-time inventory strategies for slow-moving materials.
What insurance coverage is essential for construction inventory?
Essential coverage includes builder’s risk insurance, which protects against loss or damage to materials and equipment during construction.
How does effective inventory management contribute to LEED certification?
Effective inventory management reduces waste and promotes sustainable material usage, contributing to LEED points in various categories, such as waste management and sustainable procurement.